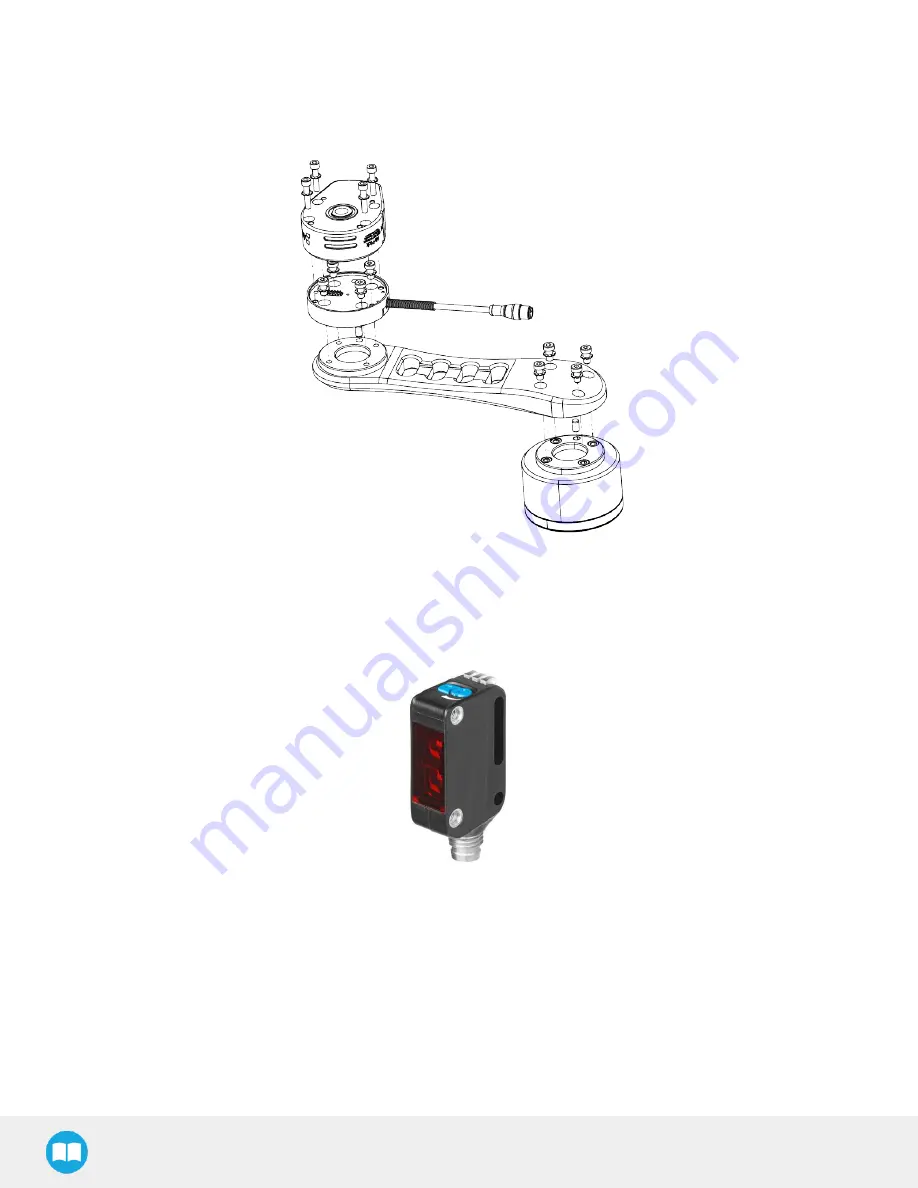
1.1.8. Extra Reach Gripper Bracket
The extra reach gripper bracket is included in the Solution to extend the AirPick Gripper of 200 mm from the robot tool flange. This
way, the Robotiq Palletizing Solution will be able to palletize boxes on large size pallets. Please refer to the Extra Reach Bracket
section for more details about the limitations of the extension bracket
Fig. 1-3: AirPick Vacuum Gripper Extra Reach Bracket
1.1.9. Box Detection Sensor
The Solution includes a box sensor that needs to be installed at the end of the conveyor in a way that it is triggered when a box is
ready to be picked up.
Fig. 1-4: Box Sensor
11
Summary of Contents for PALLETIZING SOLUTION AX Series
Page 4: ...Palletizing Solution Instruction Manual 4 ...
Page 14: ...Palletizing Solution Instruction Manual 14 ...
Page 21: ...Palletizing Solution Instruction Manual 21 ...
Page 33: ...Base Cover Plate 1 Remove the cover plate that will allow the cable management 33 ...
Page 84: ...6 1 2 AirPick Vacuum Gripper Fig 6 1 AirPick general dimensions 84 ...
Page 85: ...Palletizing Solution Instruction Manual 6 1 3 Extra Reach Bracket 85 ...
Page 86: ...6 1 4 Bracket for Two 2 Suction Cups Fig 6 2 Two air nodes bracket s dimensions 86 ...
Page 113: ...12 2 Safety Connections Fig 12 2 Universal Robots Controller Safety Connections Schema ...