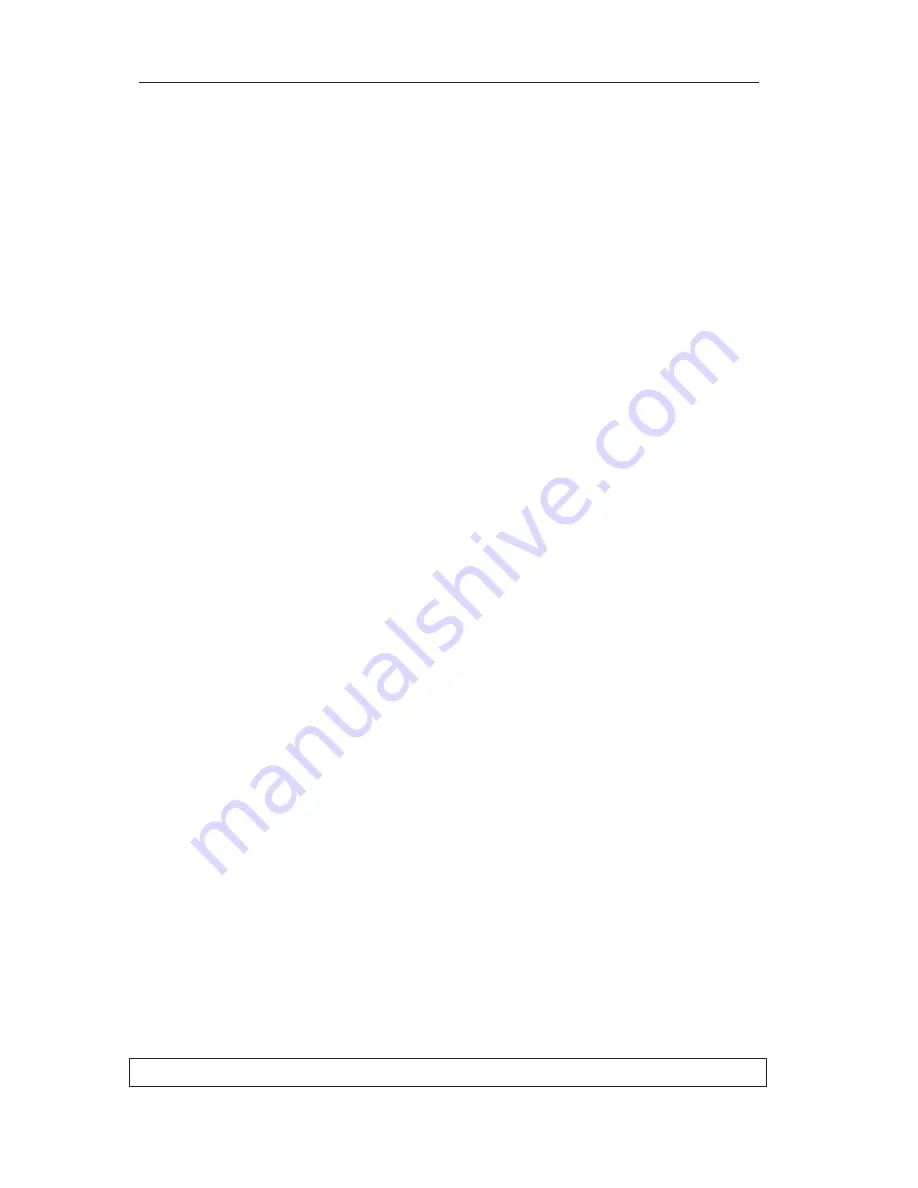
74
ORTHOPANTOMOGAPH
OP
2D
4. Troubleshooting
If the reference values are correct, but feed back values
are not, the Tubehead and/or the Generator board may
be faulty and must be replaced.
If there are no reference signals check the cabling be-
tween the L1800 Generator board and L1700. Replace
if faulty.
Error E3 (CFG Data lost)
CAUSE
L1200, CPU board, has lost the calibration data and
settings.
SOLUTION
Recalibrate L1200, see
5. S2terminal and Service
Functions
.
The required calibrations are:
- IP address will default, must be reset if another ad-
dress is required (see installation manual)
- tubehead calibration: service command "calib"
- line voltage calibration
- set the serial number
If the error message reappears after recalibration,
L1200 is faulty and needs to be replaced. See
7.5 Re-
placing circuit boards
.
Error E4 (Tubehead too hot or too cold)
CAUSE A
The tube head has overheated (> 55°C) or is too cold
(<5°C).
SOLUTION A
Wait for the tubehead to cool down if hot or warm up if
too cold.
When the tubehead reaches the right temperature the
error message will automatically disappear. Note that
this could take over 45 minutes.
Note that you will not be able to clear the error mes-
sage until the tube head has cooled to the correct tem-
perature. If the error message appears even if the unit
has not been used a lot, switch the unit off and then on
again.
CAUSE B
The tube heat signal is missing.
SOLUTION B
If the error message never clears check the path of the
tube heat signal. The tubehead and/or the generator
board may be faulty and must be replaced.
Summary of Contents for ORTHOPANTOMOGAPH OP 2D
Page 2: ......
Page 4: ...IV ORTHOPANTOMOGAPH OP 2D Contents...
Page 24: ...14 ORTHOPANTOMOGAPH OP 2D 2 Unit Description 2 3 Unit dimensions...
Page 32: ...22 ORTHOPANTOMOGAPH OP 2D 2 Unit Description...
Page 33: ...2 Unit Description ORTHOPANTOMOGAPH OP 2D 23 2 6 Block diagram...
Page 34: ...24 ORTHOPANTOMOGAPH OP 2D 2 Unit Description 2 7 Fuse diagram...
Page 38: ...28 ORTHOPANTOMOGAPH OP 2D 2 Unit Description...
Page 43: ...3 Circuit Boards L1200 ORTHOPANTOMOGAPH OP 2D 33 L1200 Block Diagram...
Page 46: ...36 ORTHOPANTOMOGAPH OP 2D 3 Circuit Boards L1500 L1500 Block diagram...
Page 50: ...40 ORTHOPANTOMOGAPH OP 2D 3 Circuit Board L1600 L1600 Block diagram...
Page 54: ...44 ORTHOPANTOMOGAPH OP 2D 3 Circuit Boards L1700 L1700 Block Diagram...
Page 57: ...3 Circuit Boards L1800 ORTHOPANTOMOGAPH OP 2D 47 L1800 Block diagram...
Page 61: ...3 Circuit Boards P1910 ORTHOPANTOMOGAPH OP 2D 51 P1910 Block diagram...