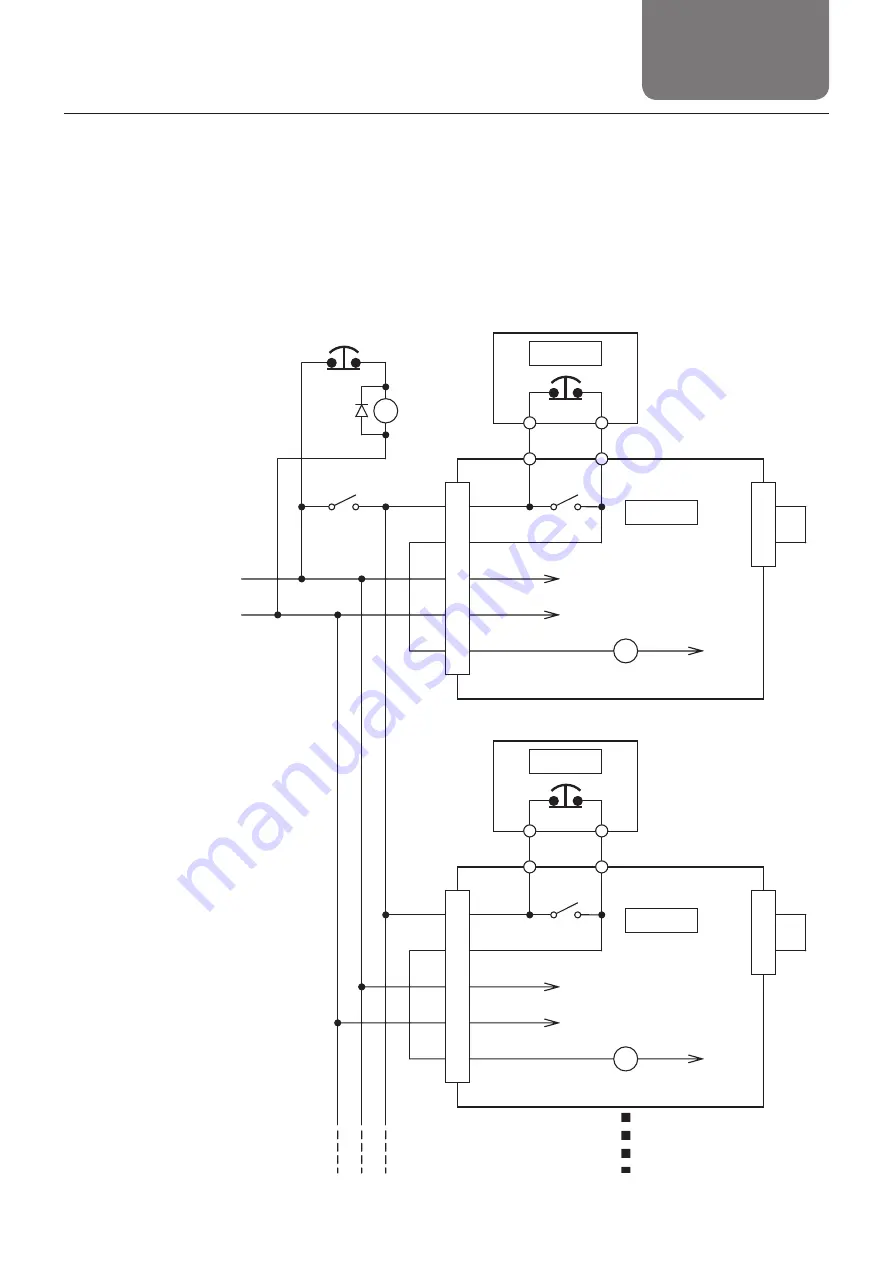
3. Wiring
1.
How to wire
3-9
TSC
Solo emergency stop of TSC (TDO uses)
・
One emergency stop switch can stop all the TSCs urgently.
・
When TDO is connected to any TSC, the emergency stop by TDO stops only the TSC
urgently.
・
Use the external relay CR with the surge absorption diode at 0.1 A or less coil current.
・
When connecting TSC to the network unit TNU, do not wire the CN5 pin number
①
(S1).
(Doing so may cause fault.)
24V
①
S1
②
S2
⑤
24V
⑥
0V
⑦
EMG-
0V
Emergency
stop switch
CN4
CN3
K1
TSC
③
MPO
④
MPI
CN4
X
TDO
0V
①
S1
②
S2
⑤
24V
⑥
0V
⑦
EMG-
0V
CN4
CN3
K1
TSC
③
MPO
④
MPI
CN4
X
CR
CR
TDO
Summary of Contents for TSC Series
Page 98: ...MEMO ...