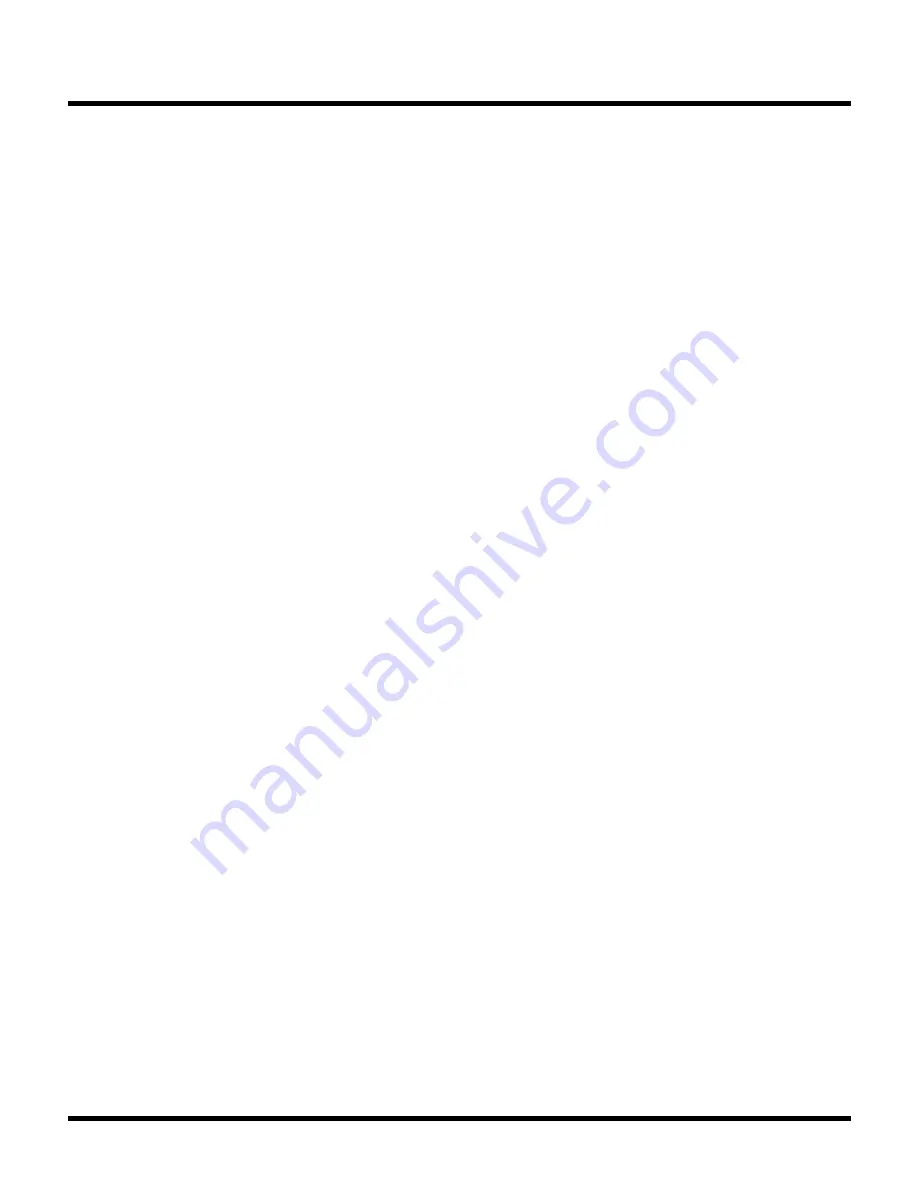
LTC3882-1
48
Rev A
For more information
APPLICATIONS INFORMATION
node rise and fall times should be minimized. The following
PCB design priority list will help ensure proper topology.
1. Place a ground or DC voltage layer between a power
layer and a small-signal layer. Generally, power planes
should be placed on the top layer (4-layer PCB), or top
and bottom layer if more than 4 layers are used. Use
wide/short copper traces for power components and
avoid improper use of thermal relief around power
plane vias to minimize resistance and inductance.
2. Low ESR input capacitors should be placed as close
as possible to switching FET supply and ground con-
nections with the shortest copper traces possible. The
switching FETs must be on the same layer of copper
as the input capacitors with a common topside drain
connection at C
IN
. Do not attempt to split the input
decoupling for the two channels, as a large resonant
loop can result. Vias should not be used to make these
connections. Avoid blocking forced air flow to the
switching FETs with large size passive components.
3. If using a discrete FET driver, place that IC close to the
switching FET gate terminals, keeping the connecting
traces short to produce clean drive signals. This rule
also applies to driver IC supply and ground pins that
connect to the switching FET source pins. The driver
IC can be placed on the opposite side of the PCB from
the switching FETs.
4. Place the inductor input as close as possible to the
switching FETs. Minimize the surface area of the switch
node. Make the trace width the minimum needed to
support the maximum output current. Avoid copper
fills or pours. Avoid running the connection on multiple
copper layers in parallel. Minimize capacitance from
the switch node to any other trace or plane.
5. Place the output current sense resistor (if used) im-
mediately adjacent to the inductor output. PCB traces
for remote voltage and current sense should be run
together back to the LTC3882-1 in pairs with the small-
est spacing possible on any given layer on which they
are routed. Avoid high frequency switching signals
and ideally shield with ground planes. Locate any filter
component on these traces next to the LTC3882-1,
and not at the Kelvin sense location. However, if DCR
sensing is used, place the top resistor (R1, Figure 25)
close to the switch node.
6. Place low ESR output capacitors adjacent to the sense
resistor output and ground. Output capacitor ground
connections must feed into the same copper that con-
nects to the input capacitor ground before connecting
back to system ground.
7. Connection of switching ground to system ground,
small-signal analog ground or any internal ground plane
should be single-point. If the system has an internal
system ground plane, a good way to do this is to cluster
vias into a single star point to make the connection. This
cluster should be located directly beneath the IC GND
paddle, which serves as both analog signal ground and
the negative sense for V
OUT1
. A useful CAD technique
is to make separate ground nets and use a 0Ω resistor
to connect them to system ground.
8. Place all small-signal components away from high
frequency switching nodes. Place decoupling capaci-
tors for the LTC3882-1 immediately adjacent to the IC.
9. A good rule of thumb for via count in a given high cur-
rent path is to use 0.5A per via. Be consistent when
applying this rule.
10. Copper fills or pours are good for all power connec-
tions except as noted above in rule 3. Copper planes
on multiple layers can also be used in parallel. This
helps with thermal management and lowers trace
inductance, which further improves EMI performance.
Output Current Sensing
The I
SENSE
+
and I
SENSE
–
pins are high impedance inputs to
internal current comparators, the current-sharing loop and
telemetry ADC. The common mode range of the current
sense inputs is approximately 0V to 5.5V. Continuous linear
operation is provided throughout this range. Maximum
differential current sense input (I
SENSE
+
– I
SENSE
–
) is 70mV,
including any variation over temperature. These inputs
must be properly connected in the application at all times.
To maximize efficiency at full load the LTC3882-1 is designed
to sense current through the inductor’s DCR, as shown in
Figure 25. The DCR of the inductor represents the small
amount of DC winding resistance of the copper, which