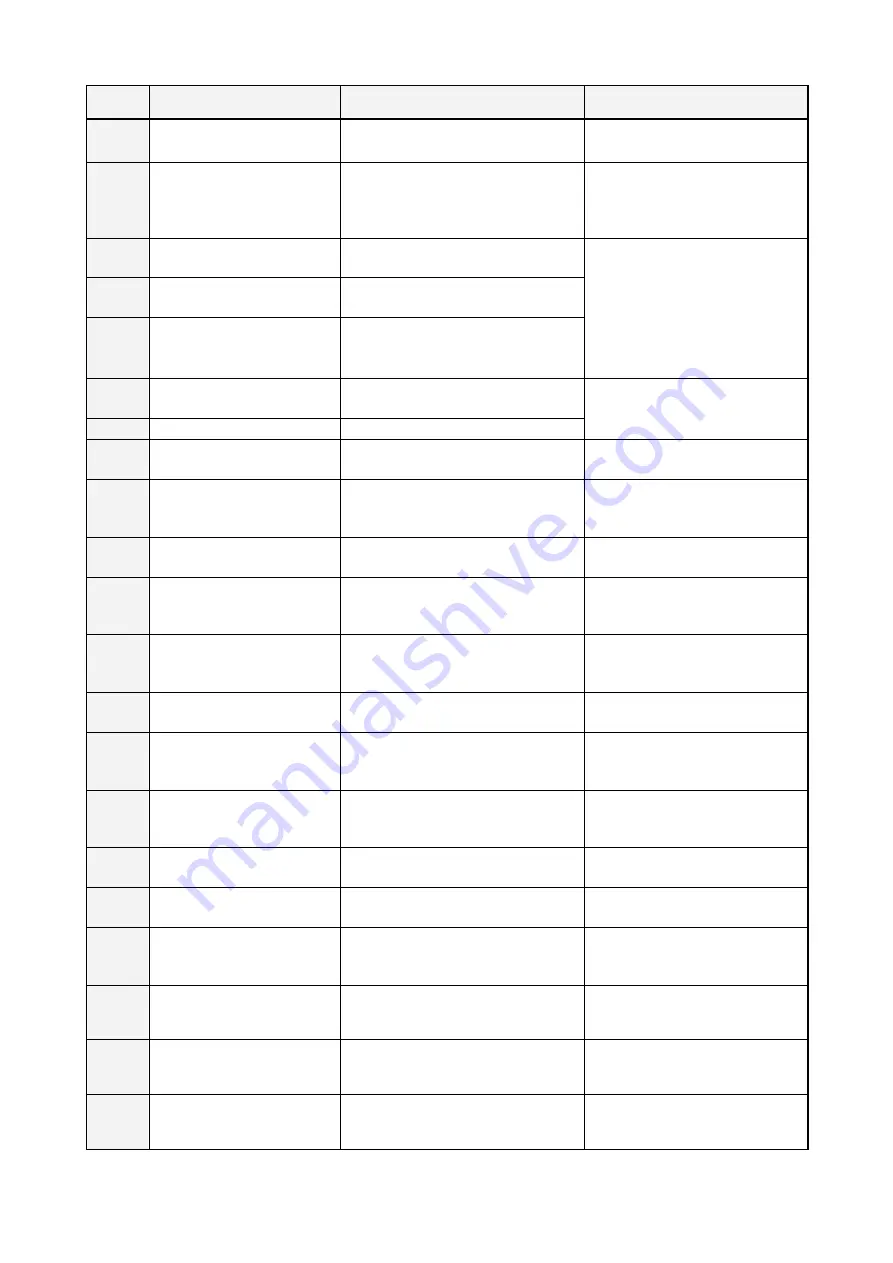
17-8
Error
code
Message
Probable Cause
Remedy
E2220
Arc sensor: Data
communication
Error in controller, or inclusion of noise.
Power to the arc sensor is OFF.
Turn off the power, and newly turn
it on.
E2230
Arc sensor: Amp. Error
Servo driver inside the spin controller
is defective. Error of the motor
temperature inside the spin head.
Remove the cover of the spin
controller and check the error
display. Investigate the cause of
the error.
E2240
Arc sensor: Operation error
Shift amount calculation error due to
error in controller or inclusion of noise.
E2260
Arc sensor: Rotational speed
RPM of the motor inside the spin head
is either too high or too low.
E2270
Arc sensor: Data
communication
Error in controller, or inclusion of
noise.
Power to the arc sensor unit is OFF.
Turn off the power, and newly turn
it on.
E2280
Arc sensor: Detection phase
Detection phase settings are not
consistent.
E2290
Arc sensor: Encoder phase
Encoder phase is out of range.
Press the Cancel key. Check the
detection phase set values.
E2320
Arc sensor: Tool number
error
Tool number 9 or higher is specified in
spin arc sensing range.
Modify the program.
E2330
Arc sensor: Arc sensing is not
available in a parallel
processing program.
Arc sense command is executed
during processing parallel programs.
Change structure of the program.
E2340
Arc sensor: Execution error
(Arc slope)
Arc slope and arc sensing is executed
in same time.
Change structure of the program.
E2350
Spin Sensor: Execution error
(Weaving)
In the "Multi-cooperative robot control"
movement, weaving and spin sensor
were executed at the same time.
Modify the program.
E3020
M-rot reset: position
Due to load inertia, external axis is not
in complete stop by the multi rotation
reset command.
Add DELAY command (about 1 to
2 seconds) in front of RSTREV
command.
E3030
Connect error (Mode)
Not accessible.
Modes do not match.
Change the mode of the slave
robot.
E3030
Connect error (Robot No.)
Not accessible.
The specified slave robot No. is
inadequate.
Check the harmonic movement
settings.
E3030
Connect error (constant)
Not accessible.
Constant of the slave robot has
changed.
Check the settings of the slave
robot.
E3040
Hold (slave err)
The slave robot stopped due to an
error.
Remove cause(s) of the error of
the slave robot.
E3050
Safety holder(slave)
Safety holder of the slave robot is
activated.
Correct the tool interference of the
slave robot.
E3060
Multi-mechanism is not set
Multi-mechanism has not specified.
Calculation area not secured.
On the
Set
menu, click
Management tool
and
System
.
Then add the “Multi-mechanism”.
E3080
COUPLE Timeout
Failed to connect to the master robot
within the preset time period after
executing COUPLE command.
Check the program.
E3100
Please turn on Servo(**)
**is Axis name.
The target independent E-axis servo
power is OFF.
Turn ON the target independent
E-axis servo power, and then
re-start.
E3110
Independent E-axis: Out of
servo off enable section
error(**) **is Axis name.
Servo power off is conducted to the
Independent E-axis to which "Servo
off enable section" is not applicable.
Turn ON the servo power on again,
and then re-start.