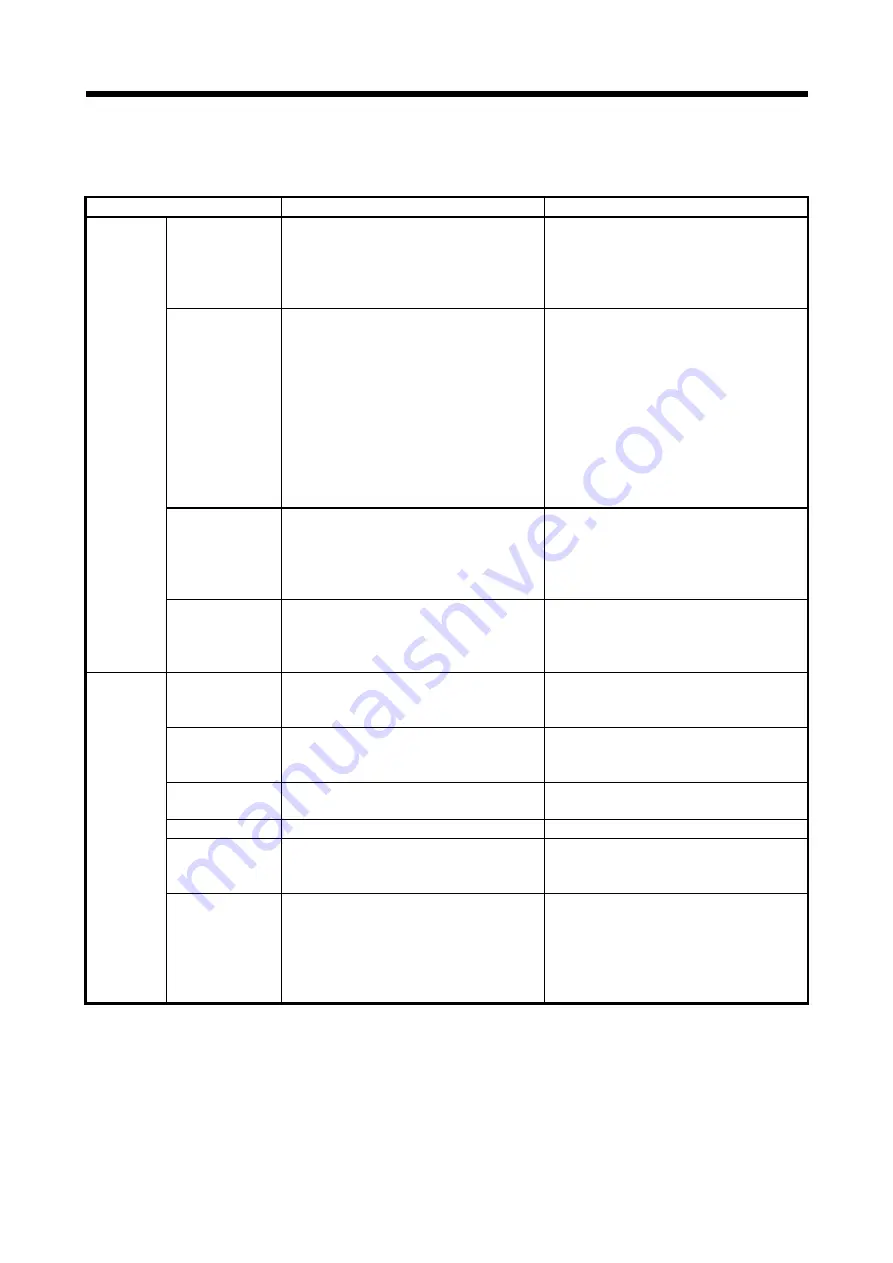
APP - 44
APPENDICES
Table 5.1 Differences between virtual mode switching method and advanced synchronous
control method (continued)
Item
Virtual mode switching method
Advanced synchronous control method
Gear
• Number of input side teeth : 1 to 65535
• Number of output side teeth : 1 to 65535
• Rotation direction
: Forward/Reverse
• Numerator of gear : -2147483648 to
2147483647
• Denominator of gear : 1 to 2147483647
• Rotation direction
: Set by a sign of the
numerator of gear
Clutch
(Note-1)
• Clutch mode
ON/OFF, Address 1, Address 2, One-shot,
External input
• Smoothing
Time constant (Exponential system),
Slippage amount (Exponential system/Linear
system)
• Clutch mode
Clutch command ON/OFF, Clutch command
leading edge, Clutch command trailing edge,
One-shot OFF, Address mode, High speed
input request.
(Set mode for ON condition and OFF condition
individually.)
• Smoothing
Time constant (Exponential system/Linear
system), Slippage (Exponential system/Linear
system)
Speed change gear
• Speed change ratio : 0 to 655.35%
• Smoothing
: Exponential system
• Numerator of speed change ratio:
-2147483648 to 2147483647
• Denominator of speed change ratio:
1 to 2147483647
• Smoothing: Linear system
Transmission
module
Differential gear
Use main shaft and auxiliary input.
(Main shaft side: +, Auxiliary shaft side: -)
Use composite main shaft gear and composite
auxiliary shaft gear.
(Select a composite method for each inputs from
"Input+/Input-/No input (0)".)
Type
Roller shaft, Ball screw shaft, Rotary table shaft,
Cam shaft
Cam shaft only.
(The linear cam can be controlled as same as
the ball screw shaft etc.)
Phase
compensation
• Advance time: -2147483648 to 2147483647[
μ
s]
• Time constant: 0 to 32767
[Number of operation cycle]
• Advance time: -2147483648 to 2147483647[
μ
s]
• Time constant: 0 to 65535 [ms]
Stroke limit
operation
An error is detected by stroke limit. However, the
operation is continued.
An error is detected by stroke limit and the
operation is stopped.
Stop command
Invalid
Valid
Cam/ball screw
switching
Provided
(Operate the ball screw by inputting the
command pulse from the drive axis.)
None
(Operate the ball screw by the positioning control
after the synchronous control stop of each axis.)
Output
module
Cam axis starting
point
1) Cam reference position setting ON
Start from the point corresponding to "current
value within 1 cam shaft revolution is 0".
2) Cam reference position setting OFF
Restore the current value within 1 cam shaft
revolution based on the current feed value.
Select the one which is restored, from "cam axis
current value per cycle", "cam reference position"
or "cam axis current feed value", in the
parameter.
(The initial setting is same as 1) in Virtual mode
switching method.)
Summary of Contents for Q172DSCPU
Page 1: ......
Page 19: ...A 18 MEMO ...
Page 39: ...3 4 3 SYNCHRONOUS CONTROL MODULE MEMO ...
Page 129: ...5 50 5 INPUT AXIS MODULE MEMO ...
Page 199: ...7 60 7 SYNCHRONOUS CONTROL MEMO ...
Page 310: ......
Page 311: ......