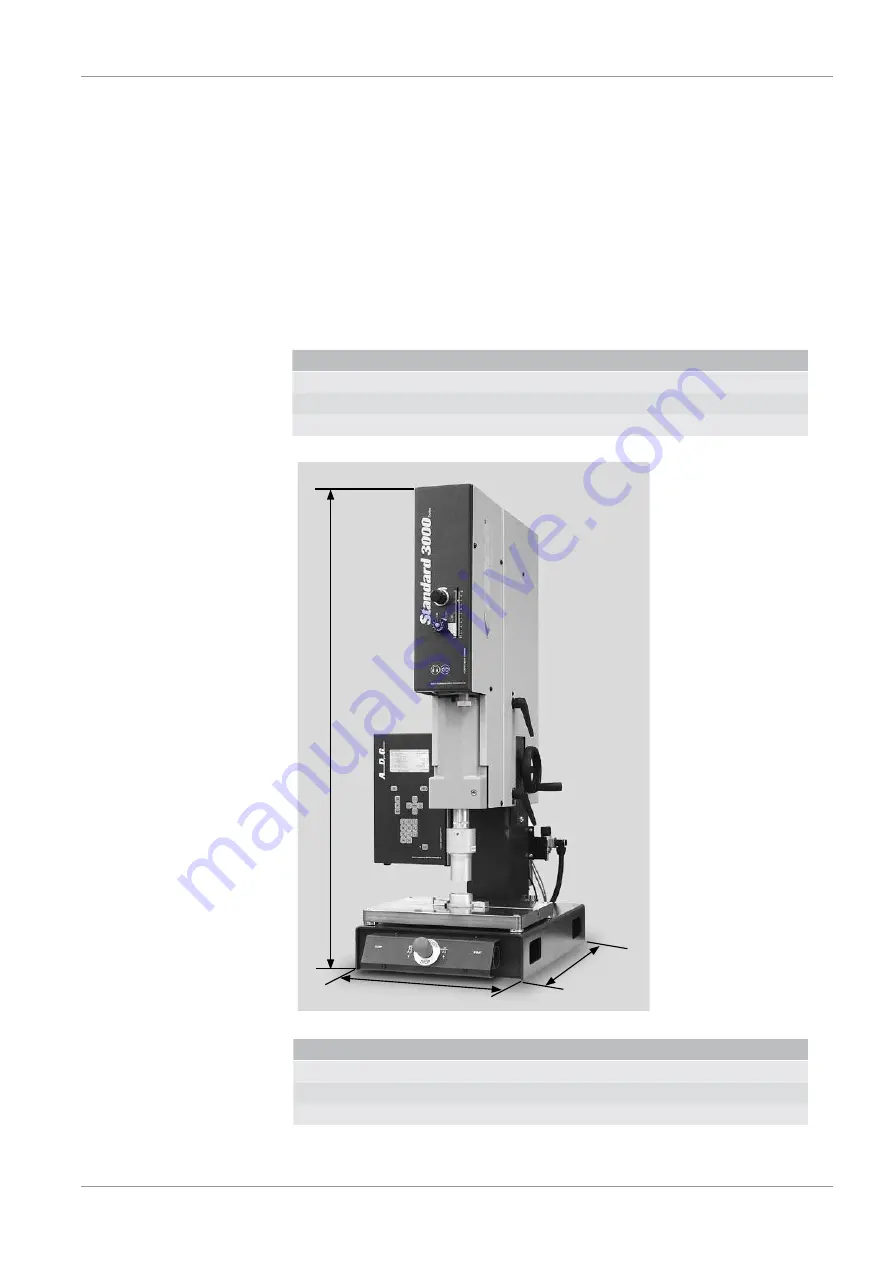
RINCO ULTRASONICS AG
Technical data | 10
BA_Standard3000_GB_V5.1_36566
119 / 137
Technical data
General information
CE
Short-circuit, overload, excessive temperature of the output stage
> 10 mA against PE
IP20
Dimensions and weights
Description
Value Designation
Length
760 mm
Width
400 mm
Height
1345 mm
Tab. 41:
Dimensions and weight
Fig. 69:
Press dimensions
Description
Value Designation
Length
340 mm
Width
205 mm
Height
345 mm
Tab. 42:
Generator dimensions
10
10.1
Conformity:
Protective measures against
Leakage current
Protection by housing
10.2
Press dimensions
Generator dimensions
1345 mm
760 mm
400 mm