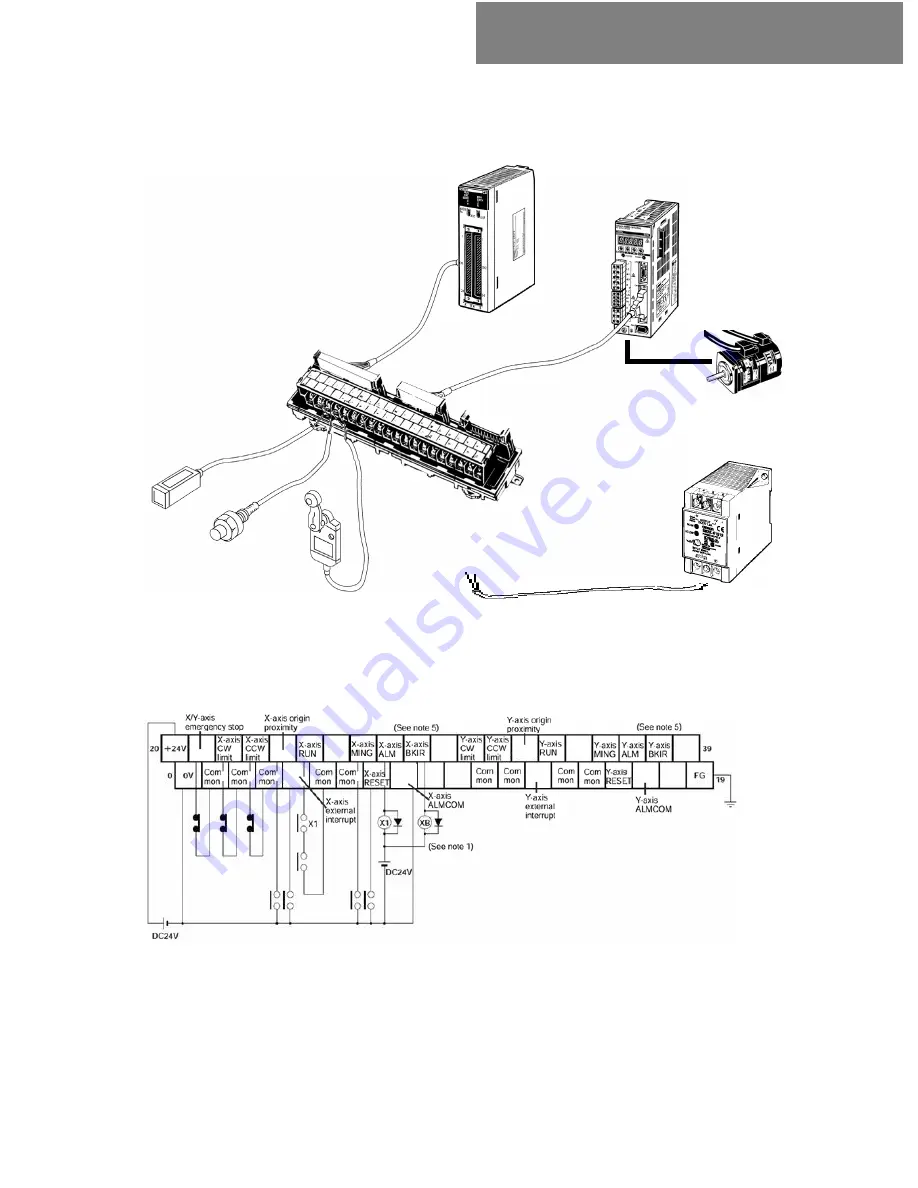
Programmable Controller
Position Control Unit
CS1W-NC413
XW2Z-100J-A7
Dedicated Connection
Cable
XW2B40J62B
Servo Terminal Unit
Servo Driver
R88D-WT01HL
XW2Z-100J-B4
Dedicated Connection Cable
Connection Example
2-3. Creating I/O Table
Set CX-Programmer online and create I/O table.
For wiring of junction unit, see W series user’s manual I531-E1 “2-7 Servo Junction Unit
and Cable Specification”.
*1. The XB contact is used to turn ON/OFF the electromagnetic brake.
*2. Do not connect unused terminals.
*3.The 0 V terminal is internally connected to the common terminals.
*4. The following crimp terminal is applicable: R1.25-3 (round with open end).
*5. Allocate BKIR (Brake Lock) to CN1 pin 27.
2-5 Position Control Unit
CS1W-NC113/133/213/233/413/433
Summary of Contents for FB LIBRARY -
Page 1: ......
Page 14: ...2 1 Controller Link Unit CJ1W CLK21 V1...
Page 23: ...2 2 DeviceNet Slave DRT2 Series DRT2...
Page 31: ...2 3 Position Control Unit CJ1W NCF71...
Page 42: ...2 4 Position Control Unit CJ1W NC113 133 213 233 413 433...
Page 49: ...2 5 Position Control Unit CS1W NC113 133 213 233 413 433...
Page 57: ...2 6 Inverter 3G3MV A2 AB A4 3G3RV A2 A4...
Page 71: ...2 7 Servo Driver R88D WT WT H WT HL R7D AP H AP L...
Page 84: ...2 8 RFID ID Sensor V600 H...
Page 95: ...2 9 Vision Sensor F160 C10...
Page 105: ...2 10 2D Code Reader V530 R2000 R160 R150V3...
Page 118: ...2 11 Smart Sensor ZX SF11 ZX LD40 ZX LDA11 N...
Page 129: ...2 12 Temperature Controller E5ZN 2...
Page 139: ...2 13 Temperature Control Unit CJ1W TC001 101 003 103 002 102 004 104...