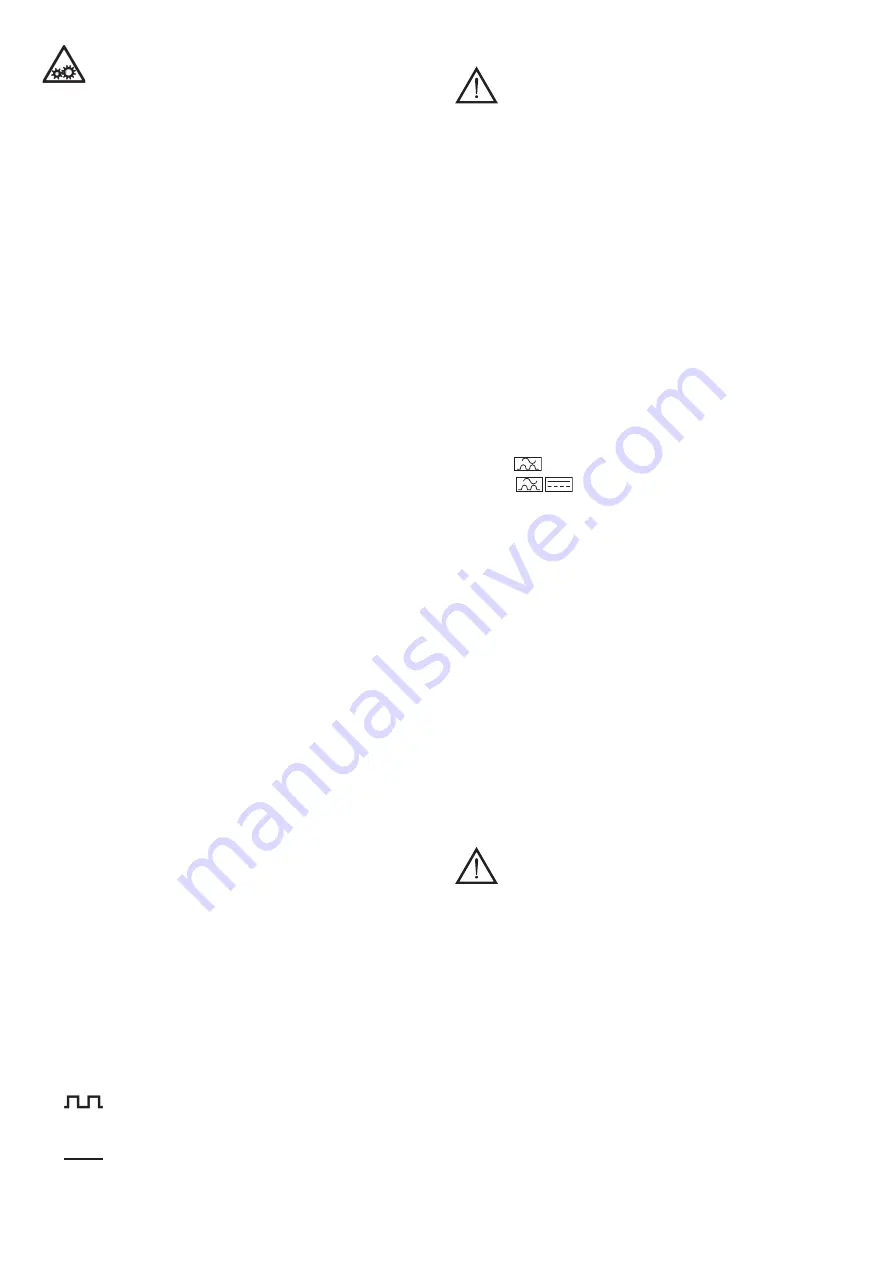
- 6 -
SAFEGUARDS AND SHIELDS
The safeguards and mobile parts of the spot welder casing must be in position,
before connecting it to the power supply.
WARNING! Any manual intervention on the accessible mobile parts of the spot
welder, for example:
- Replacement of or maintenance on the electrodes
- Adjustment of the arm or electrode positions
MUST BE CARRIED OUT WITH THE SPOT WELDER SWITCHED OFF AND
DISCONNECTED FROM THE ELECTRIC AND PNEUMATIC (if present) POWER
SUPPLY.
MAIN SWITCH LOCKED AT “O” WITH LOCK CLOSED AND KEY REMOVED in the
models with PNEUMATIC CYLINDER movement).
