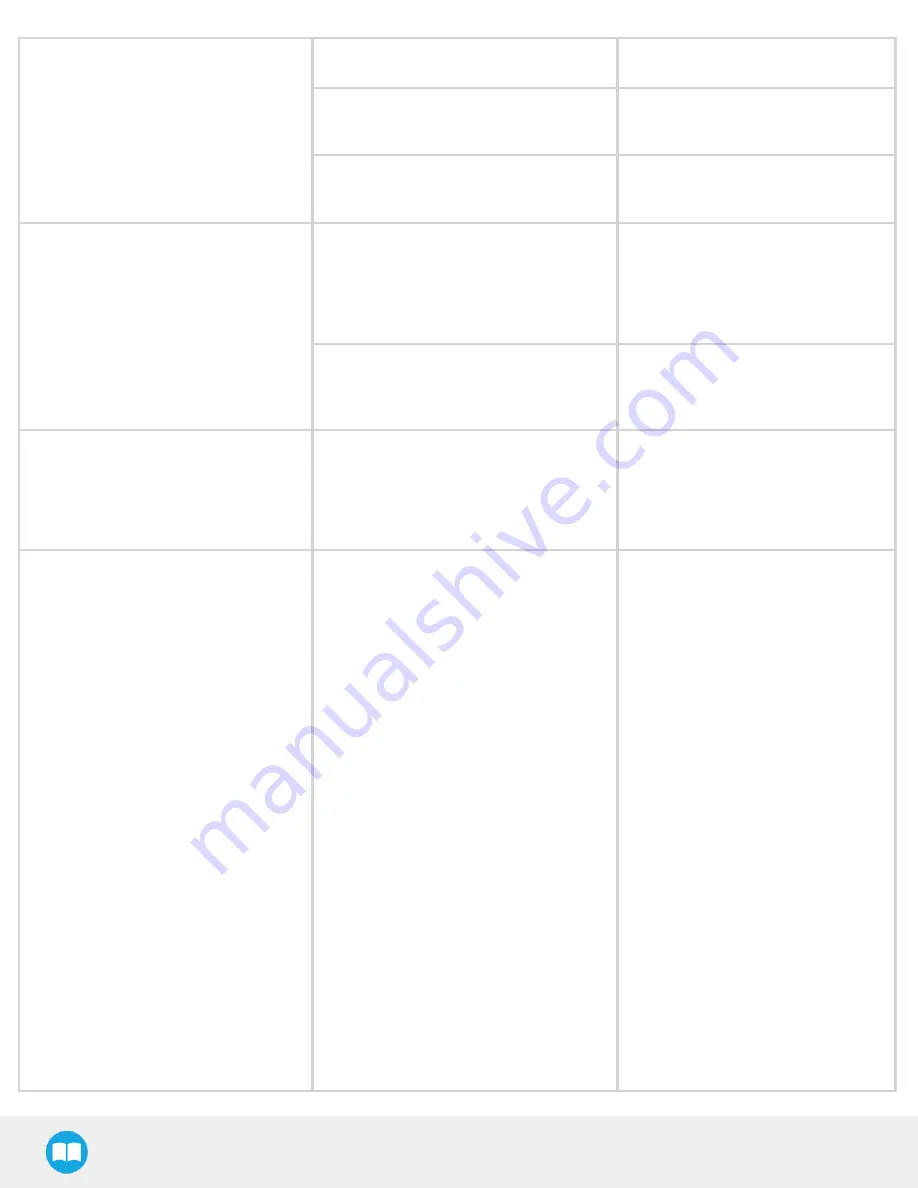
The robot triggered a protective stop
when placing a box on the first layer
The box height value entered is too high.
Verify the box height value.
The pallet height value entered is too
high.
Verify the pallet height value.
The TCP entered is incorrect.
Confirm that the TCP has been set
correctly.
Boxes are not consistently placed
straight on the pallet
The picking position is not stable.
Make sure your conveyor stop
consistently places boxes in the same
position. Box position should be
consistent in order to ensure a reliable
picking.
The picking position is incorrect.
Make sure that the picking position
places the vacuum gripper so that it is
squared and centered with the box.
Error Message "Collision detected"
during trajectory.
The layout in the pallet viewer does not
correspond with the actual layout. The
robot detected a collision with an object
that is not actually present.
l
Restart the program and select the
right box step.
l
Verify the TCP position and
orientation values.
Error Message "Discontinuous path /
joint solution impossible detected,
please change your starting point."
A singularity was reached on a planned
trajectory.
l
Go to PolyScope's Move tab, and
verify if the joints are at the center of
their range (0°) when the robot is at
the picking position. The algorithm
will adjust wrist 3 automatically at
program start.
l
If the box position is too close to
robot base, discontinuous path
issues can occur. Verify that the
picking zone is respected.
l
If this situation only occurs with
pallets on one side of the Solution,
try centering the layer pattern on the
pallet.
l
Verify TCP position and orientation
values.
l
The robot may have reached a
singularity or be closed to reaching
a singularity. Move the robot to the
Home position and restart the
program.
l
Should none of the above steps
solve the issue, please contact the
Robotiq support department.
Summary of Contents for PALLETIZING SOLUTION AX Series
Page 4: ...Palletizing Solution Instruction Manual 4 ...
Page 14: ...Palletizing Solution Instruction Manual 14 ...
Page 21: ...Palletizing Solution Instruction Manual 21 ...
Page 33: ...Base Cover Plate 1 Remove the cover plate that will allow the cable management 33 ...
Page 84: ...6 1 2 AirPick Vacuum Gripper Fig 6 1 AirPick general dimensions 84 ...
Page 85: ...Palletizing Solution Instruction Manual 6 1 3 Extra Reach Bracket 85 ...
Page 86: ...6 1 4 Bracket for Two 2 Suction Cups Fig 6 2 Two air nodes bracket s dimensions 86 ...
Page 113: ...12 2 Safety Connections Fig 12 2 Universal Robots Controller Safety Connections Schema ...