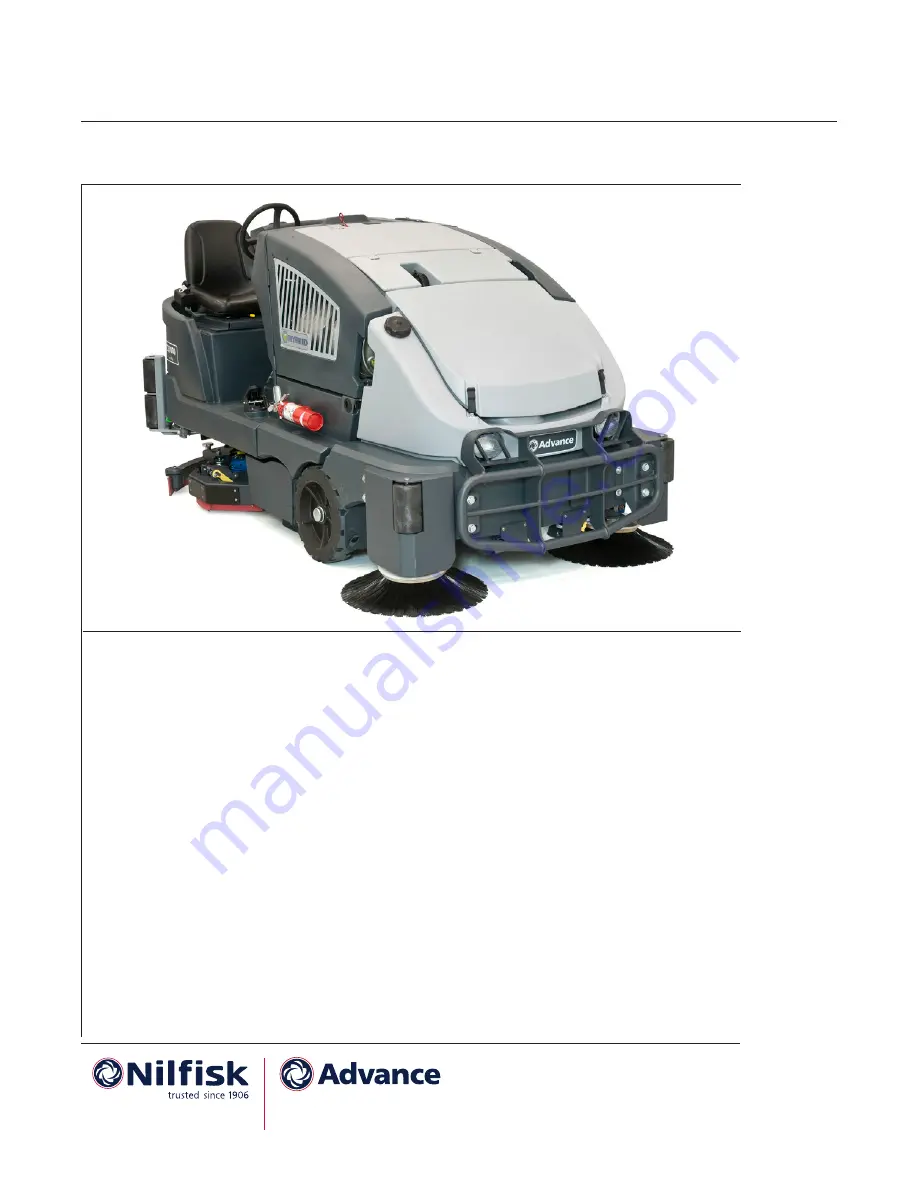
CS7000™
05/11 Revised 09/15 Form No. 56043151
Service Manual
Advance
56383115(48 Fuel Cell EcoFlex)
56509000(48 LPG Hybrid),
56509001(48 Diesel Hybrid)
56509002(48 Battery)
56509006(48 LPG Hybrid EcoFlex)
56509007(48 Diesel Hybrid EcoFlex)
56509008(48 Battery EcoFlex)
56511001(48 Gasoline/Petrol Hybrid
EcoFlex)
56511540(48 LPG LEV Hybrid)
56511541(48 LPG LEV Hybrid EcoFlex)
English
Nilfisk
56509003(1200 LPG Hybrid)
56509004(1200 Diesel Hybrid)
56509005(1200 Battery),
56511002(1200 Gasoline/Petrol
Hybrid)
56384409(1200 LPG Hybrid),
556384410(1200 Battery)
56511564(1200 LPG LEV Hybrid)
Summary of Contents for CS7000 Fuel Cell EcoFlex
Page 147: ...Electrical System 147 Service Manual CS7000 56509170 Rev L Sheet 1 of 9 ...
Page 148: ...Electrical System 148 Service Manual CS7000 56509170 Rev L Sheet 2 of 9 ...
Page 149: ...Electrical System 149 Service Manual CS7000 56509170 Rev L Sheet 3 of 9 ...
Page 150: ...Electrical System 150 Service Manual CS7000 56509170 Rev L Sheet 4 of 9 ...
Page 151: ...Service Manual CS7000 151 Electrical System 56509170 Rev L Sheet 5 of 9 ...
Page 155: ...Electrical System 155 Service Manual CS7000 56509170 Rev L Sheet 9 of 9 ...
Page 357: ...Steering System 357 Service Manual CS7000 Steering System Wiring Diagram 36 V From Key Switch ...