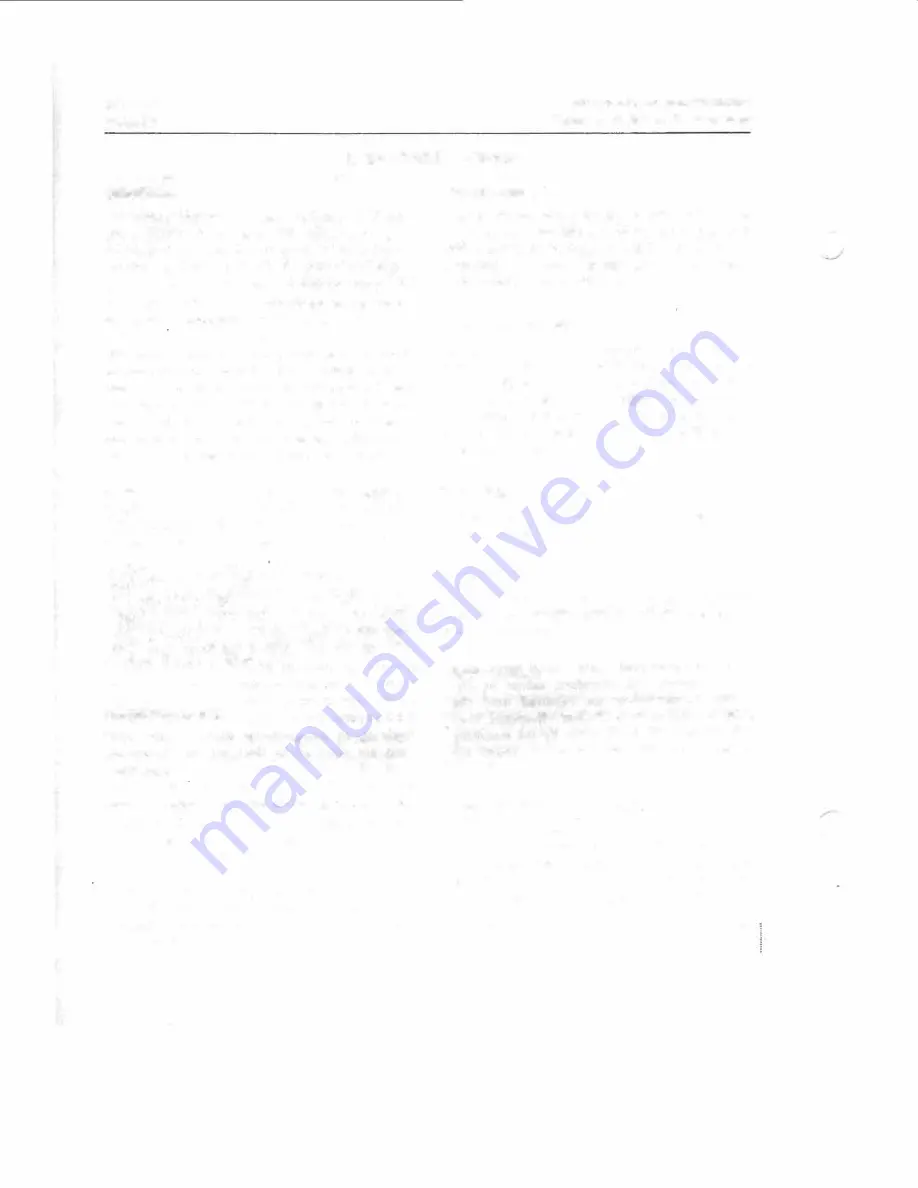
3rd
re-issue
Page 36
ROOTES MAN UAL WSM. 124
Section N (Elec. Equipment)
GENERAL
WINDSCREEN WIPER
SERVICING
The motor and gearbox are mounted on pillars
cast as part of the gearbox. The rotary motion of
the motor armature is converted to the recipro
cating motion of a cable rack by means of a single
stage worm and nylon-gear. reduction drive. A
connecting rod and cross-head In the gearbox
actuate the cable rack.
The flexible cable rack comprises an inner steel
core carrying a wire helix, the whole being run
within rigid connecting tubes between the gearbox
and two wheelboxes. These wheelboxes, house a
toothed wheel pressed on the wiper arm spindles.
The toothed wheel engages with the cable rack,
thus giving an oscillatory motion to the spindle.
A limit switch In the gearbox Is connected in
parallel with a control switch mounted on the
instrument panel. The contacts of this limit switch
are opened once per revolution of the final gear.
When the wiper control switch Is switched to the
"OFF" position the motor continues to drive until
the limit switch contacts are opened. The switch
is adjustable and can be set to alter the position of
the limit switch and this determines the position
at which the wiper blades park.
MAINTENANCE
The gearbox, rack and wheelboxes are packed with
grease during manufacture, and require no periodic
lubrication.
Worn or perished wiper blades should be renewed.
To ensure correct operation under all conditions,
It Is essential that parts of identical pattern to the
original equipment be fitted.
Oil, tar and other stains on the windscreen may be
removed by the judicious use of methylated spirits
(de-natured alcohol). Do not allow silicon or wax
based polishes on the glass.
Poor performance may be due to either mechanical
or electrical faults, not necessarily connected with
the motor Itself. Checks should first be made for
a binding rack, faulty wheelboxes, excessive blade
loading and low supply voltage.
Cable rack and tube
Check for binding by removing the wiper arms and
blades, disconnecting the rack from the motor and
affixing a light spring balance to the motor end of
the rack. A steady pull should give a reading of not
more than 6 lbs. (2·75 kg.). Remove any slight
kinks In the tube and check that It Is not bent to a
radius of less than
9
In. (23 cm.).
Wheel boxes
Check for misalignment, looseness or seizure, and
rectify or renew as necessary.
Blade loading
Windscreen contamination can cause poor perform
ance due to excessive friction. Clean, and renew
blades If necessary.
Supply voltage
With the motor operating, use a high-quality moving
coll voltmeter to check the voltage at the motor.
If below 11 ·5 volts check the battery, switch (by
substitution), wiring and connections. Rectify as
necessary.
Motor-Light running current
Connect a high-quality moving-coil ammeter In
series with the motor supply. With the cable rack
disconnected, switch on the motor and observe the
current and speed of operation. Current should be
2·7-3·"4 amps. after running for one minute.
-rwo types of limit (parking) switch (Refer to
Fig. 3-4).
.J
Summary of Contents for ALPINE I SERIES: APLINE II SERIES
Page 1: ......
Page 189: ...Fis 21 Ball pin heirht checkinr fixture in position Details of items 1 to 4 In Fig 22...
Page 208: ...Fla 3 Exploded view of rear axle Hypoid Bevel Drive...
Page 220: ...Page 16 WSM 12 f Section G Rear Axle 0 QQ I I I I I t 0 ii 8 ts t 0 Cl 2 i J...
Page 247: ...Page6 WSM 124 Section J Steering N Iii it...
Page 299: ...Page 40 3 6 7 8 Fis 22 Se rvo unit exploded view Sect WSM 124 ion K Brakes 18 419 GZo 21...
Page 413: ..._ PRINTED IN ENGLAND 9Y WREN PRINTING CQ LTD LONDON...