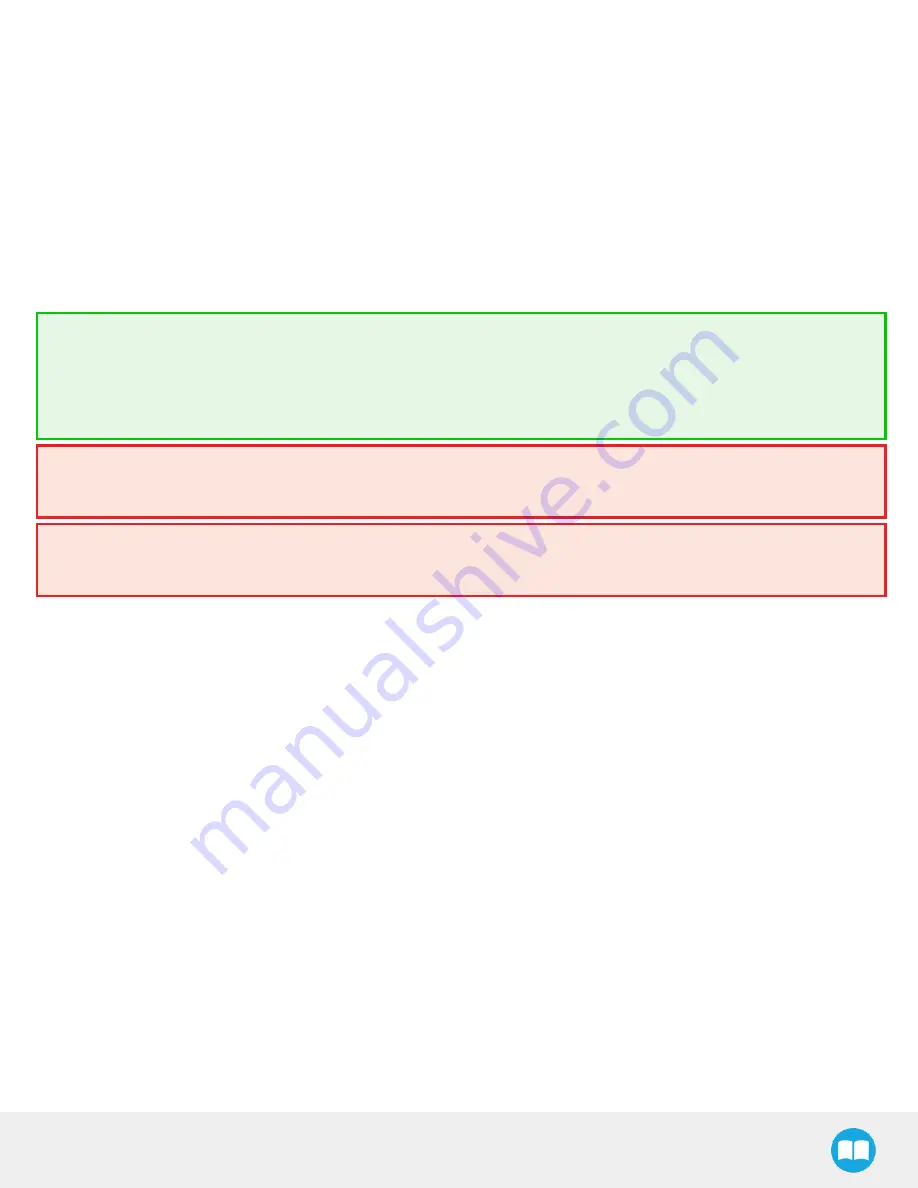
Palletizing Solution - Instruction Manual
Finalization and Power On
1. Install the box sensor on the bracket that best suits your setup with the provided screws.
2. Position the sensor box’s bracket so it can detect the box to be picked.
3. Connect the M8 connector of the box sensor's cable to the sensor.
4. Reinstall the front base cover using the provided screws (10).
5. Install the column cover using the provided screws (4).
6. Connect the power cable to the power outlet.
7. Power on the linear axis Controller and the robot.
Tip
The box sensor must be set properly. Once the system is running, adjust the detection distance with the sensitivity
adjuster. To have the sensor providing a high state, when detecting a box, be sure to set it in the light-on switching mode
(green light beside “L”). To do it, simply press the light-on / dark-on change-over switch for more than 1 second and less
than 4 seconds.
Warning
The column cover must be properly installed to achieve maximum structure rigidity.
Warning
Make sure to do a risk assessment before starting to use the Solution. For more details, please refer to the Safety section.
3.4.5. Physical Clearance and Reachable Area of the Robot
The computed trajectories allow the boxes or the robot to overrun the edges of the pallet when the robot moves the boxes to their
final position. Mitigation measures can be put in place to prevent a transient or quasi-static impact between a box, or the robot itself,
and an operator. Below are some examples:
l
Physical assets such as guardrails, bollards, etc. which prevent the operator from accessing the area
l
Sensors such as light curtains or area scanners which can detect the presence of a person, and stop the system before that per-
son reaches the danger zone.
l
Add virtual planes around pallet(s) option available in the Settings tab of the Palletizer node of the Robotiq URCap to contain the
overrun within a certain distance of the pallet. Please refer to Palletizer Node section to learn more about this option.
Potential overrun can be determined by the following formulae:
Front overrun
The potential front overrun is the highest value obtained using the following formula:
Potential front overrun (mm) = max max (0.1 x box height, 1280 - pallet depth, 180 + extra bracket reach + (0.1 x box height) -
(minimum horizontal box dimension /2))
48
Summary of Contents for PALLETIZING SOLUTION AX Series
Page 4: ...Palletizing Solution Instruction Manual 4 ...
Page 14: ...Palletizing Solution Instruction Manual 14 ...
Page 21: ...Palletizing Solution Instruction Manual 21 ...
Page 33: ...Base Cover Plate 1 Remove the cover plate that will allow the cable management 33 ...
Page 84: ...6 1 2 AirPick Vacuum Gripper Fig 6 1 AirPick general dimensions 84 ...
Page 85: ...Palletizing Solution Instruction Manual 6 1 3 Extra Reach Bracket 85 ...
Page 86: ...6 1 4 Bracket for Two 2 Suction Cups Fig 6 2 Two air nodes bracket s dimensions 86 ...
Page 113: ...12 2 Safety Connections Fig 12 2 Universal Robots Controller Safety Connections Schema ...