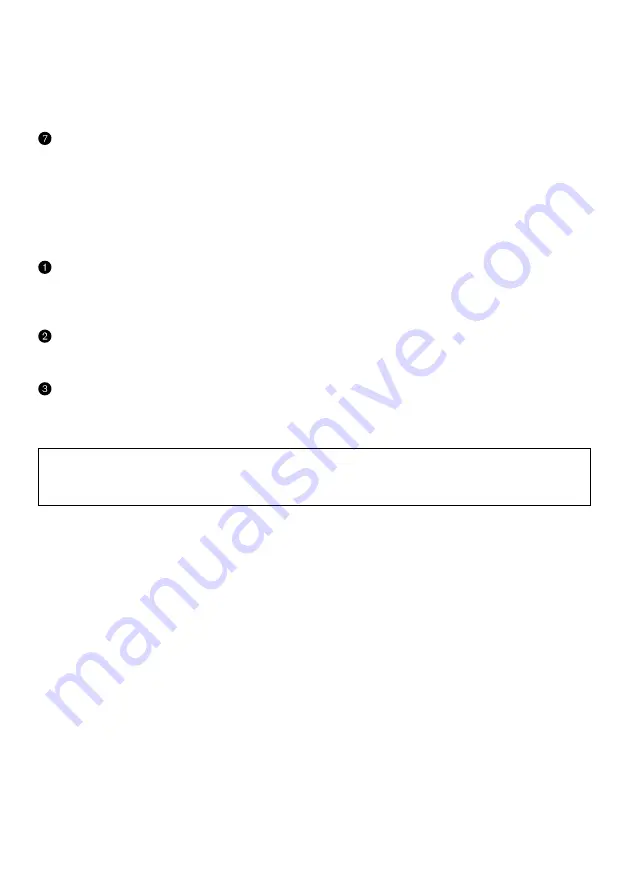
Ottobock | 47
3R60-PRO, 3R60-PRO=ST, 3R60-PRO=KD, 3R60-PRO=HD
2. A continuación, soltar el tornillo sólo hasta que el adaptador de conexión permita un desplaza-
miento.
3. Después, efectuar el desplazamiento deseado para optimizar el montaje de la prótesis.
4. Por último, apretar el tornillo a un par de apriete de 25 Nm e introducir la tapa de cierre. Es im-
prescindible que introduzca la tapa de cierre en la posición correcta.
Una el encaje y la articulación modular de rodilla mediante el adaptador correspondiente (p. ej.
el adaptador de varilla 4R111, 4R41, 4R55, 4R51).
4.1.2 Optimización estática del montaje con el L.A.S.A.R. Posture 743L100
(los siguientes pasos se refieren a la fig. 13)
La alineación básica puede mejorarse de manera considerable con la ayuda del L.A.S.A.R. Posture.
Para conseguir una seguridad suficiente y, al mismo tiempo, un comienzo de la fase de impulsión
más fácil, siga el siguiente procedimiento durante el montaje:
Para realizar la medición de la línea de carga, el paciente con amputación femoral ha de pisar
con el lado protésico la plataforma de fuerza del L.A.S.A.R. Posture y con la otra pierna la
plataforma de compensación de altura. Durante este proceso, el lado con prótesis tiene que
cargarse de modo suficiente (> 35% del peso corporal).
Ahora, debería ajustarse el montaje exclusivamente mediante la modificación de la flexión
plantar
de manera que la línea de carga (línea de láser) pase aproximadamente 10 mm por
delante del eje delantero
inferior
de la rodilla (véase fig. 13).
A continuación, realice la optimización dinámica durante la prueba de marcha (véase el apar-
tado 5).
4.2 Posibilidades de combinación
Información
Todos los componentes protésicos empleados al fabricar una prótesis para las extremidades
inferiores deben cumplir los requisitos en cuanto al peso y el grado de actividad del paciente.
4.3 Ajuste y montaje final
4.3.1 Elaboración del encaje 3R60-PRO=KD
4.3.1.1 Laminado antes de la prueba
Recubra el asiento aislado del muñón con la manga de malla de perlón 623T3 manteniendo una
longitud doble a la del modelo de escayola hasta la mitad de la malla. Retuerza la mitad restante de
la manga de malla en el extremo distal y colóquela también por encima. Para absorber las grandes
fuerzas en la zona de la articulación modular se refuerza gradualmente la armadura con una manga
de vidrio trenzado 616G13. La primera capa se remanga hasta cubrir 2/3 de la longitud del encaje,
a continuación se ata y se vuelve a remangar hasta la mitad de la longitud del encaje. En la zona
distal se tienden 2 capas de tejido de fibra de carbono 616G12 de tal modo que el adaptador 4G70
que se ha de colocar posteriormente tenga la fibra de carbono a modo de substrato sobresaliendo 3
cm de contorno. Coloque por encima dos capas de manga de malla de perlón 623T3. El laminado
se realiza en un procedimiento de colado doble, es decir, el primer colado se lamina hasta 2/3 de
la longitud con resina de laminar Orthocryl 617H19. La parte proximal del encaje se lamina en el
siguiente colado con Orthocryl suave 617H17. Después de haberse endurecido el primer colado
se ponen de nuevo 2 capas de manga de malla de perlón 623T3 antes de laminar la parte proximal
del encaje con Orthocryl suave 617H17.
Summary of Contents for 3R60-PRO HD
Page 3: ...2 3b 3a A B 5 4 F 6 ICR ICR ICR F F ICR ICR D E...
Page 4: ...4 Ottobock 3R60 PRO 3R60 PRO ST 3R60 PRO KD 3R60 PRO HD 7 7 9 8 10 10 mm 25 Nm 11b 11a...
Page 151: ...Ottobock 151 3R60 PRO 3R60 PRO ST 3R60 PRO KD 3R60 PRO HD 4 4 3R60 EBS PRO 3S107 519L5 4 5...
Page 152: ...152 Ottobock 3R60 PRO 3R60 PRO ST 3R60 PRO KD 3R60 PRO HD ISO 10328 5 5 1 5 2 93 42 IX I VII...
Page 160: ...160 Ottobock 3R60 PRO 3R60 PRO ST 3R60 PRO KD 3R60 PRO HD 4 4 3S107 519L5 4 5...