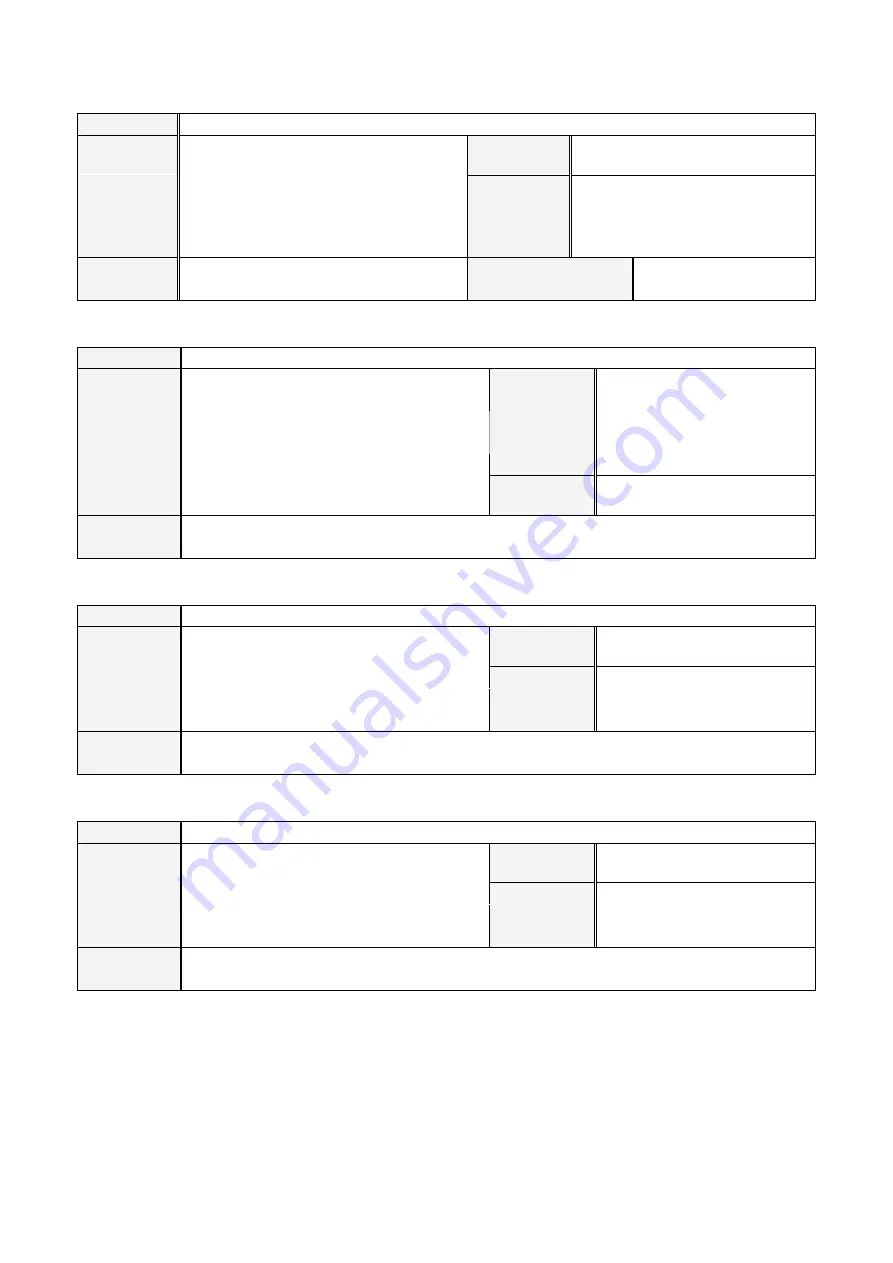
16-12
16-4-13. SET
Format
SET [Variable 1] [Variable 2]
Function
It assigns a real number or variable to another
variable.
Variable 1
Target variable
(GB,LB,GI,LI,GL,LL,GR,LR,GD,GT)
Condition
Standard.
Variable 2
Lock
condition
None.
Assigned value or variable (of the
same type).
Syntax check
None.
Example
Set 10 to variable LR001
SET LR001 = 10
The same command in
conventional models
SETREG
16-4-14. SETEL
Format
SETEL [Variable] = [Data]
Function
It assigns a value to a constituent of the variable
Variable
Target variable
Element (GD, GT)
Condition
None.
Lock condition
None.
X: a point on the X-axis.
Y: a point on the Y-axis.
Z: a point on the Z-axis.
Syntax check
Error if variable to be assigned to is not teaching
point type, 3-D type or robot type variable.
Data
Assignment value or Variable
name (GR, LR, GD, GT)
Example
Set 100 to the element of variable GD001.
SETEL GD.X GD001 = 100
16-4-15. SIN
Format
SIN [Variable] [Data]
Function
It calculates a sine value and assigns the result
to specified variable.
Variable
Variable the calculated value is to
be assigned to.
Condition
Standard.
Data
Lock condition
None.
Syntax check
None.
Calculation or variable (of the
same type)
(Unit: degree)
Example
Calculate sin45 and assign the result to LR001.
SIN LR001 45
16-4-16. SQRT
Format
SQRT [Variable 1] [Variable 2]
Function
It calculates a square root and assigns the result
to specified variable.
Variable 1
Variable the calculated value is to
be assigned to. (GR, LR)
Condition
Standard.
Variable 2
Lock condition
None.
Calculation or variable (of the
same type).
Syntax check
None.
Example
Calculate square root of 2 and then assign the result to LR001.
SQRT LR001 2