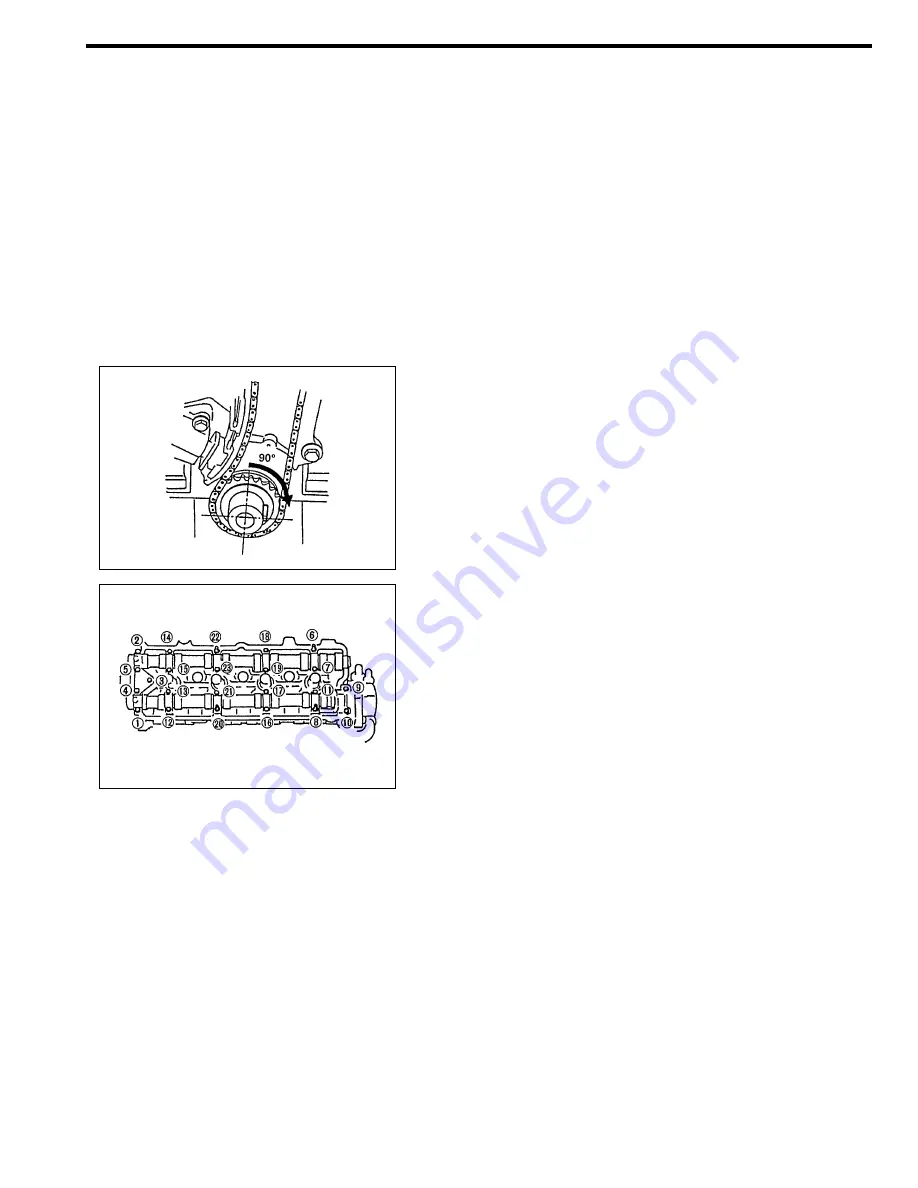
ENGINE MECHANICAL (J20 ENGINE) 6A4-43
REMOVAL
1) Disconnect negative cable at battery.
2) Drain engine oil.
3) Drain coolant.
4) Remove oil pan and oil pump strainer referring to “Oil Pan
and Oil Pump Strainer” in this section.
5) Remove cylinder head cover referring to “Cylinder Head
Cover” in this section.
6) Remove timing chain cover referring to “Timing Chain Cover”
in this section.
7) Remove 2nd timing chain referring to “2nd Timing Chain and
Chain Tensioner” in this section.
8) Remove CMP sensor referring to “CMP Sensor” in Section
6F2.
9) After removing 2nd timing chain, set key on crankshaft in
position as shown by turning crankshaft. This is to prevent
interference between valves and piston.
10) Loosen camshaft housing bolts in such order as indicated in
figure and remove them.
11) Remove camshaft housings.
12) Remove camshafts.
Summary of Contents for Engine 2002 GRAND VITARA SQ625
Page 5: ......
Page 248: ...ENGINE GENERAL INFORMATION AND DIAGNOSIS H25 ENGINE 6 1 107 Fig for Step 4...
Page 274: ...ENGINE GENERAL INFORMATION AND DIAGNOSIS H25 ENGINE 6 1 133 Fig and Table for Step 3...
Page 291: ...6 1 150 ENGINE GENERAL INFORMATION AND DIAGNOSIS H25 ENGINE...
Page 360: ...ENGINE MECHANICAL G16 ENGINE 6A1 69 Main Bearings Crankshaft and Cylinder Block COMPONENTS...
Page 489: ...6A2 114 ENGINE MECHANICAL H25 ENGINE...
Page 572: ...ENGINE MECHANICAL J20 ENGINE 6A4 83 Main Bearings Crankshaft and Cylinder Block COMPONENTS...
Page 591: ...6A4 102 ENGINE MECHANICAL J20 ENGINE...
Page 598: ...ENGINE COOLING 6B 7...
Page 623: ...6B 32 ENGINE COOLING...
Page 693: ...6E1 62 ENGINE AND EMISSION CONTROL SYSTEM G16 J20 ENGINES...
Page 697: ...6E2 4 ENGINE AND EMISSION CONTROL SYSTEM H25 ENGINE ENGINE AND EMISSION CONTROL SYSTEM DIAGRAM...
Page 743: ...6E2 50 ENGINE AND EMISSION CONTROL SYSTEM H25 ENGINE...
Page 814: ...CHARGING SYSTEM 6H 21 Disassembly 70 A and 80 A types...
Page 827: ...6H 34 CHARGING SYSTEM...
Page 833: ...6K 6 EXHAUST SYSTEM...
Page 834: ...Prepared by 1st Ed Dec 2002 Printed in Japan 824...