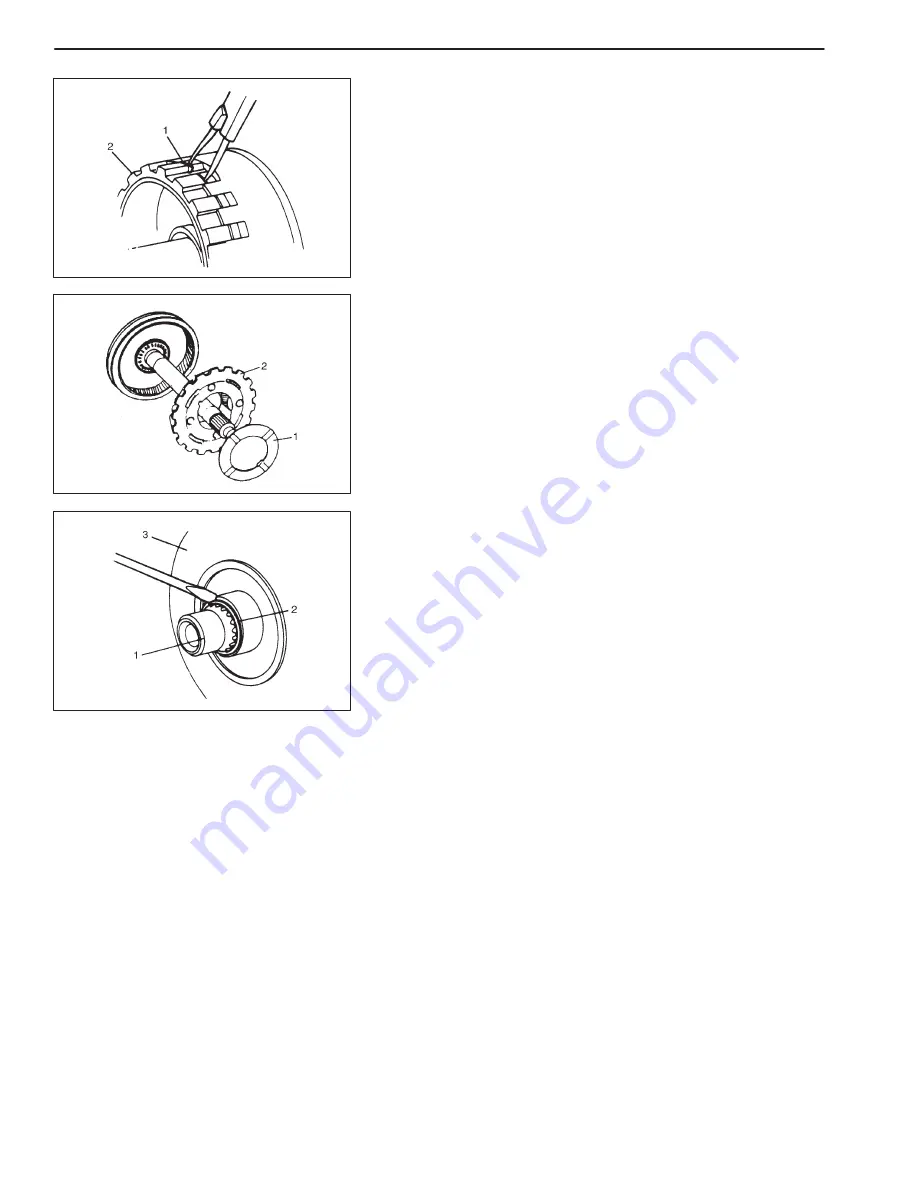
7B1-102
AUTOMATIC TRANSMISSION (4 A / T)
5) After removing retaining ring (1), remove front planetary ring
gear (2), thrust bearing and rear planetary race.
6) Remove rear planetary thrust washer (1), rear planetary gear
(2).
7) After removing retaining ring (2) from inner shaft (1), remove
rear planetary ring gear (3) and thrust bearing assembly.
ASSEMBLY
Assemble components by reversing disassembly procedure and
noting following points.
D
Refer to the first figure of “PLANETARY GEARS AND OUTPUT
SHAFT” when installing each component.
D
Check seal sleeve ring for damage before installation and replace
if damaged.
D
Fit retaining rings into groove securely.