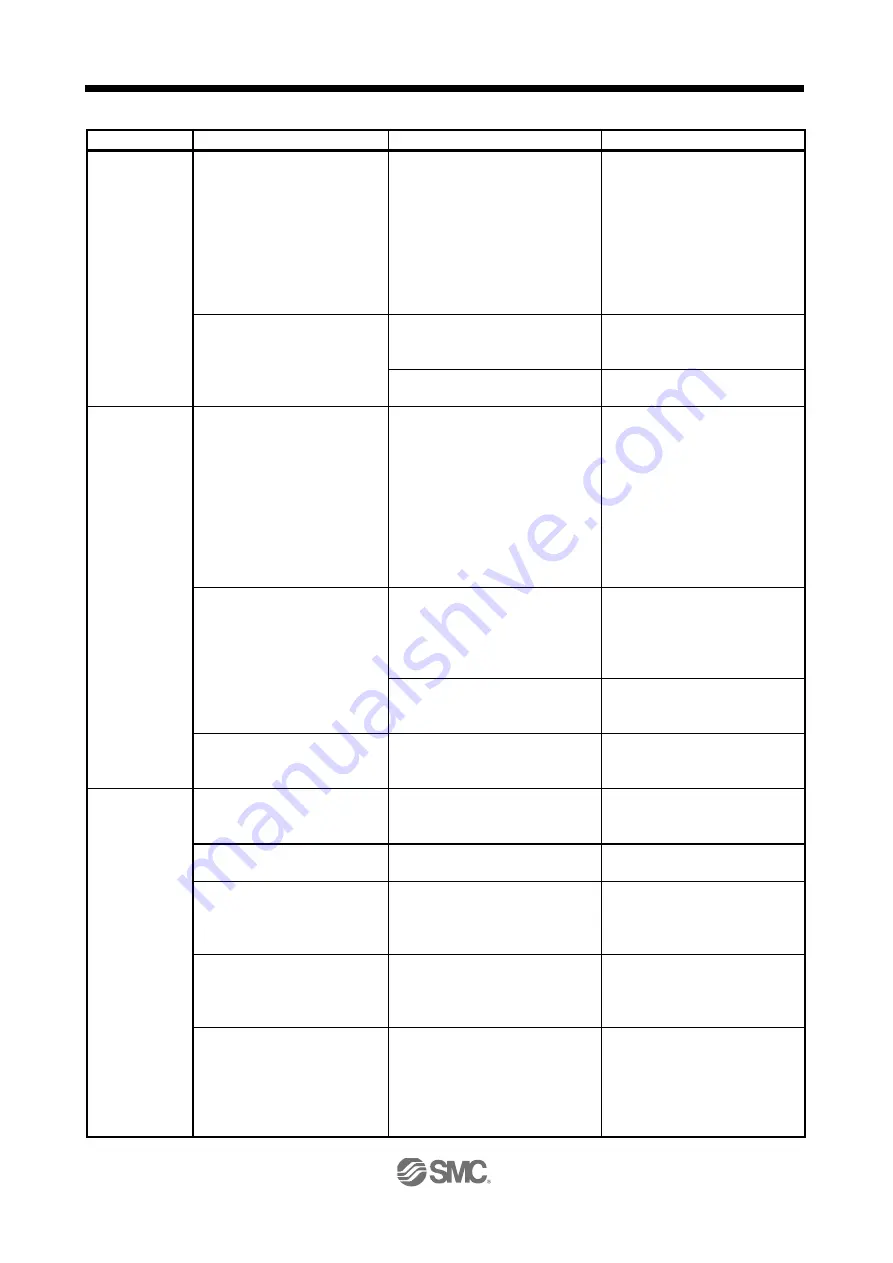
9 - 25
9. TROUBLESHOOTING
Phenomena
Checkpoint
Estimated cause
Action
The absolute
position
reconstruction
position is
misaligned at
recovery by the
absolute position
detection system.
Check the settings as follows for
the geared servo motor.
1. The travel distance per servo
motor revolution (Set with the
driver.)
2. Command input pulses per
revolution (parameter No.PA05)
3. Electronic gear (parameter
No.PA06/PA07)
The calculation of the reduction ratio
is not correct.
Review the setting of the reduction
ratio.
The positioning after is not
misaligned after the home position
return.
The maximum permissible speed at
power failure (3000r/min) is exceeded
while the driver is off.
Review the machine configuration in
order that the servo motor speed
does not exceed 3000r/min.
The transfer data to the driver is
incorrect.
Review the driver programs.
The overshoot/
undershoot
occurs.
1. Check that the overshoot/
undershoot occurs to confirm
the speed ripple with the
"Graph" command on the
"Monitor" menu on software
(MR Configurator2
TM
).
2. If the safe operation is possible,
repeat acceleration/deceleration
4 times or more to complete the
auto tuning.
1. The servo gain is too low or too
high.
2. The auto tuning response is low or
too high.
Adjust the auto tuning response and
then adjust the gains again.
(Refer to chapter 7.)
Check if the maximum torque does
not exceed the torque limit value.
1. Check the "instantaneous
torque" with the status display.
2. Check the torque ripple with the
"Graph" command on the
"Monitor" menu on software
(MR Configurator2
TM
).
The maximum torque is lacking.
1. The servo capacity is lacking.
2. The load is too large.
1. Change the mass or the shape of
the work to reduce the load.
2. Make the acceleration/
deceleration time shorter to make
the effective load ratio lower.
The torque limit settings are incorrect.
(Set with the parameter No.PA11/
PA12/PC35.)
Review the torque limit setting.
Check that the machine parts are
not unstable or do not have
backlashes.
The servo motor and the machine
(gear, coupling, etc.) have
backlashes.
Adjust the coupling or the backlash
of the mechanical parts.
The
communication
cannot be made
with the driver by
software (MR
Configurator2
TM
).
Check that the status is on-line.
The status is off-line.
Set the status to on-line.
Select "On-line" on "System
settings" on the "Setup" menu.
Check that the communication
cables are not damaged.
A communication cable is faulty.
Replace the communication cable.
Check the communication settings
(baud rate and port).
Check with the "system settings"
on the "setup" menu.
The communication setting is
incorrect.
Set the communication settings
correctly.
Check that the model selection is
set correctly.
Check with the "System settings"
command on the "Setup" menu.
The other model, which differs from
the one connected on the model
selection, is selected.
Set the model settings correctly.
Check that "MITSUBISHI
MELSERVO USB Controller" is
displayed under the driver by the
device manager of the personal
computer.
The device is not set correctly.
Delete the unknown device or other
devices. Turn the driver power on
and then re-set with found new
hardware wizard.
Refer to the software (MR
Configurator2
TM
) help for details.