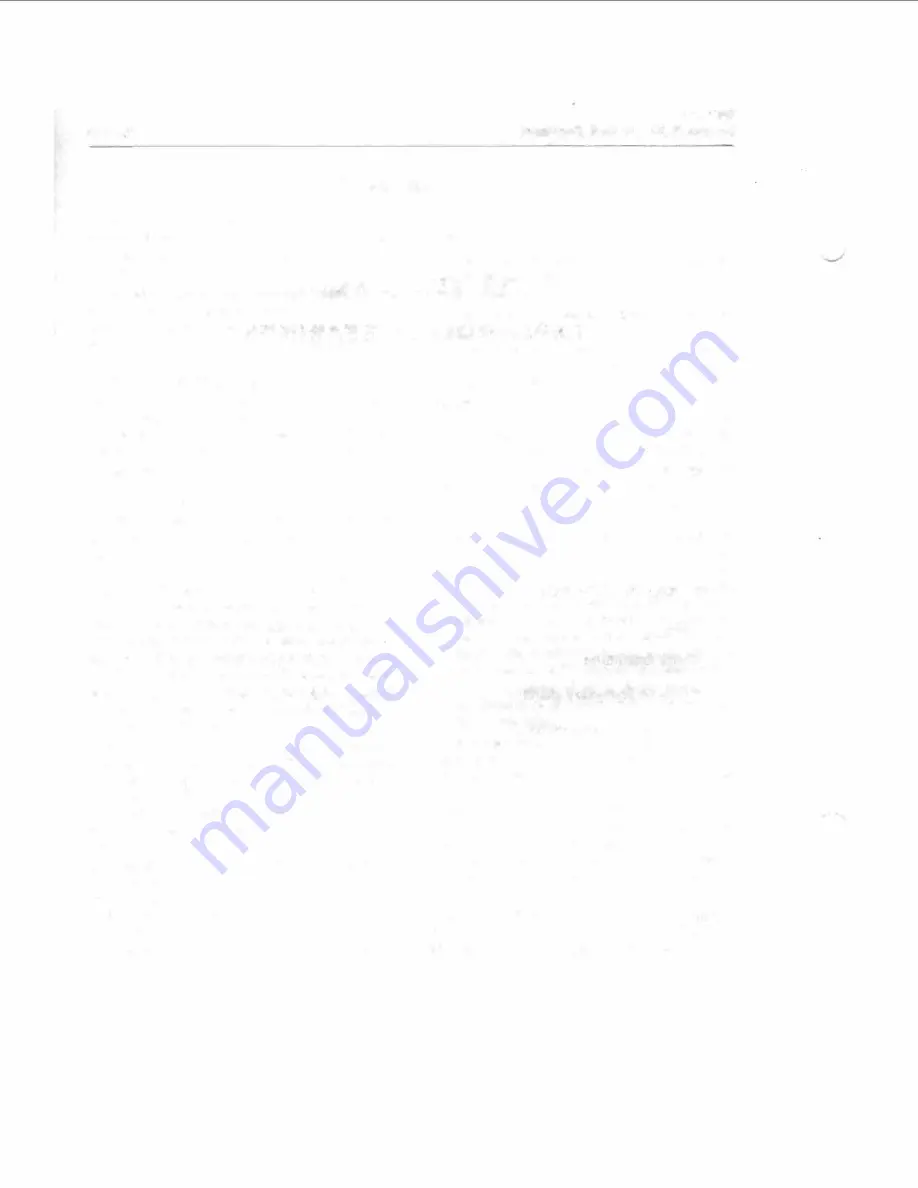
Page 2
WSM.124
Section Q (Oil Seals & Bearings)
OIL SEALS
1. Before fitting, carefully examine the seal and
remove all traces of dirt or grit. This should be
done by wiping carefully with a cloth moistened
with clean oil.
2. Leather Seals Impregnated with Wax.
These seals should not be soaked in oil prior to
fitting as their initial lubrication is provided for
during manufacture. Smear the sealing lips with
clean grease.
