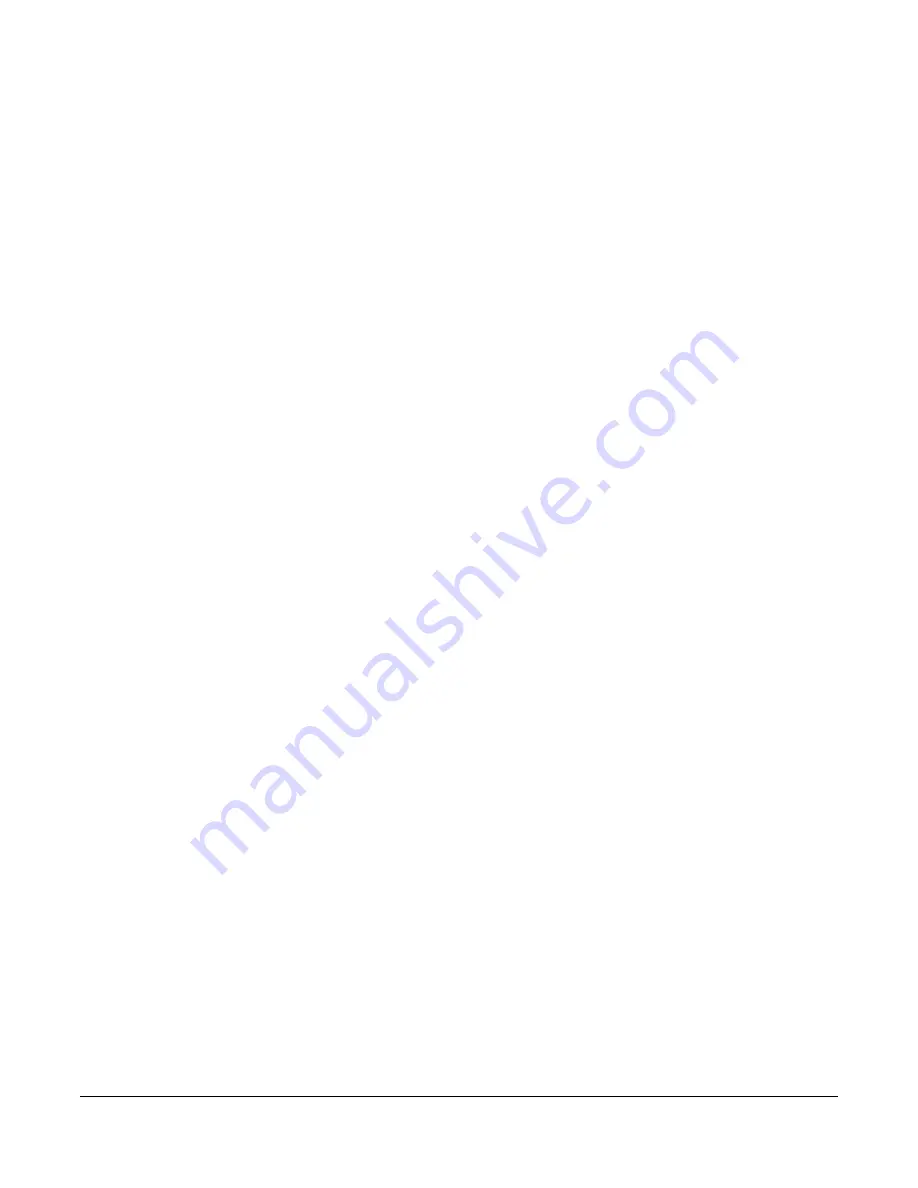
IMPULSE•G+/VG+ Series 4 Technical Manual
November 2022
Page 98
5.2.16 No-Load Brake Hoist
The No-Load Brake Hoist mode is a VG+ feature that provides a start and stop sequence designed specifically for
hoists without a mechanical load brake. This mode is enabled automatically when the Motion is set to NLB Hoist
(A01-03 = 2). This will also automatically set the Stopping Method to No-Load Brake (B03-03 = 6).
Start
The start sequence begins by building up torque in the motor to a predefined level within the C08-01 (Torque
Compensation Time) timer. This level is determined by several factors which are defined below. During the C08-02
time, the VFD is monitoring current to motor. The current feedback equation must be satisfied within the time set in
C08-02 (IFB OK Time). If it is not, a BE2 (No-Current) fault will be displayed on the keypad and the VFD will stop
outputting voltage to the motor. The brake will remain closed.
Once the brake has been commanded to release, the VFD output remains in Load Float for the amount of time
programmed into C08-04. During C08-04, the VFD waits for the brake to completely open and watches encoder
feedback. If the amount of feedback is less than the setting in C08-05 (Roll Back Count), then the VFD proceeds to
the BE3 check. If it is not, a BE1 fault is displayed on the keypad and the sequence stops. For the BE3 check, if the
brake opened mechanically, then the encoder feedback must be greater than or equal to the value programmed in
C08-07 (BE3 Detect Count) within the time set in C08-06 (BE3/Alt Torq Tim). If it is not, then a BE3 fault is
displayed. By the time the VFD has completed the BE3 check, there should be a significant amount of motor shaft
movement and the start sequence is complete.
Stop
The stop sequence begins when the run command has been removed and the output frequency has decelerated to
zero. Once at zero speed, the motor maintains a Load Float position for the duration of C08-10 (Load Float Time).
During the Load Float time, run commands in either direction are accepted and will begin accelerating immediately
in the commanded direction, thereby skipping the start sequence entirely. The Load Float Timer is reset after each
new run command. Once the Load Float Timer expires, the brake output command is removed (thereby closing the
brake) and Load Float is maintained for the time set in C08-11 (Brake Set Delay) to allow the brake to fully close.
Once the Brake Delay Time has expired, the BE6 check is executed. The BE6 check monitors encoder feedback
while the load is being transferred from the motor to the brake and compares it to C08-13 (BE6 Max Count). The
encoder feedback must not exceed the number of counts in C08-13 within the C08-12 (BE6 Detect Timer) time. If it
does (meaning the load slipped through the brake), a BE6 alarm is displayed on the keypad and the VFD will reset
its Load Float position and maintain its new position. Run commands will still be accepted with the exception of a
reduced speed in the up direction set by C08-18 (BE6 Up Speed Limit) and the NLB stop sequence will begin again
once the run command had been removed.
Torque Proving
Factor 1: On the first run command after power up, or after any fault which causes the stop sequence to be
skipped, the start sequence by default uses the value programmed in C08-16, the Initial Brake Release torque.
Factor 2: Once the system has completed a successful start and stop, a new Brake Release Torque value is used.
This value is one that has been memorized and stored into memory during the stop sequence. It is equivalent to
the amount of torque required for the motor to hold the load on the hook in Load Float with the brake released.
Some benefits of stored Load Float torque for the next brake release are:
•
Faster response to run commands when VFD is in Base Block Status.
•
Upon brake release, shaft rotation begins in the direction of the run command.
If the stored value is less than the programmed value in C08-03 (Minimum Brake Release torque), C08-03 is used
as the next brake release value. If the feature must be disabled, C08-03 will override C08-16 if it is a greater value.