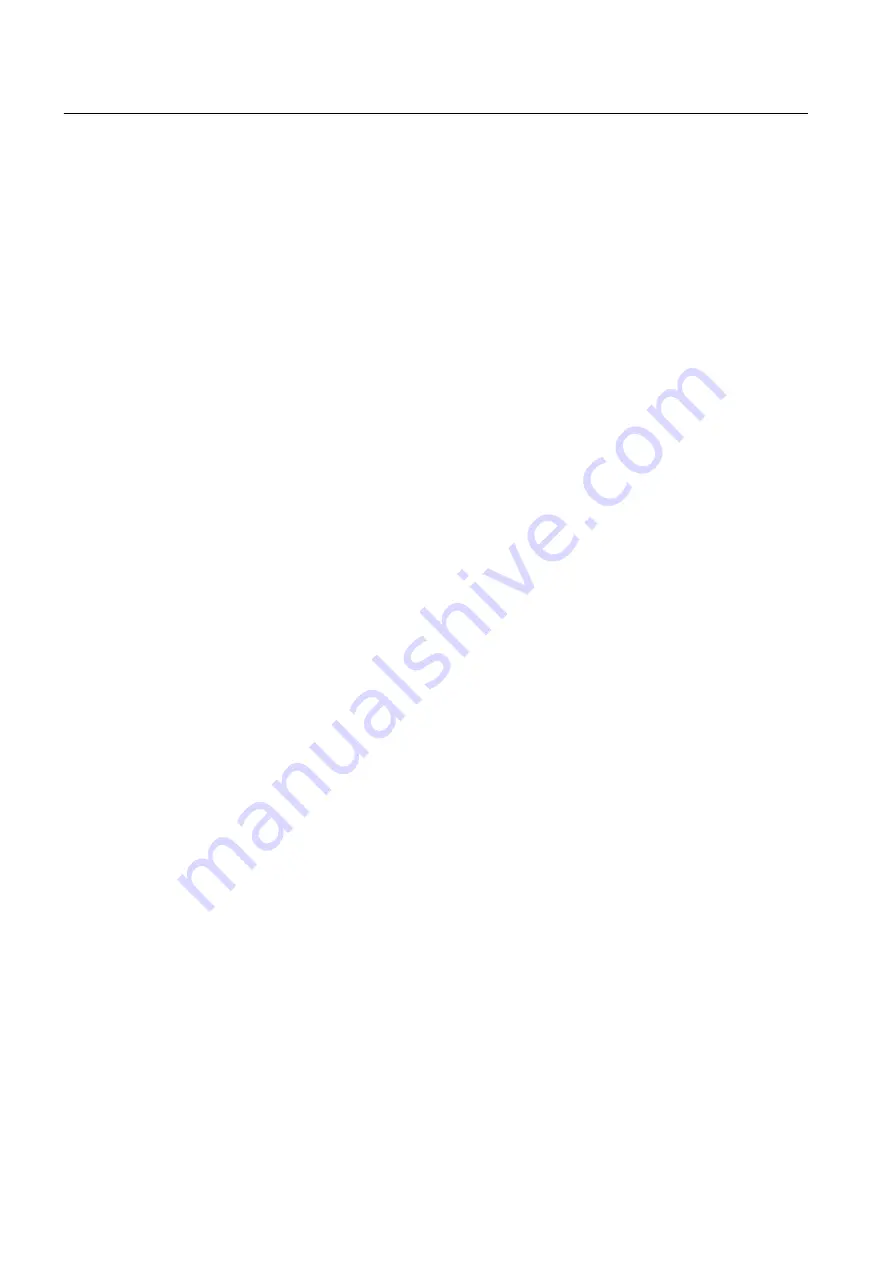
4.14
Converter operation
4.14.1
Connecting to a converter
Selecting and connecting the cable
● Use Motion Connect cables or symmetrically constructed, shielded cables to connect the
motor to a converter. The cable shielding, made up of as many strands as possible, must
have good electrical conductivity. Braided shields made of copper or aluminum are well
suited.
● The shield is connected at both ends, at the motor and converter. Keep unshielded cable
ends as short as possible.
● In order to ensure that high-frequency currents are efficiently discharged, provide a 360°
contact through a large surface area at the converter and at the motor. Use for instance,
EMC glands at the cable entries.
Measures to reduce bearing currents
To specifically reduce and prevent damage caused by bearing currents, consider the system
as a whole, which comprises the motor, converter, and driven machine. The following
precautions help to prevent bearing currents:
● Setting up a properly meshed grounding system in the system as a whole, with low
impedance for high-frequency currents
● No potential difference between the motor, converter, and working machine.
– Use symmetrical, shielded connecting cables.
– Connect the cable shield at both ends over the greatest possible surface area (360°
contact).
– Use equipotential bonding conductors between the motor and the driven machine as
well as between the motor and the converter
● Limit the voltage rate of rise by using an output filter to dampen harmonic components in
the output voltage
4.14.2
Insulated bearings for converter operation
If the machine is operated with a low-voltage converter such as SINAMICS G150 / S150 /
S120, then an insulated bearing and a speed encoder with insulated bearings (option) is
mounted at the non-drive end.
For 1PH818, the insulated bearings are optional; for 1PH822 and 1PH828, insulated bearings
are standard.
Comply with the plates on the machine relating to bearing insulation and possible bridges.
Preparations for use
4.14 Converter operation
SIMOTICS M-1PH8 1PH818., 1PH822.
46
Operating Instructions 07/2016
Summary of Contents for 1PH818
Page 2: ...18 07 2016 14 04 V14 00 ...
Page 12: ...Introduction SIMOTICS M 1PH8 1PH818 1PH822 12 Operating Instructions 07 2016 ...
Page 28: ...Description SIMOTICS M 1PH8 1PH818 1PH822 28 Operating Instructions 07 2016 ...
Page 100: ...Operation 8 10 Faults SIMOTICS M 1PH8 1PH818 1PH822 100 Operating Instructions 07 2016 ...
Page 136: ...Quality documents SIMOTICS M 1PH8 1PH818 1PH822 136 Operating Instructions 07 2016 ...
Page 197: ...AA Manual STROMAG Break AC Manual Ziehl Abegg external fan ...