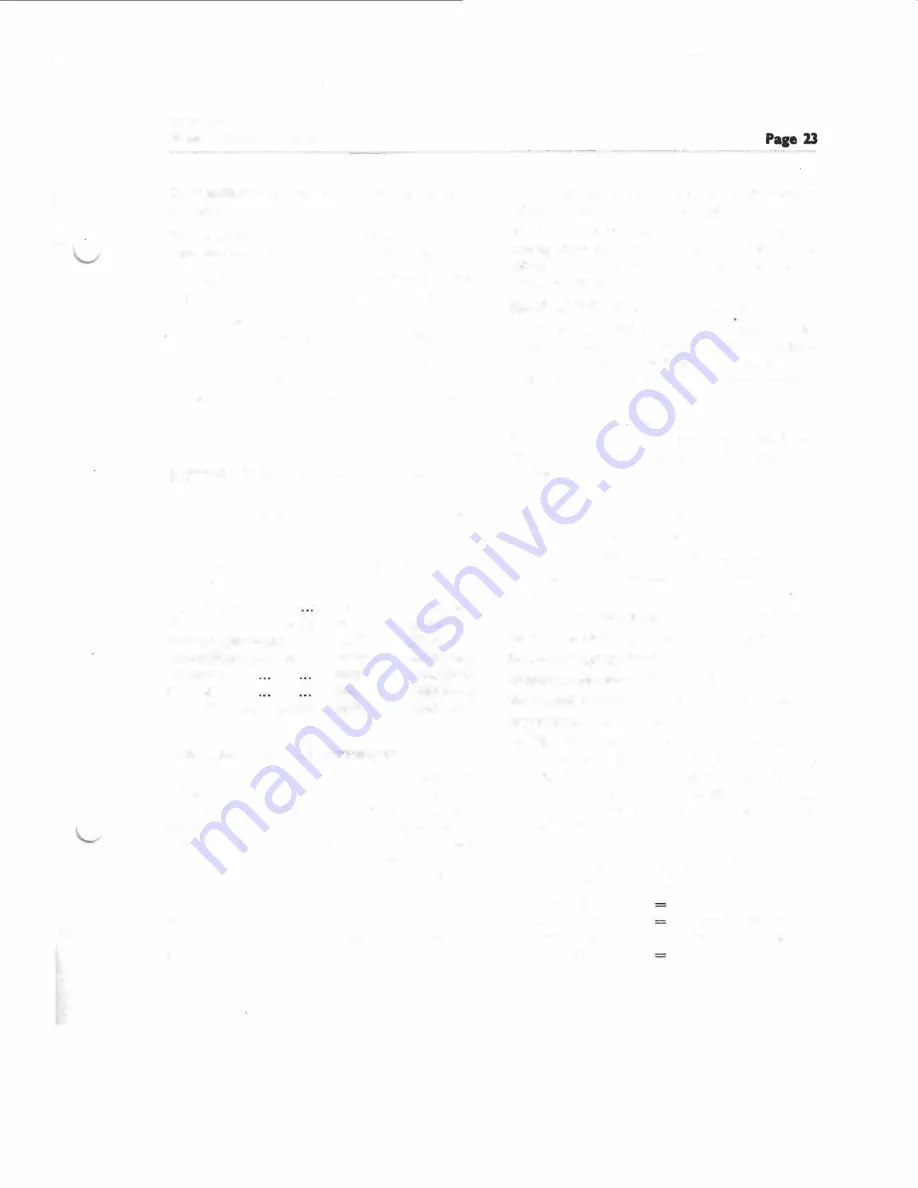
WSM.124
Section G (Rear Axle)
DIFFERENTIAL UNIT-Measurement of
bearings
This requires great accuracy and may present a
little difficulty. Two methods may be used.
1. A clock gauge is suitably mounted on a surface
plate and set to zero on the dummy bearing.
The reading then taken on the actual bearing
be used gives the difference. (See Fig. 8.)
2. In the absence of a clock gauge the difference
between the dummy and the actual bearing
can be ascertained by the use of feeler gauges
and a straight edge, if both are placed on a
surface plate. (See Fig. 8).
DIFFERENTIAL UNIT-Adjustment of
bearings
The foregoing Instructions may appear somewhat
complicated, but no difficulty should be experienced
if the measurements are set out in the manner
indicated, It being essential, of course, to deal with
each side separately, e.g. side "C":-
Dummy Bearing
Gap "A"
... (say)
Whence Dimension "C"
Actual Bearing . . . (say)
Difference
Preload
Total shimming required
·8125
n
·012"
·8245
n
·8130
#
·0115
#
·002"
·0135
6
CHECKING OF ADJUSTMENTS
(20·64 mm.)
(0·30 mm.)
(20·94 mm.)
(20·65 mm.)
(·292 mm.)
(·051 mm.)
(·343 mm.)
If it is considered desirable to check the adjustment
effected by use of jigs, this may be done after the
assembly of the differential unit by lightly coating
the teeth of the crown wheel with a light paste of
red lead and engine oil. The crown wheel should
then be revolved In both directions when the
marking shown In example A, Fig. 7 should be
obtained on the pinion.
Backlash must be measured at three positions
of the crown wheel and must be 0·005-0·009
n
(0·13-0·23 mm.).
A dial indicator gauge must be used; the body of
which Is secured to the differential housing.
The reading Is then taken off the thrust side of a
crown wheel tooth, by means of moving the crown
wheel In each direction. The pinion Is at all times
prevented from rotating.
REAR AXLE-To remove and refit
As described In the foregoing operations, in the
majority of cases It is quite unnecessary to remove
the rear axle from the underframe, but In the event
of this being necessary for any purpose the following
procedure should be adopted:-
Remove rebound straps.
Jack up rear of car so that the road wheels are
clear of the ground and support the underframe
on stands.
Remove road wheels.
Disconnect propeller shaft at rear driver coupling.
Remove rear shock absorbers.
Disconnect handbrake cable from linkage.
Disconnect rear brake hose at 3-way ui:iion on axle
casing.
Protect brake hose from Ingress of foreign matter,
lift hose upwards and tie to prevent loss of fluid.
Remove all spring U-bolts.
Withdraw axle from between springs.
Reassembly Is a reversal of the above operations.
Bleed brakes. (See Section K.)
NOTE:-The rear road springs are rubber
mounted, the rubber being Interposed between
the axle casing brackets and the road springs.
When refitting the axle to the road springs,
the "U" bolts must not be overtightened as
this will destroy the Insulation effect of the
rubber.
The U-bolts must be tightened with a torque
spanner to the torques specified In the Data Section.
Crown Wheel
Rear Gear
Drive Coupling
Companion Flange
Differential Wheel
=
Differential
Side
Gear
Bevel Pinion
Pinion Gear
Summary of Contents for ALPINE I SERIES: APLINE II SERIES
Page 1: ......
Page 189: ...Fis 21 Ball pin heirht checkinr fixture in position Details of items 1 to 4 In Fig 22...
Page 208: ...Fla 3 Exploded view of rear axle Hypoid Bevel Drive...
Page 220: ...Page 16 WSM 12 f Section G Rear Axle 0 QQ I I I I I t 0 ii 8 ts t 0 Cl 2 i J...
Page 247: ...Page6 WSM 124 Section J Steering N Iii it...
Page 299: ...Page 40 3 6 7 8 Fis 22 Se rvo unit exploded view Sect WSM 124 ion K Brakes 18 419 GZo 21...
Page 413: ..._ PRINTED IN ENGLAND 9Y WREN PRINTING CQ LTD LONDON...