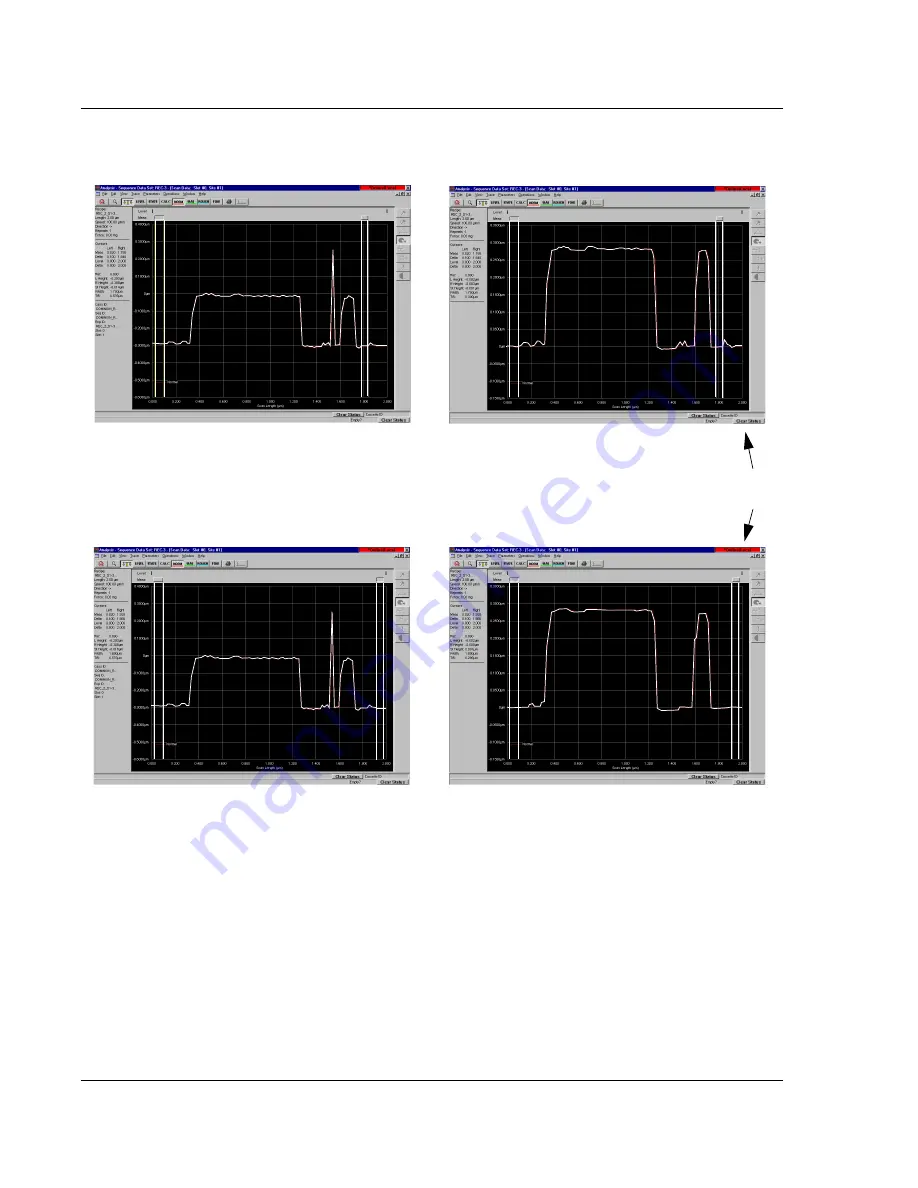
Scan Recipes - Creating and Editing a Scan Recipe
KLA-Tencor P-16+ / P-6 User’s Guide
3-46
KLA-Tencor Confidential
0142530-000 AB
3/13/09
The median filter is a major component of the Glitch Removal process used on data in
the Analysis screen for both 2D and 3D data.
The available filter sizes (kernels) for 2D data are: 1 x 3, 1 x 5, and 1 x 7 points.
The available filter sizes (kernels) for 3D data are: 3 x 3, 5 x 5, and 7 x 7 points.
To add a filter or change the filter size on existing data, use the following procedure:
1.
From the Analysis screen, click
Edit
to display its menu.
2.
Select
Recipe
. This opens the recipe used to generate the data.
Figure 3.36
Median Filter Application in Glitch Removal
1 x 3
point median filter
before and after application
BEFORE APPLICATION
AFTER APPLICATION
1 x 7
point median filter
before and after application
BEFORE APPLICATION
AFTER APPLICATION
Notice how much smoother the 1 x 7
filter (below) made the scan than that of
the 1 x 3 filter (above).