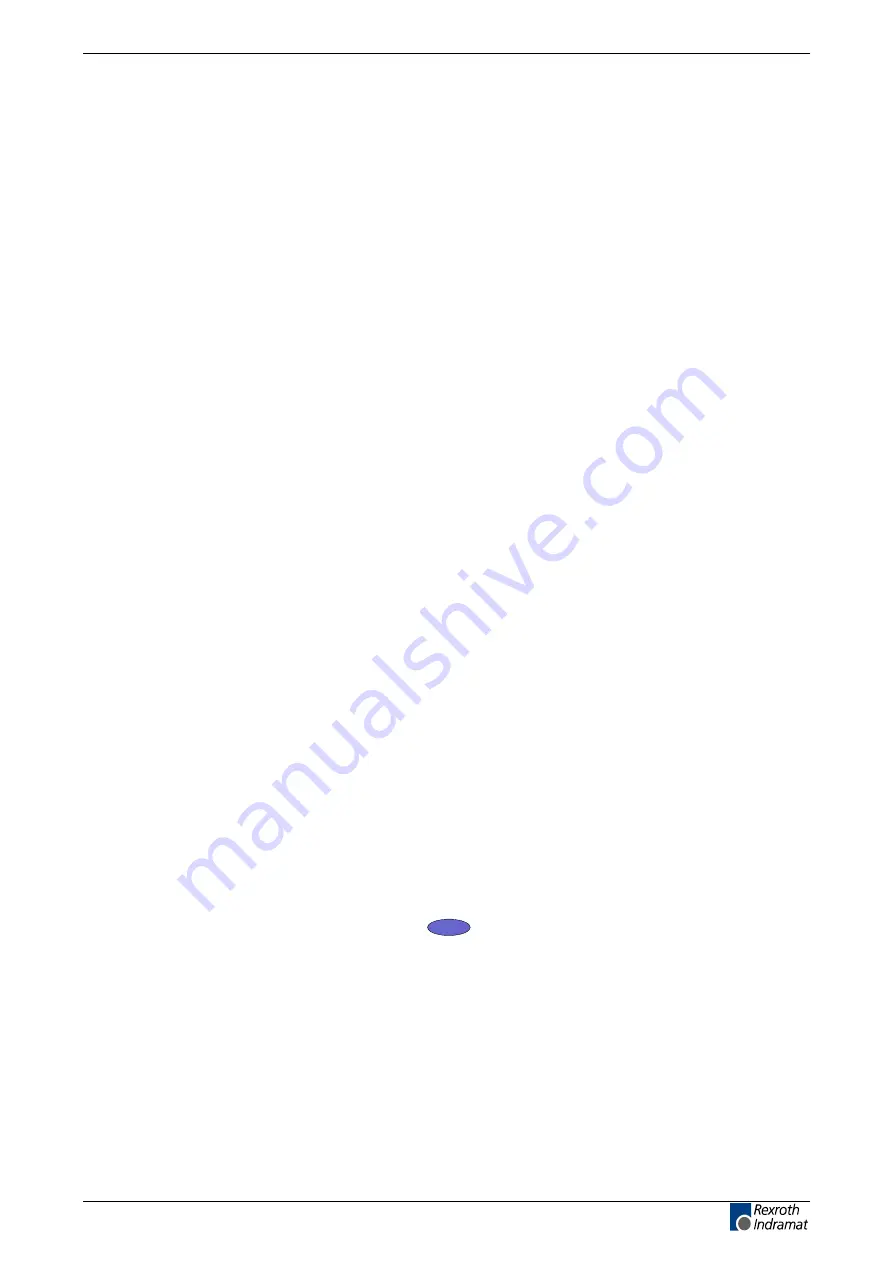
REFUdrive 500 RD51
Troubleshooting
7-1
DOK-RD500*-RD51*******-IB01-EN-P
7 Troubleshooting
7.1
Self test - error messages
After the initialization routine, the system executes a self test. The
individual components of the microcomputer system are tested, e.g. the
EEPROM, and the data from the power control board is read-in.
7.2 Alarms
If an alarm is output, the alarm message is displayed, alternating with the
programmed operating display. The alarm bit can be output at a digital
input. If the drive converter should be prevented from powering-up, the
alarm bit must be interlocked in the free parameterization.
7.3 Faults
During operation, permanently-programmed and parameterizable limit
values are continuously monitored. In order to protect the power module
against damage, when a limit value is exceeded, the drive converter is
always powered-down and the appropriate fault message is displayed.
For REFU
drive 500
drive converters with three-phase supply, when a fault
occurs, the main contactor is de-energized, and the power module goes
into a no-voltage condition. The appropriate fault message is displayed.
The fault is displayed using the red LED "alarm" on the front panel of the
drive.
Fault messages are saved in the fault memory so that they are not lost
when the power fails. The fault memory is called-up in the monitor
(operator control, refer to Section 4). The last faults are saved in the fault
memory. The last fault is S0 in the memory location, the oldest, in S9. A
new fault is always saved in memory location S0. All of the older faults in
the memory are shifted one position upwards. This means the fault at
memory location S9 is lost.
Fault acknowledgment
After a fault trip, the drive converter cannot be powered-up again until the
fault has been acknowledged. The fault cannot be acknowledged as long
as the fault still exists. If the cause of the fault has been removed, the
fault can be acknowledged after a timer has expired (P0093, factory
setting 1 sec.).
There are several ways of acknowledging a fault message:
•
Pressing
the
Esc
-button on the operator panel.
•
Pressing the button S9 "Fault acknowledgment" on the control card.
•
Using a digital input: Connect an H signal at the digital input, inter-
connect non-inverted D parameters of the selected digital inputs to
P0050.07.
•
Via the serial RS485 interface; transfer control word with bit 7 set to
"high".
LSA Control S.L. www.lsa-control.com [email protected] (+34) 960 62 43 01