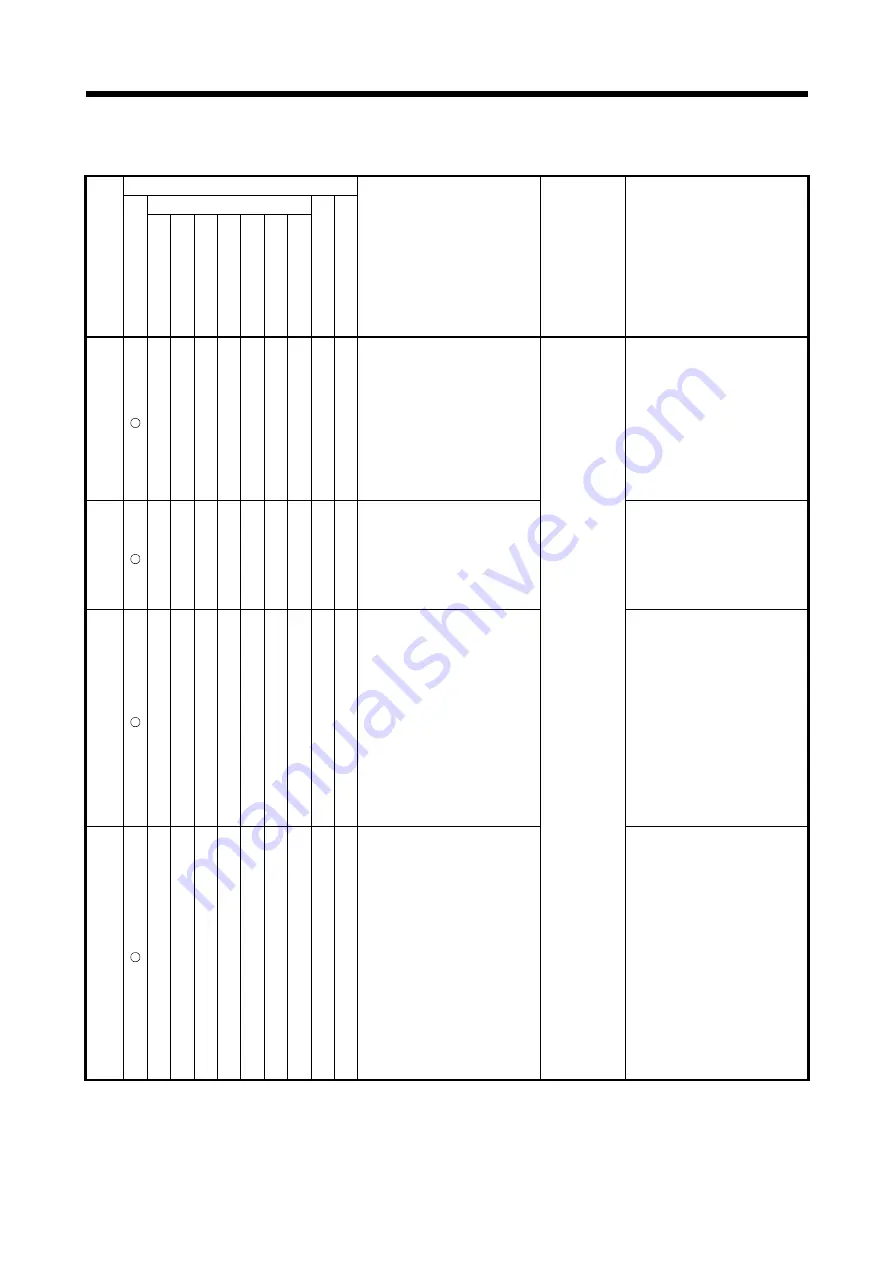
APP - 33
APPENDICES
Table 1.14 Synchronous control output axis error (1700 to 1799) list (Continued)
Control mode
Command generation axis
Error
code
Synchronous control
Positioning
Fixed-pitch feed
Speed
Constant-speed
JOG
Position follow-up control
Speed control with fixed
position stop
Synchronous encoder
Servo input axis
Error cause
Error
processing
Corrective action
1766
• The synchronous parameter
"[Pr.464] Setting method of cam
axis current value per cycle
(150n)" is set to other
than 0 to 3.
• "3: Current value per cycle after
auxiliary shaft gear" is
established when the auxiliary
shaft does not exist.
• Set a value within the range of 0
to 3.
• Set other than "3: Current value
per cycle after auxiliary shaft
gear" when the auxiliary shaft
does not exist.
1767
• The synchronous parameter
"[Pr.468] Cam axis current value
per cycle (Initial setting)
(150n, 150n)"
is set to other than 0 to (Cam
axis length per cycle - 1).
• Set within the range of 0 to (Cam
axis length per cycle - 1).
1768
• Cam axis current value per cycle
corresponding to the current
feed value at synchronous
control start could not be
restored when the synchronous
parameter "[Pr.462] Cam axis
position restoration object
(150n)" was "0: Cam
axis current value per cycle
restoration".
(Occurs in reciprocated cam
pattern)
• Start synchronous control after
moving the current feed value as
to fit within the stroke of two-way
operation cam pattern.
• Set the cam reference position
as to fit within the stroke of two-
way operation cam pattern.
1769
• Restoration could not be
completed when the
synchronous parameter "[Pr.462]
Cam axis position restoration
object (150n)" was "2:
Cam axis current feed value
restoration", because the
difference between the restored
cam axis current feed value and
the current feed value at
synchronous control start (pulse
command unit) was larger than
the servo parameter "In-position
range".
Synchronous
control does
not start.
• Start synchronous control after
calculating the cam axis current
feed value to be restored, using
the cam position calculation
function, and moving the current
feed value.
• Set a larger setting value for the
servo parameter "In-position
range", if the current value is too
small (such as 0)."
Summary of Contents for Q172DSCPU
Page 1: ......
Page 19: ...A 18 MEMO ...
Page 39: ...3 4 3 SYNCHRONOUS CONTROL MODULE MEMO ...
Page 129: ...5 50 5 INPUT AXIS MODULE MEMO ...
Page 199: ...7 60 7 SYNCHRONOUS CONTROL MEMO ...
Page 310: ......
Page 311: ......