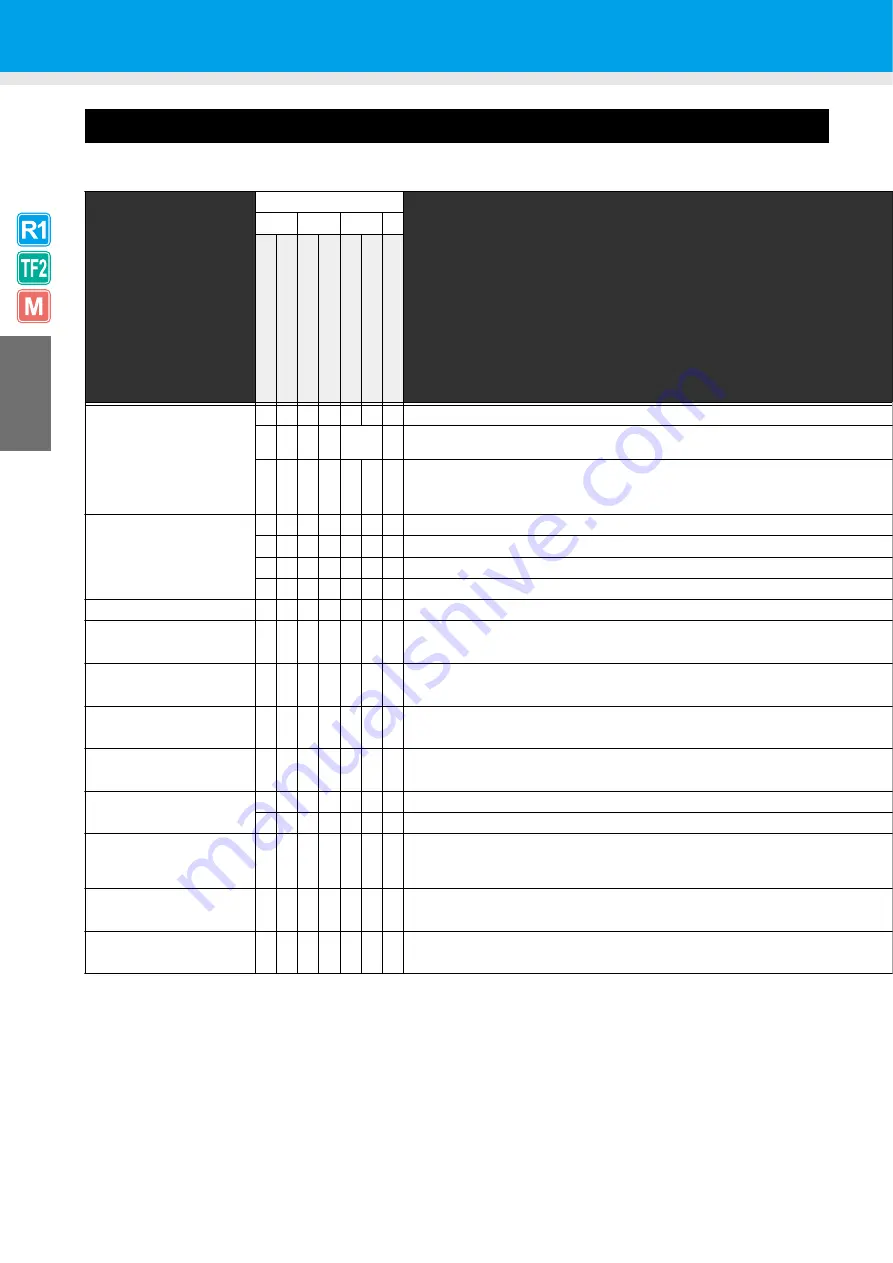
2-14
Set Items
The cutting condition set items differ according to the tool.
Set Item
Tool Type
Set value
A
B
C
Swivel cutter
Pen
Ta
ngen
tial cu
tter
Re
ci
proc
at
in
g cu
tte
r
(*
1)
Radius cutter
Crea
se ro
ller
Milling tool
SPEED
○ ○ ○
○ ○
2, 5, 10, 15, 20, 25, 30, 35, 40, 45, 50 (cm/s)
○
○
*1
*1. Valid for Model R1 only.
0.2, 0.5, 1, 2, 5, 10,15 , 20, 25, 30, 35, 40, 45, 50 (cm/s)
○
0.1 ~ 3 (step 0.1cm/s)
3.0 ~ 10 (step 1cm/s)
10.0 ~ 50 (step 5cm/s)
PRESSURE
○ ○
20 ~ 100 (step 5g) 100 ~ 400 (step 10g)
○
300 ~ 1500 (step 100g)
○
*2
*2. Available only when the VIBRATION cutting condition is set OFF if cutter holder 2N is mounted Unit B in Model R1.
500 ~ 1500 (step 100g) *Fixed 1500g in setting VIBRATION
○ ○
1000 ~ 5000 (step 100g)
ACCELE
○ ○ ○ ○ ○ ○ ○
0.1 ~ 0.5 (step 0.1G)
F OFFSET
○ ○ ○
0 ~ 2.50 (step 0.05mm)
E OFFSET
○ ○ ○
0 ~ 2.50 (step 0.05mm)
UP ANGLE
○ ○ ○ ○
0 ~ 45 (step 1
°
)
RING DIS
○ ○ ○ ○
0 ~ 2.50 (step 0.05mm)
PRESS COR
○ ○
○
0 ~ 500 (step 100g)
○
0 ~1000 (step 100g)
Y PRESS
○
-5000 ~ +5000 (step 100g)
OFFSET
○
0 ~ 2.50 (step 0.05mm)
VIBRATION
○
OFF, 1 ~ 5
*2
Summary of Contents for CF3-1610
Page 7: ...vi ...
Page 110: ...3 20 ...
Page 124: ...4 14 ...
Page 164: ...6 30 ...
Page 165: ...D201768 14 29062009 ...
Page 166: ...NH FW 3 30 Printed in Japan MIMAKI ENGINEERING CO LTD 2009 ...