STORAGE
- Place the machine and its accessories (with or without packaging) in closed
areas.
- The relative humidity of the air must not exceed 80%.
- The environmental temperature must be between -15°C and 45°C.
If the machine has a water cooling unit and the environmental temperature is
lower than 0°C: add the indicated antifreeze liquid or completely empty the
hydraulic circuit and the water tank.
Always use suitable measures for protecting the machine from humidity, dirt
and corrosion.
2. INTRODUCTION AND GENERAL DESCRIPTION
2.1 INTRODUCTION
Portable spot-welder for resistance welding.
The series consists of 3 models:
- 5.8kA:
Portable spot-welder with electronic timer. Used for precision spot-welding with
electronic control of spot-welding time, and electrode force adjustment. Spot
welding capacity on low carbon steel sheet (standard arms) up to 1+1 mm thick.
- 6.9kA (230V):
Portable spot-welder with digital microprocessor control.
The most important properties managed by the control panel are:
- Selection of the thickness of the sheet to be spot-welded.
- Correction of spot-welding time.
- Possibility of enabling pulsed welding current.
- Adjustment of spot-welding force.
- Spot welding capacity on low carbon steel sheet (standard arms) up to 2+2 mm
thick.
- 6.9kA (400V):
Portable spot-welder with digital microprocessor control.
The same features as the 6.9kA (230V) model, but operating with a power supply
voltage of 400V(380V-415V).
2.2 STANDARD ACCESSORIES:
The standard spot-welder includes 120 mm arms and standard electrodes.
2.3 OPTIONAL ACCESSORIES
- Electrode arm pairs of different lengths and/or shapes, also in kits of several pairs.
- Trolley for arms: to carry the spot-welder and accessories.
3. TECHNICAL DATA
3.1 RATING PLATE (FIG. A)
The main data relating to use and performance of the spot-welder are summarised on
the rating plate and have the following meanings:
1- Number of phases and frequency of power supply.
2- Power supply voltage.
3- Rated mains power with 50% duty cycle.
4- Mains power with permanent running (100%).
5- Maximum loadless voltage over electrodes.
6- Maximum current when electrodes are shorted.
7- Maximum electrode force:
8- Current to secondary when running permanently (100%).
Note: The rating plate shown is an example to show the meaning of the symbols and
numbers; the exact values of the technical specifications for your spot-welder can be
found on the rating plate of the spot-welder itself.
3.2 OTHER TECHNICAL DATA
General specifications TAB. 1.
Weight of the spot-welder TAB. 7.
4. DESCRIPTION OF THE SPOT-WELDER
4.1 PRINCIPAL COMPONENTS AND ADJUSTMENTS (FIG.B)
1- Electrode force adjustment screw.
2- Left/right hand positionable handgrip.
3- Hole for eyebolt if used.
4- Movable welding arm.
5- Fixed welding arm.
6- Power supply cable.
7- Rating plate.
8- Microswitch.
9- Spot-welding time adjustment (only on 5.8kA models (
FIG. B1)
) ; for 6.9kA models
see 4.2:
CONTROL PANEL.
10- Spot-welding lever.
4.2 CONTROL PANEL (only for 6.9kA models) (FIG. C)
1- Key for correcting spot-welding time.
adjusts spot-welding time with respect to the factory default setting.
2- Key for selecting sheet thickness.
selects the thickness of the sheet to be welded.
3- Key for selecting spot-welding mode.
: The welding current is pulsed.
Making this selection will improve spot-welding capacity on high yield
point sheets or on sheets with special protective film. The length of
the pulse is automatic and requires no regulation.
: Normal spot welding.
4- LED’s for indicating triggering of thermal safeguard.
The two LED’s flash alternately, the remaining LED’s are off, indicating that
the spot-welder is shut down due to overheating; reset is automatic when the
temperature returns within the allowed limits.
5. INSTALLATION
WARNING! CARRY OUT ALL INSTALLATION OPERATIONS AND
ELECTRICAL AND PNEUMATIC CONNECTIONS WITH THE SPOT-WELDER
COMPLETELY SWITCHED OFF AND DISCONNECTED FROM THE POWER
SUPPLY OUTLET. THE ELECTRICAL AND PNEUMATIC CONNECTIONS MUST
BE MADE ONLY AND EXCLUSIVELY BY AUTHORISED, SKILLED PERSONNEL.
5.1 PRELIMINARY OPERATIONS
Unpack the spot-welder, assemble the separate parts included in the package.
