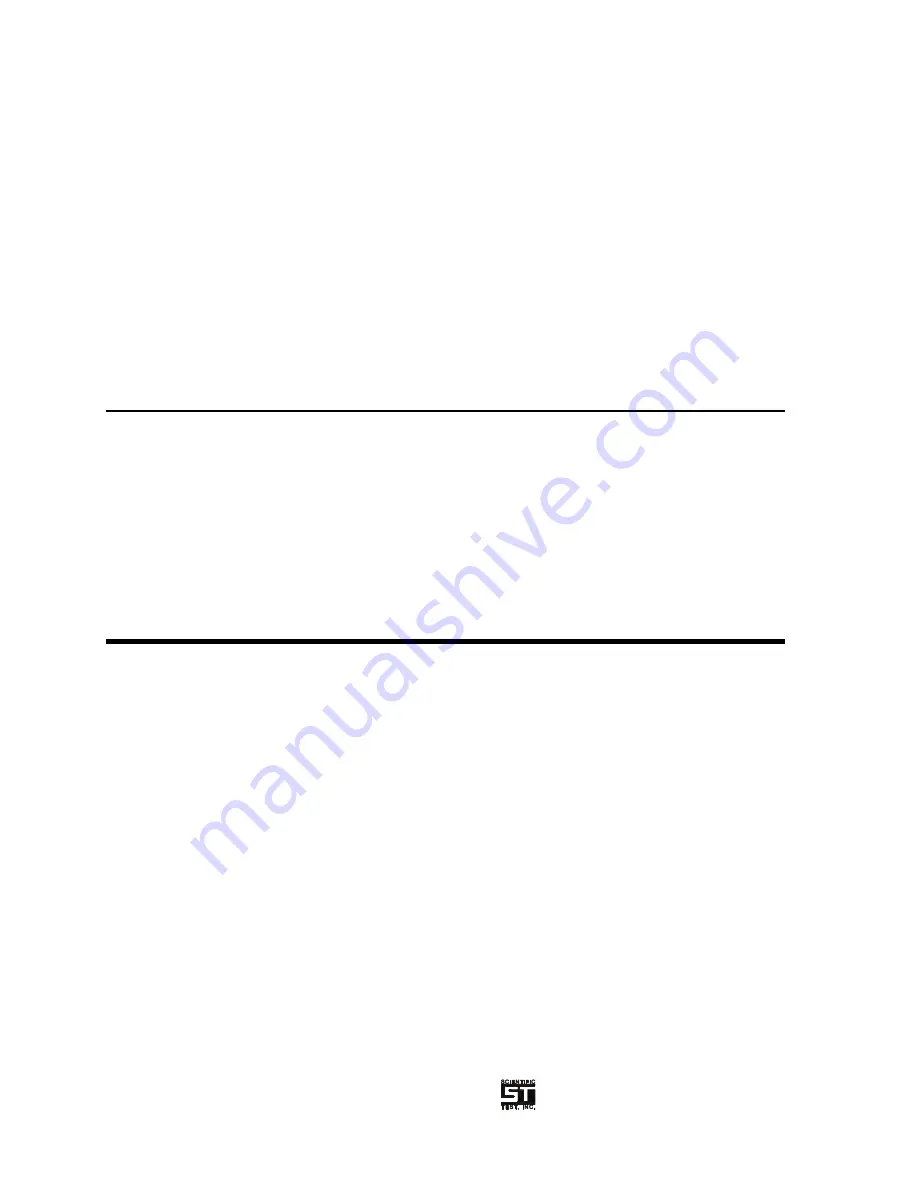
3 - THEORY
3-2
Version 1.23
MODEL 5000 SERIES MANUAL
The computer bus extends forward into the larger section of the card cage for
computer control of the main boards. The larger section of the card cage contains
the Power Sources, Analog, Relay, Normalize and Control boards. At the gold edge
fingers of each main board, J1 pins 1 through 44 carry analog signals plus AC and
DC power for distribution among the boards. J2 pins 1 through 56 carry the
computer signals (extension of the STD bus).
Low-level analog signals are generated by the Analog I/O board and transferred
down the bus (OUT line) to the power sources. Result signals are returned (IN line)
to the Analog I/O board to generate the answer. Analog signals are referenced to the
Signal line (S line) that is separated from ground to eliminate current in the S line.
The power source outputs are steered through the Relay board to the device front
panel jacks. The Relay board also switches in internal loads or the external loads on
the front panel jacks.
3.1.2 Analog Board
The Analog Board generates the analog reference signals that are applied to the Hi
and Lo Sources to control their current and voltage drives and clamps. There is one
output bus (pin J1-33) over which these signals are transferred. The signals are
generated and put on the OUT bus in sequence and de-multiplexed from the bus by
the sample and hold circuits on the source boards. The Analog Board also monitors
the resultant current and voltage signals as they are returned in the input (IN) bus
(pin J1-31). They are compared after filtering in the proper time frame to obtain the
result of each test as it occurs.
See Analog Board Schematic in Parts Lists/Schematics section of this manual.
