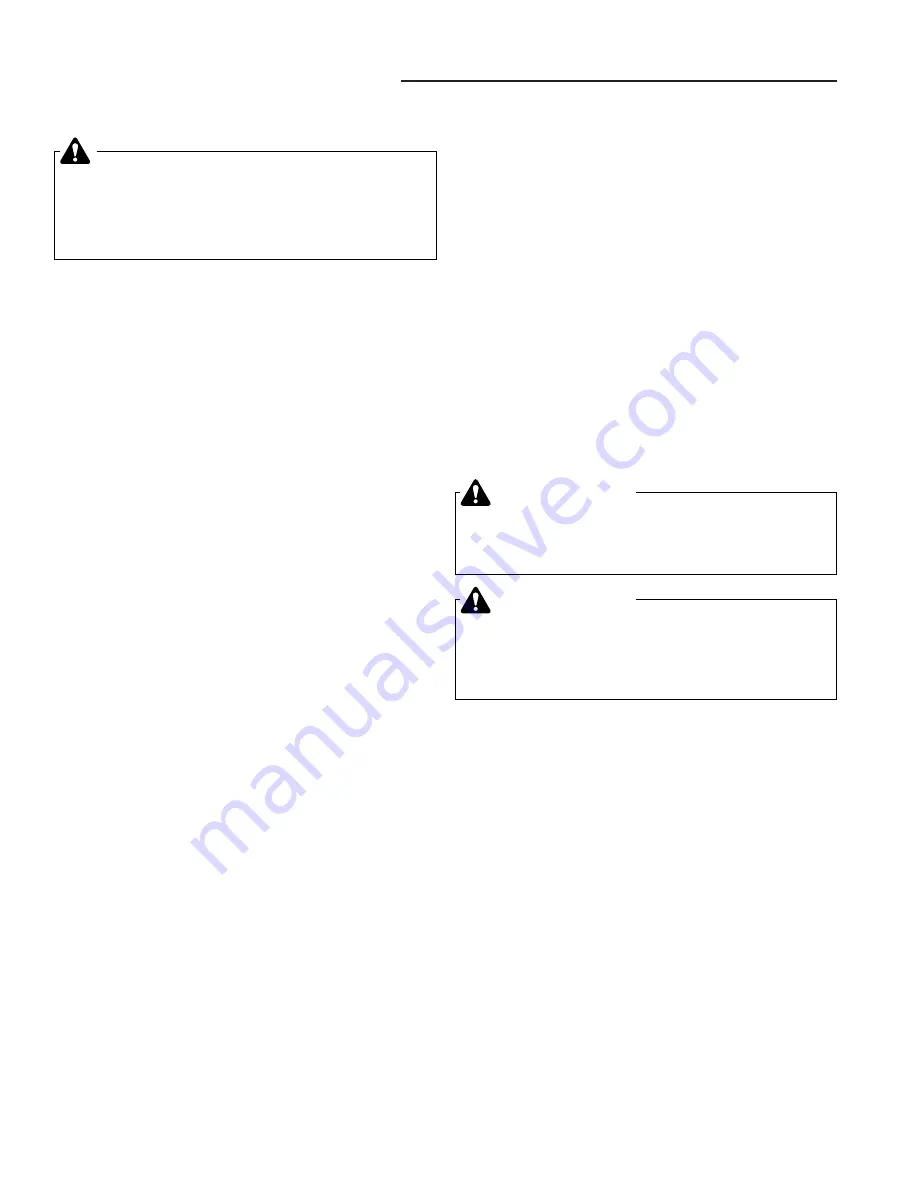
10 U-Type Hydrostatic Unit Service
Safety Rules
10 - 4
SAFETY RULES
General
• Simplicity Manufacturing, Inc., recommends the use
of environmentally sound waste storage and disposal
practices. Federal, state, and/or local regulations may
apply to the handling, storage, recycling, and dispos-
al of waste products. It is your responsibility to be
aware of and obey all applicable regulations. Use
suitable containers to collect, store, and dispose of
waste products in an approved and safe manner.
Never drain fluids onto the ground, into a sewer or
catch basin, or into a river or lake.
• Be certain that engine and exhaust assemblies are
not hot before cleaning ANY part of the tractor using
a flammable solvent. Never let shop rags used for
cleaning sit around and become fire hazards.
