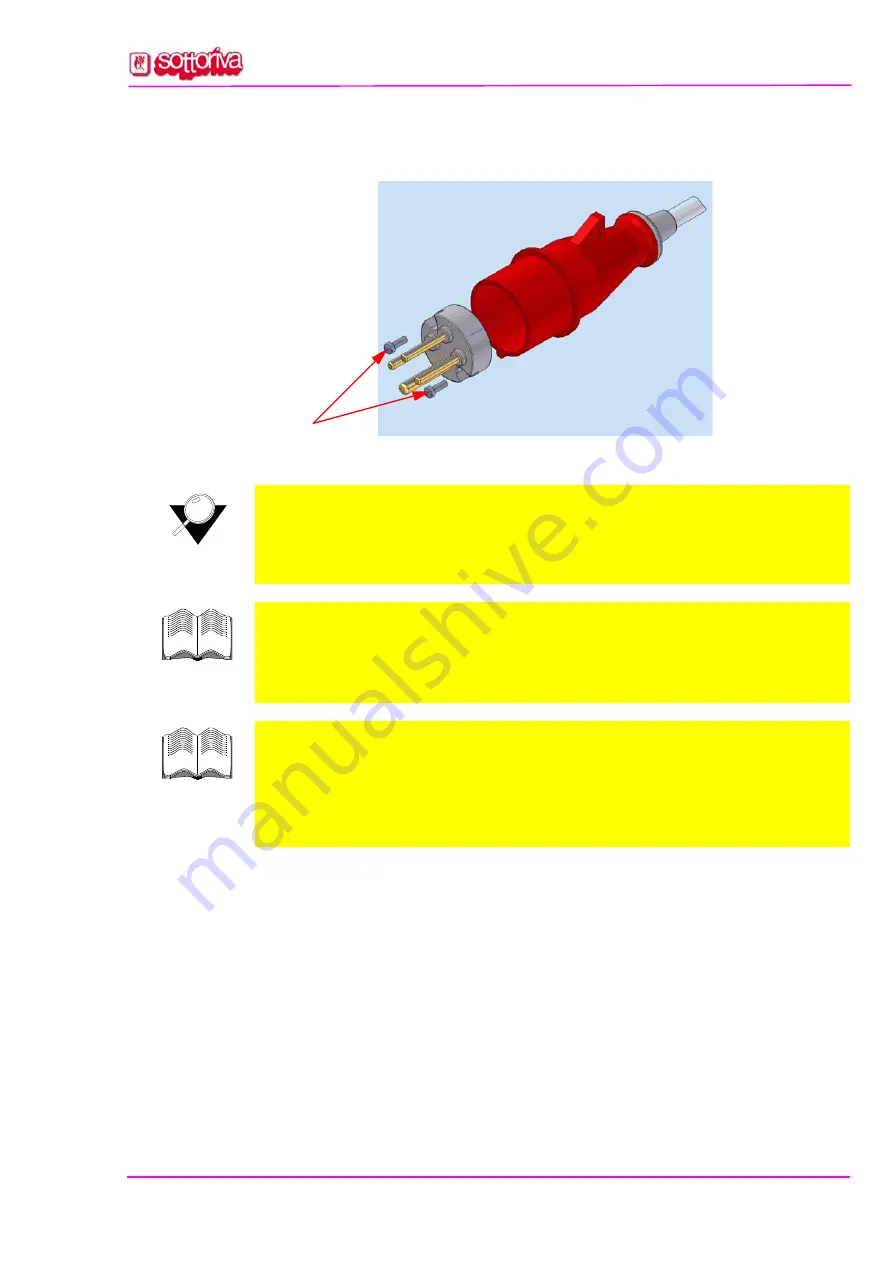
SVP08-0/1/2/3 - Code: 3529.0231.01
Rev. F
dated 02/07/2015
Arc. 66-V
PT
0715
MV
0715
MC
0715
Service
Phone (+39) 0445.595.111
35
8) Close the plug with the screws as shown in
Fig. 9
on page 35.
9) Reconnect the plug to the power socket.
10) Check the direction of rotation again by repeating the steps indicated from point 3).
Fig. 9 Mains plug
Remark
In case of three phase + n ground power connection, there are two
black wires. In this case, either of the black wires may be swapped with the
brown one; If the cable is three-phase + ground there is only one black
wire; swap it with the brown wire.
Warning!
Never disconnect the yellow-green (ground) or blue wires or change their
positions.
Warning!
Unauthorised tampering with or replacement of any part of the machine,
and the use of any accessories, tools or consumables other than those
recommended by the Manufacturer, may constitute a hazard for the
operator or other persons and as such void the Manufacturer’s liability,
whether penal or civil, for any damage to persons and/or property resulting
therefrom.
Summary of Contents for SVP08-0
Page 2: ......