3.2 Power Sources
Two power sources are used for device excitation. The Hi Source is applied across
the device main terminals (collector-emitter, anode-cathode, etc.) and the Lo Source
is applied to the device control terminal. Ranges and limits of the two sources are
shown on the specification and current curves sheets in Section 4.
Voltage and current ranges are programmed automatically for each source as
required by entered test limits. The sources can be used as either voltage or current
sources. When used as a voltage source, the current is clamped. When used as a
current source, the output voltage is clamped. Outputs and clamp limits are
determined automatically and are dependent on test type and programmed test
values. Whether the source is used in the current or voltage mode depends on the
particular test to be executed. A leakage test, for example, would use the Hi Source
in the voltage mode with the current clamped at a value just above the programmed
leakage limit.
Power source variables are rise time, test time and duty cycle. These variables are
dependent on the particular test and the entered test values and are determined
automatically by the system. Hi Source test time above 10mA is 300 microseconds.
The power sources are variable gain high current buffered power amplifiers that
develop the current and voltage drives reflected in the specifications. The Hi Source
Board drives through the buffer directly to the Relay Board where anode/collector
loads are applied if required. Drive is then applied to the device. For voltages
greater than 50 volts, the high source is amplified through a transformer booster
Summary of Contents for 5000 Series
Page 2: ......
Page 4: ......
Page 10: ......
Page 30: ...TABLE OF CONTENTS xx Version 1 23 MODEL 5000 SERIES MANUAL ...
Page 38: ...1 OVERVIEW 1 8 Version 1 23 MODEL 5000 SERIES MANUAL ...
Page 52: ...3 THEORY 3 6 Version 1 23 MODEL 5000 SERIES MANUAL ...
Page 62: ...4 SPECIFICATIONS 4 10 Version 1 23 MODEL 5000 SERIES MANUAL ...
Page 64: ...5 BASIC OPERATION 5 2 Version 1 23 MODEL 5000 SERIES MANUAL ...
Page 102: ...6 PC SOFTWARE 6 38 Version 1 23 MODEL 5000 SERIES MANUAL ...
Page 218: ...7 MAINTENANCE TROUBLESHOOTING 7 116 Version 1 23 MODEL 5000 SERIES MANUAL ...
Page 226: ...8 LOW CURRENT DECK 8 8 Version 1 23 MODEL 5000 SERIES MANUAL ...
Page 234: ...10 PIN PROGRAMMABLE SCANNER 10 4 Version 1 23 MODEL 5000 SERIES MANUAL ...
Page 242: ...APPENDICES 13 2 Version 1 23 MODEL 5000 SERIES MANUAL ...
Page 244: ...APPENDIX A 13 4 Version 1 23 MODEL 5000 SERIES MANUAL ...
Page 250: ...APPENDIX C 13 10 Version 1 23 MODEL 5000 SERIES MANUAL ...
Page 252: ...APPENDIX D 13 12 Version 1 23 MODEL 5000 SERIES MANUAL ...
Page 254: ...APPENDIX E 13 14 Version 1 23 MODEL 5000 SERIES MANUAL ...
Page 258: ...APPENDIX F 13 18 Version 1 23 MODEL 5000 SERIES MANUAL ...
Page 262: ...APPENDIX G 13 22 Version 1 23 MODEL 5000 SERIES MANUAL ...
Page 268: ...APPENDIX H 13 28 Version 1 23 MODEL 5000 SERIES MANUAL ...
Page 290: ...APPENDIX I 13 50 Version 1 23 MODEL 5000 SERIES MANUAL ...
Page 292: ...APPENDIX J 13 52 Version 1 23 MODEL 5000 SERIES MANUAL ...
Page 296: ...APPENDIX K 13 56 Version 1 23 MODEL 5000 SERIES MANUAL ...
Page 304: ...APPENDIX M 13 64 Version 1 23 MODEL 5000 SERIES MANUAL ...
Page 308: ...APPENDIX N 13 68 Version 1 23 MODEL 5000 SERIES MANUAL ...
Page 312: ...APPENDIX P 13 72 Version 1 23 MODEL 5000 SERIES MANUAL ...
Page 316: ...14 APPLICATION NOTES 14 2 Version 1 23 MODEL 5000 SERIES MANUAL ...
Page 318: ...APP 001 14 4 Version 1 23 MODEL 5000 SERIES MANUAL Figure 14 2 APP 001 Test Screen ...
Page 320: ...APP 001 14 6 Version 1 23 MODEL 5000 SERIES MANUAL ...
Page 322: ...APP 002 14 8 Version 1 23 MODEL 5000 SERIES MANUAL Figure 14 6 APP 002 Bin Sort Screen ...
Page 324: ...APP 003 14 10 Version 1 23 MODEL 5000 SERIES MANUAL ...
Page 326: ...APP 004 14 12 Version 1 23 MODEL 5000 SERIES MANUAL ...
Page 332: ...APP 006 14 18 Version 1 23 MODEL 5000 SERIES MANUAL ...
Page 336: ...APP 007 14 22 Version 1 23 MODEL 5000 SERIES MANUAL ...
Page 338: ...APP 008 14 24 Version 1 23 MODEL 5000 SERIES MANUAL ...
Page 340: ...APP 009 14 26 Version 1 23 MODEL 5000 SERIES MANUAL ...