3. Synthetic Rubber Oil Seals. These require
no preliminary soaking in oil, it being necessary
only to smear the sealing lips with clean grease.
It is most important when fitting to see that the
sealing lip is not damaged, even by the slightest
scratch and that the garter spring is correctly
located when in position. The seal must be properly
pressed home in the housing recess, with the
lip and the garter spring side to face the oil.
4. Examine the shaft and remove all roughness,
burrs on the edges of keyways, screw threads,
splines, shoulders, etc., over which the sealing lie
is passed. In some cases, where the profile of
a shaft over which a seal must pass during fitting is
liable to cut the sealing lip, it is good practice to
use a fitting sleeve with a lead-on taper and a
diameter a few thousandths of an inch greater than
the shaft. Where necessary a sheet of shim steel,
copper or paper, well greased, should be wrapped
around the shaft to cover such sharp edges as
might damage the seal.
5. In most cases it will be necessary to press the
seal into the housing first and subsequently enter
the shaft. In all cases it must be stressed that as
far as possible the sealing lips should be observed
during fitting to ensure that the garter spring
does not become displaced during the process.
When passing the seal along the shaft, or entering
the shaft in the seal, as the case may be, a slight
rotary motion will assist the operation. Grease
should be applied to the shaft.
6. Do not allow the assembly to rest for any length
of time in an incomplete stage of fitting where It
might cause the weight of the shaft or housing to be
borne by the seal, resulting in damage or distortion
to the latter.
7. Before pressing the seal into the housing the
outside diameter should be lightly coated with a
liquid jointing compound.
8. When pressing a metal cased seal Into the
housing, a firm uniform pressure should be exerted,
preferably by means of an arbor press in combina
tion with a suitable tool for a ram. The diameter of
the tool should be slightly less than the outside
diameter of the seal, e.g. -oos·--015• (·13-·38
mm.) smaller. Only if an arbor press or fitting tool
is not available may the following method be
adopted. By means of gentle hammer blows applied
to an intermediate metal ring, disc or tube of
slightly smaller diameter than that of the seal
(i.e. -oos•--015• smaller), or other protective
piece, drive the seal into place. Care should be
taken to apply blows uniformly around the outside
edge of the seal face, and In no circumstances
should the hammer be applied direct to the seal
casing. Great care must be taken to see that the
seal does not enter the recess In a tilted position.
Note: When pressing metal cased seals Into
position note that one of the three oil entry
holes in the metal face adjacent to the oil must
be
upwards
or at "12 o'clock" position so that
a small quantity of oil Is always retained In
the bottom of the metal casing between the
other two holes.
9. When pressing In a synthetic rubber type seal
(without metal casing), great care is necessary.
The leading edge of the recess Into which it fits In
the housing should be slightly chamfered in order
to provide a lead, and the circumference of the
seal should also be smeared with oil or grease to
avoid cutting its outside diameter during fitting.
This type of seal should only be Inserted by means
of a specially formed tool which is arranged to
bear on the flat face of the seal.
Remember that the efficiency of the unit is
dependent on the efficiency of the Oil Seal.
Therefore treat the latter with care.
.J
Summary of Contents for ALPINE I SERIES: APLINE II SERIES
Page 1: ......
Page 189: ...Fis 21 Ball pin heirht checkinr fixture in position Details of items 1 to 4 In Fig 22...
Page 208: ...Fla 3 Exploded view of rear axle Hypoid Bevel Drive...
Page 220: ...Page 16 WSM 12 f Section G Rear Axle 0 QQ I I I I I t 0 ii 8 ts t 0 Cl 2 i J...
Page 247: ...Page6 WSM 124 Section J Steering N Iii it...
Page 299: ...Page 40 3 6 7 8 Fis 22 Se rvo unit exploded view Sect WSM 124 ion K Brakes 18 419 GZo 21...
Page 413: ..._ PRINTED IN ENGLAND 9Y WREN PRINTING CQ LTD LONDON...