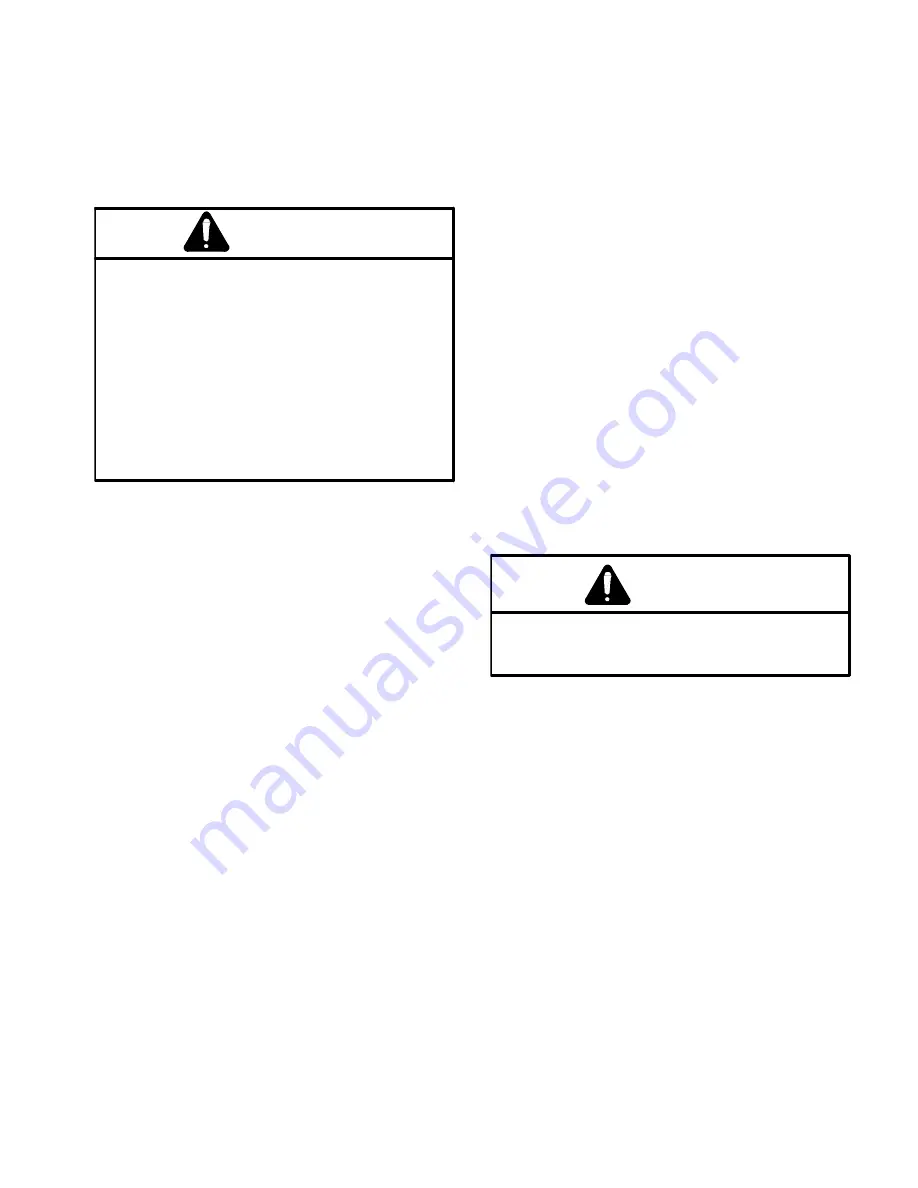
Removal (Fig. 2)
1. Park machine on a level surface, lower cutting deck
(or implement), stop engine, engage parking brake and
remove key from the ignition switch.
2. Drain oil from rear axle (see Traction Unit Operator’s
Manual).
CAUTION
ing other service, use correct blocks, hoists,
and jacks. Make sure machine is parked on a
ments that may interfere with the safe and
block wheels. Use jack stands or solid wood
jack stands, the machine may move or fall,
When changing attachments, tires, or perform-
solid, level surface such as a concrete floor.
Prior to raising machine, remove any attach-
proper raising of the machine. Always chock or
blocks to support the raised machine. If the ma-
chine is not properly supported by blocks or
which may result in personal injury.
