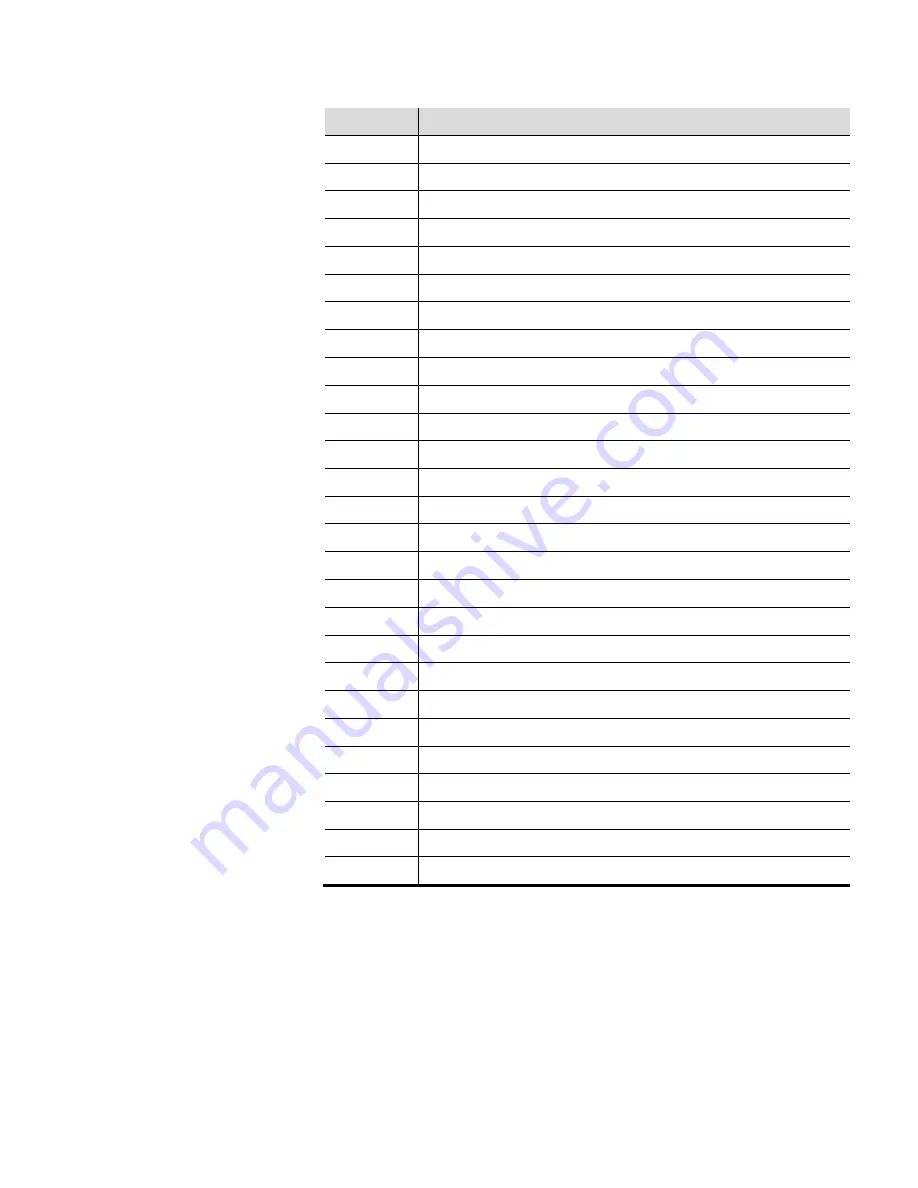
Product Overview
Parts List
2-14 SOLA II User Guide
Thermo Fisher Scientific
P/N
Description
5382
Thermistor IM-1002-A5
27-1108-0
Thermocouple, S type
TE-9934
Transducer, flow
TE-9877
Transducer, pressure assembly
TE-8774
Trigger pak for SOLA II bench, standard unit
TE-8392
Trigger pak for SOLA II bench, Trace unit
30-1025-0
Tube, quartz pyrolyzer furnace, looped
64-1304-0
Tubing, 1/16”, Sulfinert
64-1051-0
Tubing, 1/16" OD x 0.02” ID SS
40-0614
Tubing, 1/16" OD x 0.01" ID, SS, capillary
64-1305-0
Tubing, 1/4", Sulfinert
64-1303-0
Tubing, 1/8”, Sulfinert
40-0611
Tubing, black nylon, 1/4" OD x 0.035” wall
40-0609
Tubing, FEP, 0.125” OD x 0.062” ID, high temperature
40-0600
Tubing,1/8” OD x 0.085” ID, 0.020, 304SS
97-1591-1
Two-year spare parts kit, Dinfa valve, liquid phase applications
97-1591-2
Two-year spare parts kit, Valco valve, gas phase applications
97-1591-0
Two-year spare parts kit, Valco valve, liquid phase applications
75-1343-0
Valve head, Valco, 10-port
75-1333-0
Valve head, Valco, 6-port
45-1837-0
Valve, 3-way, air operated
75-1335-0
Valve, Dinfa, 8-port, 1.2 µl, complete assembly
45-1823-0
Valve, Valco rotor 1.0 µl, 6-port
45-1835-0
Valve, Valco rotor, 10-port
75-1340-0
Valve, Valco, 10-port, complete assembly
75-1332-0
Valve, Valco, 6-port, 1µl, complete assembly with rotor
45-1235-0
Valve, 3-way ball, tube to tube, 316SS, TFE seat, 1/8” port size
Summary of Contents for SOLA II
Page 2: ...SOLA II Sulfur Online Analyzer User Guide P N 90 1307 0 Revision AB...
Page 4: ......
Page 6: ......
Page 12: ......
Page 16: ......
Page 38: ......
Page 50: ......
Page 84: ......
Page 92: ......
Page 150: ......
Page 160: ......
Page 168: ......
Page 188: ......
Page 194: ......
Page 198: ......
Page 200: ...Thermo Fisher Scientific SOLA II User Guide M 2 THIS PAGE INTENTIONALLY BLANK...