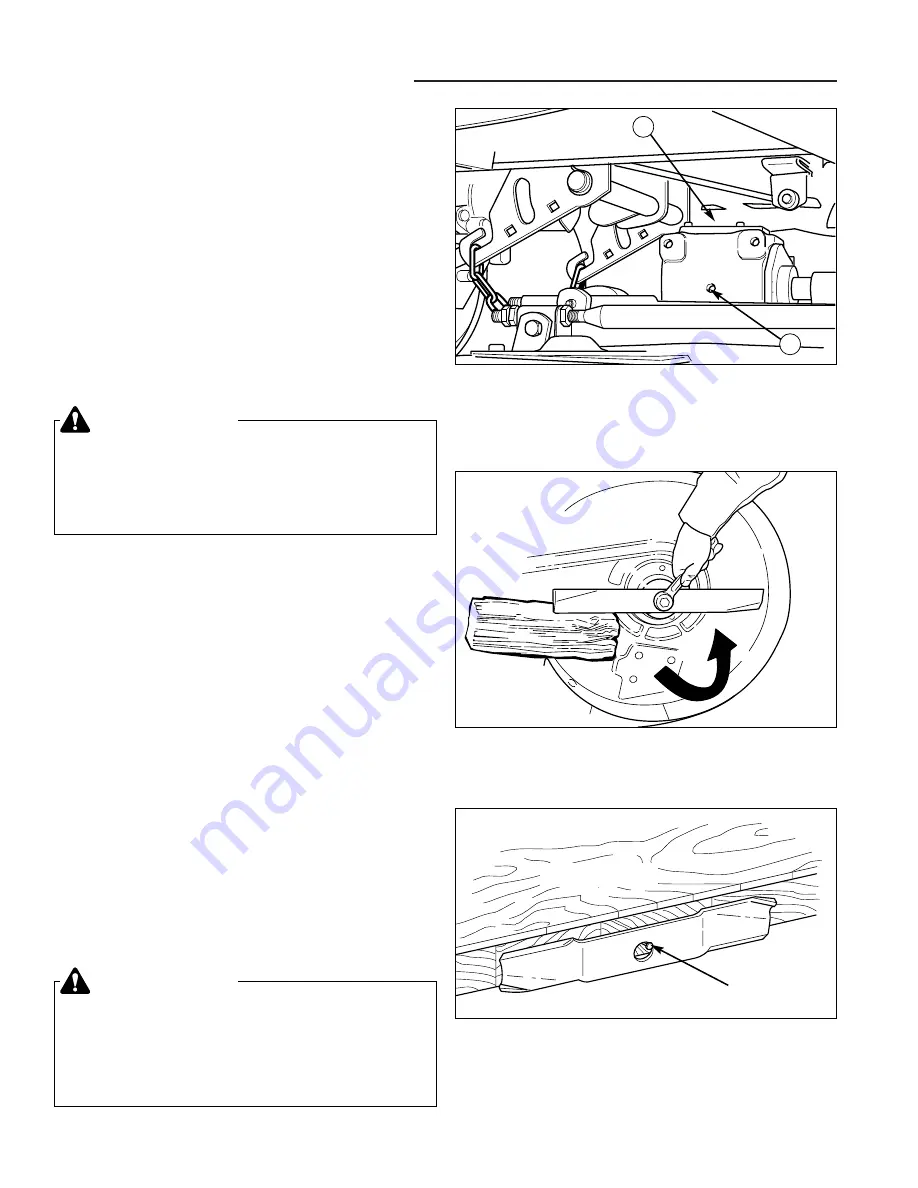
3 - 6
3 Maintenance
Maintenance Procedures – All Models
Check Mower Deck Gear Box Oil
To check the mower deck gear box oil:
1. Remove the plugs from the top and side of the gear
box (Figure 4).
2. Add SAE 85W-90 oil through the top hole until oil
comes out the side fill hole. Place a shop towel under
the side opening to keep oil off the belt and pulleys.
3. Replace the plugs and wipe up any spilled oil.
Figure 4. Gear Box Fill Plug Location
A. Top Fill Plug
B. Side Fill Plug
A
B
SERVICING THE MOWER BLADES
1. Remove mower from the tractor. See Mower
Installation & Removal.
2. Blades should be sharp and free of nicks and dents.
If not, sharpen blades as described in the following
steps.
3. To remove blade for sharpening, use a wood block to
hold blade while removing the blade mounting cap-
screw (Figure 5).
4. Use a file to sharpen blade to fine edge. Remove all
nicks and dents in blade edge. If blade is severely
damaged, it should be replaced.
5. Balance the blade as shown in Figure 6. Center the
blade’s hole on a nail lubricated with a drop of oil. A
balanced blade will remain level.
6. Reinstall each blade with the tabs pointing up toward
deck as shown in Figure 7. Secure with a capscrew
(D), spring washer (C), and spline washer (B). Be
certain the spline washer is aligned with the shaft
splines. Use a wood block to prevent blade rotation,
and torque capscrews to 45-55 ft. lbs. (61-75 N.m.).
WARNING
For your personal safety, do not handle the sharp
mower blades with bare hands. Careless or
improper handling of blades may result in serious
injury.
WARNING
For your personal safety, blade mounting
capscrews must each be installed with a hex
washer and spring washer, then securely tightened.
Torque blade mounting capscrew to 45-55 ft. lbs.
(61-75 N.m.).
LOOSEN
Figure 5. Removing the Blade
Figure 6. Balancing the Blade
Workbench
Nail
Not
for
Reproduction
Summary of Contents for AGCO Allis 2000 Series
Page 1: ...USE N o t f o r R e p r o d u c t i o n...
Page 18: ...1 16 1 General Information Notes N o t f o r R e p r o d u c t i o n...
Page 24: ...2 Troubleshooting Notes 2 6 N o t f o r R e p r o d u c t i o n...
Page 52: ...5 Belt Replacement Notes 5 6 N o t f o r R e p r o d u c t i o n...
Page 101: ...7 33 7 Electrical System Service Troubleshooting Notes N o t f o r R e p r o d u c t i o n...
Page 114: ...7 46 7 Electrical System Service Notes N o t f o r R e p r o d u c t i o n...
Page 126: ...8 Power Steering Service Notes 8 12 N o t f o r R e p r o d u c t i o n...
Page 162: ...11 Transaxle Removal Installation Notes 11 10 N o t f o r R e p r o d u c t i o n...
Page 206: ...13 Engine Removal Installation Notes 13 36 N o t f o r R e p r o d u c t i o n...
Page 244: ...17 Miscellaneous Component Service Notes 17 4 N o t f o r R e p r o d u c t i o n...
Page 304: ...19 Implement Lift Service Notes 19 10 N o t f o r R e p r o d u c t i o n...
Page 312: ...20 Power Steering Unit Service Notes 20 8 N o t f o r R e p r o d u c t i o n...