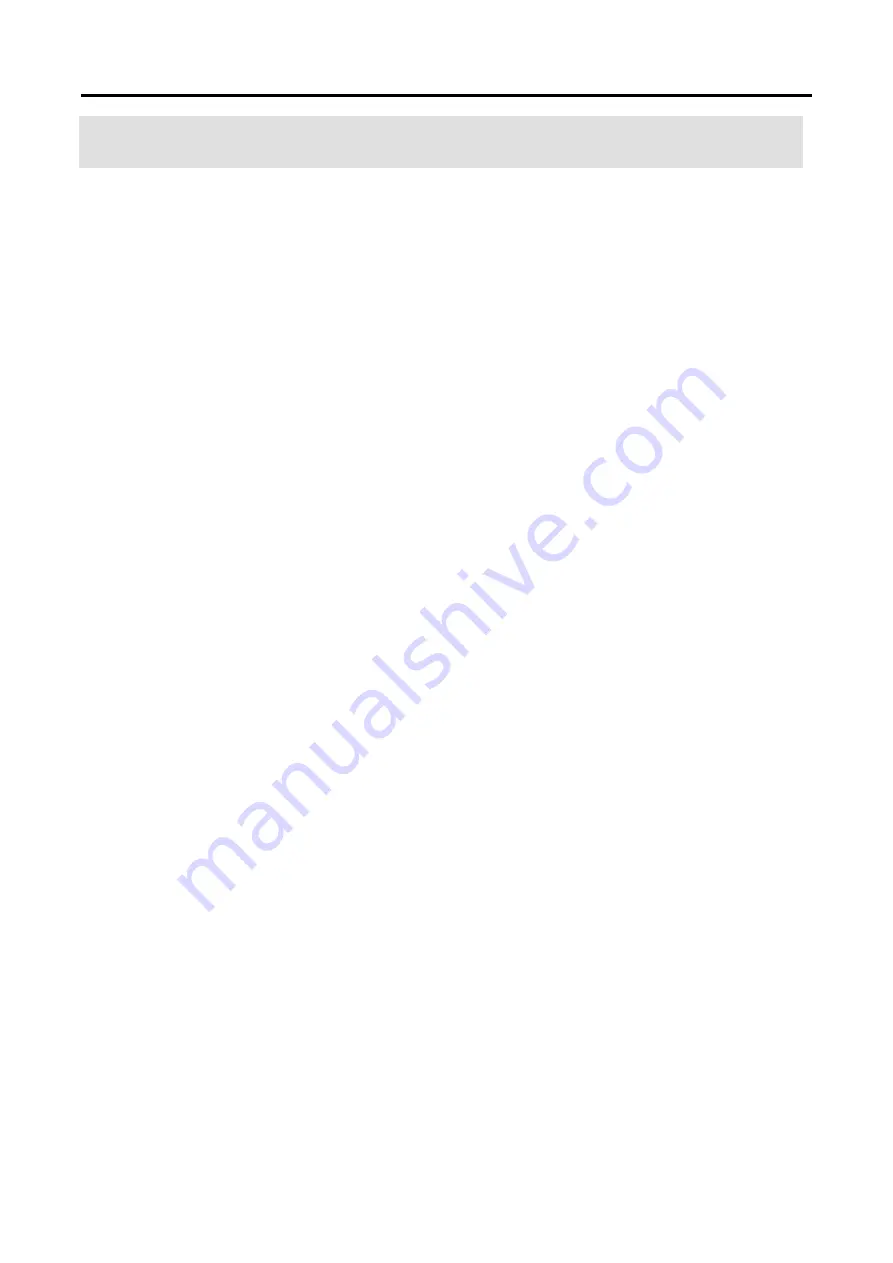
6. Servo Tuning
6-1
6.1 Servo tuning functions and basic adjustment procedure
To operate the servo motor (and machine) using the servo amplifier, adjustments of the servo
gain and its control system is necessary. Generally, the higher setting value of the servo gain
increases the machine response. However, if the servo gain is too high, in a lower rigidity
machine, vibration may result and the machine response will not increase. The servo gain and its
control system need to be appropriately adjusted according to the operating servo motor and the
mechanical system, and this adjustment method is called Servo tuning.
Following is an explanation of the Servo tuning procedure:
6.1.1 Servo tuning functions
■
Adaptive notch filter function
Realizing vibration suppression operation of machine vibration by estimating resonant
frequency of machine system during servo motor operation and making feedback it to the
control system.
■
Automatic Tuning function
Automatic
Tuning
Servo amplifier estimates load inertia moment ratio during operation, and then
automatically adjusts servo gain and filter frequency on a real-time basis. This is the
most basic tuning method.
Automatic Tuning [JRAT Manual Setting]
The servo amplifier does not estimate the Load inertia moment ratio. Servo gain and
filter frequency are adjusted automatically corresponding to the load inertia moment
ratio and the responses that are already set. This method is used when the Load inertia
moment ratio could not be estimated correctly with auto-tuning.
■
Manual Tuning
Set all parameters, such as Load inertia moment ratio, servo gain, filter frequency, etc.
manually. This method is used when characteristics during auto-tuning are insufficient.
■
The function of making servo gain higher
Velocity loop phase lead compensation
This is the function which compensate phase delay of velocity control system, to get
higher velocity loop proportional gain.
Position loop phase lead compensation
This is the function which compensate phase delay of position control system, to get
higher position loop proportional gain.
Torque feed forward compensation
This is the function which improve response for the command of control system by
applying feed forward compensation to torque control system.
■
Model following control
Model following control is a control method that ensures a higher response by composing a
model control system including the mechanical system in a servo amplifier to operate the
actual servo motor in order to follow the model control system.
■
Auto notch filter tuning function
Notch filter is able to suppress high frequency resonance depends on a mechanical system
coupling or stiffness. "Auto notch filter tuning" is able to search mechanical system resonant
frequency easily by rotating servo motor in a short time.
Summary of Contents for SANMOTION 3E S
Page 1: ...M0011696D Instruction Manual TYPE S For Rotary Motor Linear Motor Interface ...
Page 2: ......
Page 182: ...No Text on This Page ...
Page 200: ...No Text on This Page ...
Page 270: ...No Text on This Page ...
Page 336: ...No Text on This Page ...
Page 384: ...No Text on This Page ...
Page 408: ...No Text on This Page ...
Page 420: ...12 Appendix 12 10 12 4 Servo motor data sheet Refer another document M0011792 ...
Page 422: ...12 Appendix 12 12 12 5 3 RS3 03A HL 12 5 4 RS3A05A HL ...
Page 423: ...12 5 Servo amplifier dimensions 12 13 12 Appendix 12 5 5 RS3A07A HL 12 5 6 RS3A10A HA ...
Page 424: ...12 Appendix 12 14 12 5 7 RS3A15A HA 12 5 8 RS3A30A HL ...
Page 428: ...12 Appendix 12 18 12 5 13 RS3C02A HA 12 5 14 RS3C05A HA ...
Page 429: ...12 5 Servo amplifier dimensions 12 19 12 Appendix 12 5 15 RS3C10A HA 12 5 16 RS3C15A HL ...
Page 430: ...12 Appendix 12 20 12 5 17 RS3C30A HM ...
Page 484: ...12 Appendix 12 74 REGIST 1000W Wiring diagram ...
Page 486: ...No Text on This Page ...
Page 487: ...Release Revision A Sep 2017 Revision B Sep 2018 Revision C Dec 2018 Revision D Apr 2019 ...