5.2 LIFTING THE SPOT-WELDER
WARNING: None of the spot-welders described in this handbook have lifting devices;
when required attach an eyebolt to suspend the spot-welder using the hole made for
this purpose
(FIG. F (2)), take care to insert the threaded bolt to a depth of no
more than 8mm
.
5.3 POSITION
The installation area must be sufficiently large and without obstacles, suitable for
ensuring safe access to the control panel and to the work area (electrodes).
Ensure that there are no obstacles near the cooling air inlets and outlets and that no
conductive dusts, corrosive vapour, humidity, etc. can be sucked in.
Position the spot welder on a flat surface of homogeneous and compact material
that is suitable for supporting its weight (see “technical data”) to avoid the danger of
toppling or dangerous movements.
5.4 CONNECTION TO THE MAIN POWER SUPPLY
5.4.1 Warnings
- Before making any electrical connection, check the rating plate data on the spot
welder to make sure they correspond to the voltage and frequency of the available
power supply where the machine is to be installed.
- The spot welder must be connected only and exclusively to a power supply with the
neutral conductor connected to earth.
- To guarantee protection against any direct contact always use the differential
switches indicated below:
- Type A (
) for single-phase machines;
- Type B (
) for three-phase machines;
- In order to satisfy the requirements of the EN 61000-3-11 (Flicker) standard we
recommend connecting the spot welder to interface points of the main power
supply that have an impedance of less than Zmax = 0.179 ohm.
- The spot welder does not fall within the requisites of IEC/EN 61000-3-12 standard.
Should it be connected to a public mains system, it is the installer’s responsibility
to verify that the spot welding machine itself is suitable for connecting to it (if
necessary, consult the distribution network company).
5.4.2 Plug and socket
Connect a normalized plug to the power cable (3P+T: only 2 poles are used for the
400V INTERPHASE SYSTEM connection; 2P+T: 230V INTERPHASE connection)
of appropriate capacity and prepare a power supply outlet fitted with fuses or an
automatic circuit-breaker; the corresponding earth terminal should be connected to
the (yellow-green) earth conductor of the power supply.
The power supply connection and the number of poles on the plug, which
depend on the distribution system and the power supply voltage of your spot-
welder, should correspond with the indications given in the tables (TAB. 2; 3;
4; 5).
The capacity of the plug and specifications of the fuses and circuit-breaker are given
in the tables TAB. 1 and TAB. 7.
Should more than one spot-welder be installed, distribute the power cyclically among
the three phases in order to obtain amore balanced load; e.g.
230V spot-welders:
Spot-welder 1: power supply L1-N.
Spot-welder 2: power supply L2-N.
Spot-welder 3: power supply L3-N.
etc.
400V spot-welders:
Spot-welder 1: power supply L1-L2.
Spot-welder 2: power supply L2-L3.
Spot-welder 3: power supply L3-L1.
etc.
WARNING! Failure to observe the rules given above will invalidate the
(class I) safety system provided by the manufacturer causing serious risks to
people (e.g. electric shock) and objects (e.g. fire).
6. (SPOT) WELDING
6.1 PRELIMINARY OPERATIONS
Before carrying out any spot-welding operation, it is necessary to carry out a series
of checks and tests with the spot-welder disconnected from the main power supply.
1- Ensure that the electrical connections are correct, in accordance with the above
instructions.
2- Electrode force and alignment
- lock the lower electrode securely in the most suitable position for the job to be
done,
- loosen the fastening screw on the top electrode so that it is able to slide in the
hole in the arm,
- between the electrodes place a shim with the same thickness as the sheets to
be spot-welded,
-
FIG. D
close lever 2 until the arms are parallel and the electrode tips coincide;
insert screw 3 (d.M6) which is supplied into hole 1 and tighten it to lock the
lever in a suitable position for adjusting the electrode force,
- lock the top electrode in the correct position, tightening the screw securely,
- regulate the force exerted by the electrodes during spot-welding FIG.E, by
adjusting the screw (1) fitted for this purpose using the key supplied; the value
of the setting, according to the position of the indicator on the graduated scale,
is shown in
FIG. F
.
TAB. 6
shows the value of the force that can be obtained
with different arm lengths.
Turn it clockwise to increase the force in proportion to the increase in sheet
thickness but make the adjustment so that the clamp is able to close, and
trigger the corresponding microswitch, with very little effort.