• Always keep work area clean and free of oil, grease,
and water. Some of these may be spilled on the floor
during normal disassembly procedures. Clean this up
as soon as possible to prevent accidents.
• Always disconnect starter cables from battery before
disassembling tractor to prevent accidental starting. If
cables are not disconnected (for normal servicing and
adjustments), be certain tractor is OFF and the key is
removed from ignition.
• Always wear “safety glasses” when working in the
shop area. Safety glass lenses will ALWAYS be
marked “K1.” Do not confuse ordinary prescription
glasses (even with tempered lenses) or sunglasses
with shop “safety glasses.”
• Always place tractor in NEUTRAL before servicing.
Always block both front or both back wheels when
working underneath tractor. Apply hand brake, if pos-
sible.
• Be certain that any part being removed is properly
supported or held to prevent personal injury or dam-
age to the part.
• Always use the proper tool for the work being done.
Where a specific tool is specified in the manual,
always use THAT tool.
• Be certain that any work bench or support being used
is strong enough. The weight of the part plus the
force applied to it during assembly or disassembly
may put a great strain on the bench or support.
SPECIFICATIONS AND DESCRIPTION
Specifications
Pump Displacement:
0-.913 in 3/rev.
Pump Input Speed:
3600 RPM
Motor Displacement:
.913 in 3/rev.
Motor Output Speed:
0-3600 RPM
Max. Operating Pressure:
3000 PSI
Charge Pump Displacement:.
33 in 3/rev.
Charge Relief Setting:
70-150 PSI
Implement Relief Setting
900-1000 PSI
Filtration:
.25 micron
(nominal)
Hydraulic Fluid Recommendations
Use Type F Automatic Transmission Fluid.
This notation preceding Cautions and Warnings
in the text signifies important precautionary steps
which, if not properly followed, could result in
personal injury or damage to your equipment.
Specific
• Always thoroughly steam clean the hydrostatic unit
BEFORE any hoses are disconnected during removal
of the unit. If steam cleaning is not possible, clean the
unit using fuel oil or a suitable solvent. Do not use
paint thinner, acetone, or acetone-based solvents.
These may damage O-rings, gaskets, or seals.
• Always be certain that internal mechanisms and com-
ponents are kept free of chemical and particulate
contaminant's, even water.
• Do not use impact force (pounding) when installing
control linkage or drive coupling. Driving on the input,
output, or control shafts will damage the unit.
• Always use new hydraulic fluid and filter after servic-
ing unit.
• Always use new O-rings, gaskets, and seals during
assembly.
WARNING
Be aware that the hydraulic fluid is under pres-
sure. Use caution when disconnecting hydraulic
lines.
WARNING
If ANY hydraulic fluid is injected into the skin, it
must be surgically removed within a few hours
by a doctor familiar with this type of injury, or
gangrene may result.
Not
for
Reproduction
Summary of Contents for AGCO Allis 2000 Series
Page 1: ...USE N o t f o r R e p r o d u c t i o n...
Page 18: ...1 16 1 General Information Notes N o t f o r R e p r o d u c t i o n...
Page 24: ...2 Troubleshooting Notes 2 6 N o t f o r R e p r o d u c t i o n...
Page 52: ...5 Belt Replacement Notes 5 6 N o t f o r R e p r o d u c t i o n...
Page 101: ...7 33 7 Electrical System Service Troubleshooting Notes N o t f o r R e p r o d u c t i o n...
Page 114: ...7 46 7 Electrical System Service Notes N o t f o r R e p r o d u c t i o n...
Page 126: ...8 Power Steering Service Notes 8 12 N o t f o r R e p r o d u c t i o n...
Page 162: ...11 Transaxle Removal Installation Notes 11 10 N o t f o r R e p r o d u c t i o n...
Page 206: ...13 Engine Removal Installation Notes 13 36 N o t f o r R e p r o d u c t i o n...
Page 244: ...17 Miscellaneous Component Service Notes 17 4 N o t f o r R e p r o d u c t i o n...
Page 304: ...19 Implement Lift Service Notes 19 10 N o t f o r R e p r o d u c t i o n...
Page 312: ...20 Power Steering Unit Service Notes 20 8 N o t f o r R e p r o d u c t i o n...