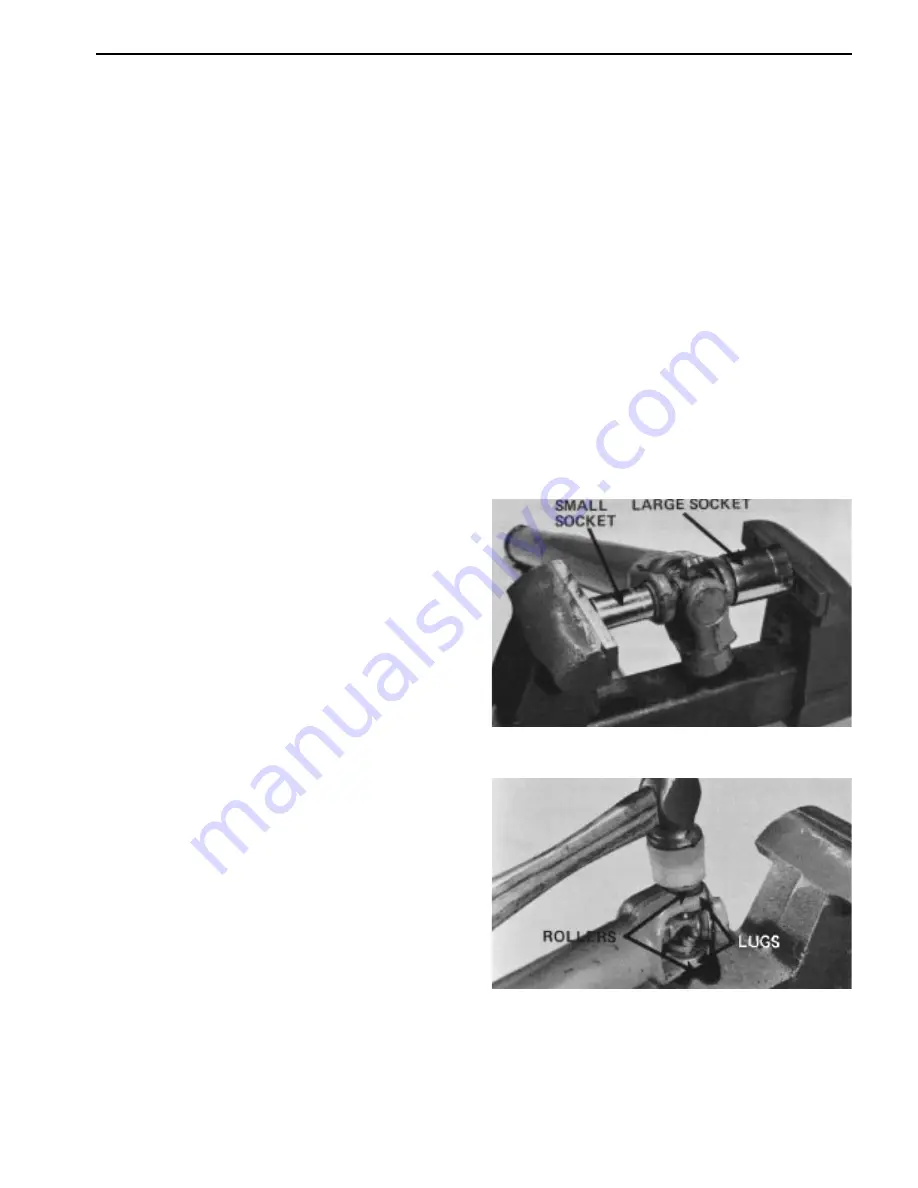
PTO Drive Shaft Universal Joint Replacement (Fig. 16, 17)
1 Remove the P.T.O. drive shaft.
2. Separate the two sections of the P.T.O. shaft.
3. Mount the section to be repaired in a vise so that the
U-joint is pointing upward.
NOTE: If the splined portion is to be repaired, protect
the splines from vise damage with wooden blocks, vise
jaw cushions, etc.
4. Use two thin screwdrivers to remove the “C” shaped
snap ring from each of the U-joint rollers (located inside
of each yoke). Remove the shaft from the vise.
5. The vise may now be used as a press by placing a
small socket against one roller and a large socket
against the yoke on the opposite side. As the vise is
closed, the small socket will force the cross to push the
opposite roller partway into the large socket.
6. When the roller is forced partway out, grasp the roller
and strike the yoke to complete removal. Do not spill the
needle bearings.
7. Follow steps 5 and 6 to complete the removal of the
U-joint from the P.T.O. shaft.
8. When replacing the U-joint, pack the roller bearings
with the recommended lubricant (multi-purpose
grease). Pack carefully to eliminate trapped air. Install
seals.
9. Start one of the rollers in the yoke. Insert from the
bottom with the open side of the roller up to prevent loss
of the needles. Make sure that each roller contains all
of the needles.
10. Insert one of the cross trunnions into the roller. Start
the other roller making certain it slips over the trunnion.
11. When partially seated, place the two rollers between
the vise jaws. Squeeze until FLUSH with the yoke. Stop
when flush; do not over-tighten.
12. Tap one of the rollers (use a brass punch the full
width of the roller) through the yoke until the snap ring
can be inserted. Insert the snap ring. Use new snap
rings. Make certain the snap ring is seated to full depth.
13. Support the cross and strike the yoke to force the
snap ring against the inner face of the yoke. Always seat
the roller in this fashion to prevent improper centering
of the cross.
14. Install the other snap ring or rings and seat the rollers
against the rings.
15. Grease the fitting SLOWLY until grease starts to
show at the seals. Use a low pressure hand grease gun
or a power gun equipped with a pressure relief valve.
Never use a high pressure gun without this adapter as
it is possible to blow the rollers out of the yokes with the
tremendous pressure; seals may also be damaged.
16. Test the action of the assembled joint. It should move
throughout its range without binding. If a slight bind
exists, rap the yoke lugs with a soft hammer. This will
usually free the joint. If it does not, disassemble and
check for the source of the bind.
IMPORTANT: When clamping in the vise, clamp the
solid portion of the U-joint. If the yoke must be
clamped, clamp lightly. Use jaw covers. Avoid
clamping the tube portion of the propeller shaft as
it is thin and easily crushed. Never clamp the tube
portion, even lightly, when it is necessary to ham
mer on the yoke. Support the free end of the propel
ler shaft to remove some of the strain from the
clamped end.
Figure 16
Figure 17
Groundsmaster
®
300 Series
Page 9 - 13
Repairs
Summary of Contents for Groundsmaster 328-D
Page 2: ......
Page 12: ...Torque Specifications Page 2 4 Rev A Groundsmaster 300 Series ...
Page 44: ...Troubleshooting Page 4 16 Groundsmaster 300 Series ...
Page 45: ...Groundsmaster 300 Series Page 4 17 Troubleshooting ...
Page 171: ...Groundsmaster 300 Series Page 6 25 Testing ...
Page 220: ...Repairs Page 7 24 Groundsmaster 300 Series ...
Page 320: ...Troubleshooting Troubleshooting Page 11 4 Groundsmaster 300 Series ...
Page 348: ...Troubleshooting Troubleshooting Page 12 4 Groundsmaster 300 Series ...
Page 379: ...Troubleshooting Groundsmaster 300 Series Page 13 3 Troubleshooting ...
Page 400: ...This page is blank ...
Page 401: ...This page is blank ...