3. Chock front wheels and jack up rear of machine.
Support machine with jack stands or solid wood blocks.
4. Remove wheels from rear axle.
5. Remove six (6) socket head screws (item 8) and lock
washers (item 7) that secure driveshaft to bidirectional
clutch on rear axle. Position end of driveshaft away from
clutch.
6. Thoroughly clean around hydraulic hose connec-
tions to steering cylinder. Label hoses for assembly pur-
poses. Disconnect hoses from fittings on steering
cylinder. Put plugs or caps on open hoses and fittings to
prevent contamination of hydraulic system.
7. If machine has rear weight(s) attached to frame, re-
move weight(s).
8. Support rear axle to prevent it from falling. Remove
four (4) flange head screws (item 21) and flange nuts
(item 23) that secure rear axle support to equipment
frame. Lower rear axle and rear axle support from ma-
chine.
9. Locate and retrieve frame spacers (item 22).
10.Remove jam nut (item 19) and thrust washer (item
20) from rear axle pin (item 27) that attaches rear axle
to rear axle support. Remove washer head screw (item
29) that secures flange of axle pin to rear axle support.
11. Remove rear axle pin. Separate rear axle support
from rear axle. Note location and quantity of thrust
washers (items 52 and 53) between axle boss and axle
support.
Installation (Fig. 2)
1. Position rear axle support to axle. Install thrust wash-
ers (items 52 and 53) between axle boss and axle sup-
port to minimize clearance.
2. Install rear axle pin (item 27) to secure axle to rear
axle support. Install thrust washer (item 20) and jam nut
(item 19) onto pivot pin. Torque jam nut from 90 to 120
ft–lb (122 to 163 N–m). Secure pivot pin to axle support
with washer head screw (item 29).
3. Position axle and axle support under machine with a
jack. Place frame spacers (item 22) on axle support.
Raise assembly to machine frame and align mounting
holes of axle support, frame spacers and machine
frame.
4. Secure rear axle support to frame with four (4) flange
head screws (item 21) and flange nuts (item 23).
5. Remove plugs and caps from steering cylinder hy-
draulic hoses and fittings. Connect hoses to fittings on
steering cylinder.
6. Position end of driveshaft to bidirectional clutch on
rear axle. Secure driveshaft to clutch with six (6) socket
head screws (item 8) and lock washers (item 7).
Failure to maintain proper wheel lug nut
torque could result in failure or loss of wheel
WARNING
and may result in personal injury.
7. Install wheels to axle. Torque wheel lug nuts from 45
to 55 ft-lbs. (61 to 75 Nm).
8. Lower machine to ground.
9. If any rear weight(s) were removed from machine, at-
tach weight(s) to machine.
10.Fill axle and input gearbox with SAE 80W–90 weight
gear lube (see Traction Unit Operator’s Manual).
11. Check bidirectional clutch lubricant level (see Trac-
tion Unit Operator’s Manual). Adjust if necessary.
12.Start engine and check for component interference
as steering wheel is turned from lock to lock. Also, check
for any hydraulic leaks.
13.Check rear wheel toe–in and adjust if necessary (see
Traction Unit Operator’s Manual).
14.Check adjustment of steering stop bolts (see Steer-
ing Stop Bolt Adjustment in the Adjustments section).
Groundsmaster 328–D
Page 10.1 – 5
4WD Rear Axle (Rev. G)
(Dae Dong Axle)
Summary of Contents for Groundsmaster 328-D
Page 2: ......
Page 12: ...Torque Specifications Page 2 4 Rev A Groundsmaster 300 Series ...
Page 44: ...Troubleshooting Page 4 16 Groundsmaster 300 Series ...
Page 45: ...Groundsmaster 300 Series Page 4 17 Troubleshooting ...
Page 171: ...Groundsmaster 300 Series Page 6 25 Testing ...
Page 220: ...Repairs Page 7 24 Groundsmaster 300 Series ...
Page 320: ...Troubleshooting Troubleshooting Page 11 4 Groundsmaster 300 Series ...
Page 348: ...Troubleshooting Troubleshooting Page 12 4 Groundsmaster 300 Series ...
Page 379: ...Troubleshooting Groundsmaster 300 Series Page 13 3 Troubleshooting ...
Page 400: ...This page is blank ...
Page 401: ...This page is blank ...