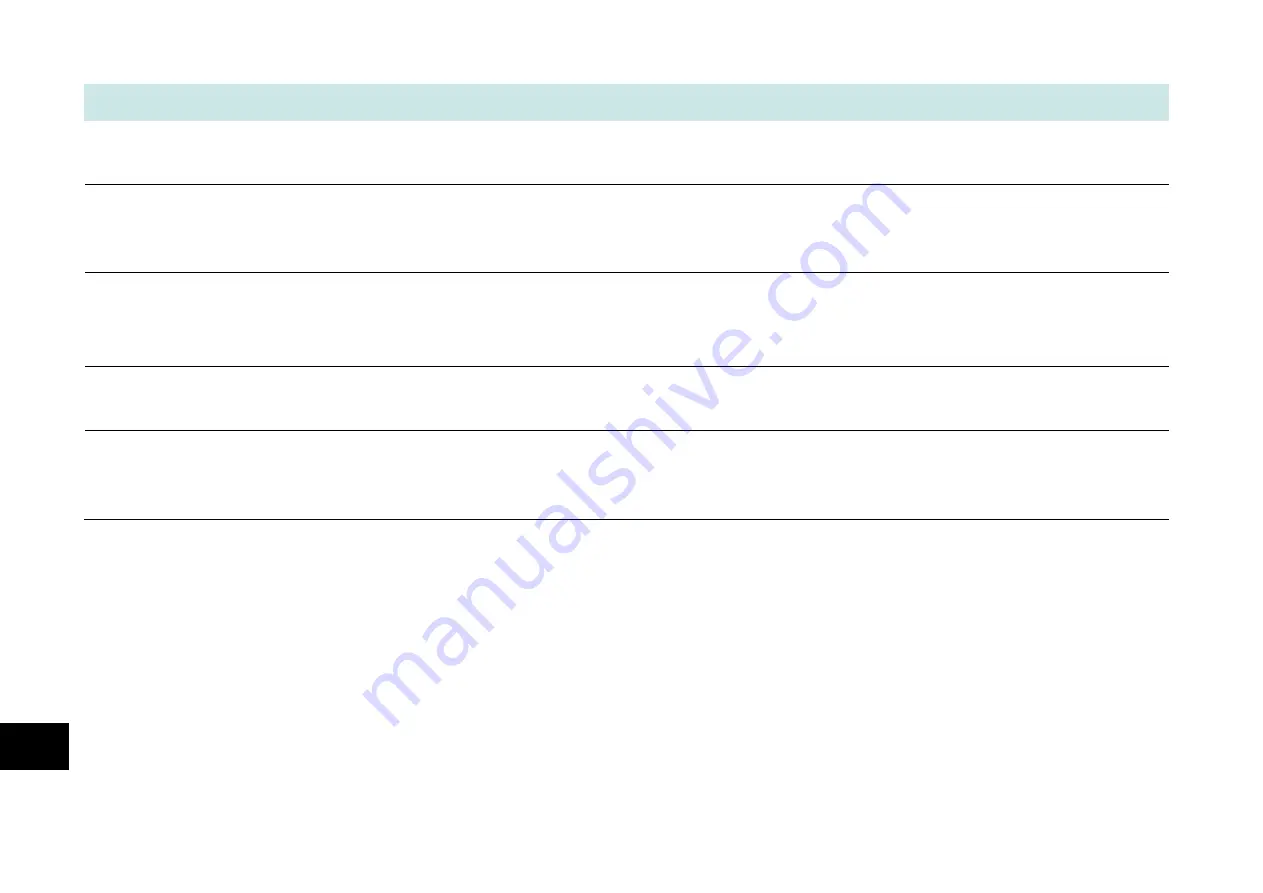
Programming
Page
D-14
890CS Common Bus Supply - Frames B & D; 890CD Common Bus Drive and 890SD Standalone Drive - Frames B, C & D
8
9
10
A
B
C
D
E
1
2
3
4
5
6
7
Parameter Descriptions
COMMS COMMAND
PREF: 95.09
Default: 0000
Range:
0x0000 to 0xFFFF
16-bit Command. Refer to Appendix B: “Sequencing Logic”.
COMMS SEQ
PREF: 95.06
Default: FALSE
Range: FALSE / TRUE
Diagnostic indicating if operating in Remote Sequencing Comms Mode.
If FALSE (0), the Drive may be in Local Sequencing mode or Remote Sequencing Terminal mode.
COMMS REF
PREF: 95.07
Default: FALSE
Range: FALSE / TRUE
Diagnostic indicating if operating in Remote Reference Comms Mode.
If FALSE (0), the Drive may be in Local Reference mode or Remote Reference Terminal mode.
FIREWIRE REF
PREF: 95.11
Default: FALSE
Range:
TRUE / FALSE
This diagnostic indicates if Firewire Ref is the active reference.
COMMS STATUS
PREF: 95.08
Default: 0000
Range:
0x0000 to 0xFFFF
Diagnostic showing the 16-bit Status word as seen by the communications.
Refer to Appendix B: “Sequencing Logic”.