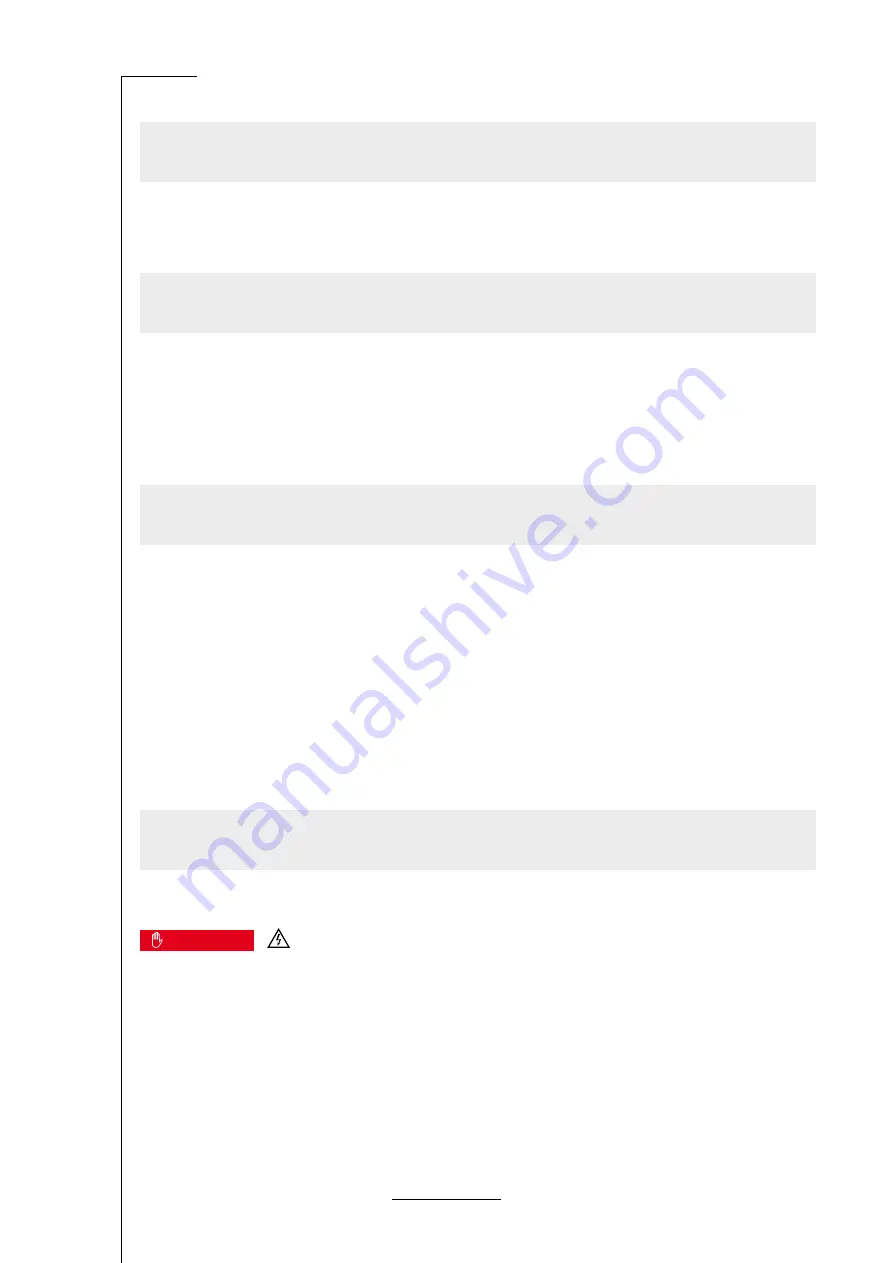
item Controller BL 1-04 /C
― Product manual
52
9 Electrical installation
This chapter provides all of the relevant information for the electrical installation of a servo drive of the BL 4000-C series with
an integrated "Safe Torque Off (STO)" safety function.
9.1 Notes concerning the safe and EMC- compliant installation
9.1.1 Explanations and terminology
Electromagnetic compatibility (EMC) or electromagnetic interference (EMI) includes the following requirements:
▪ Sufficient
immunity
of an electrical installation or an electrical device against external electrical, magnetic or electromag
-
netic interferences via cables or the environment.
▪ Sufficiently small
unwanted emission
of electrical, magnetic or electromagnetic interference from an electrical installation
or an electrical device to other devices in the vicinity via cables or the environment.
9.1.2 General information about electromagnetic compatibility
The interference emission and interference immunity of a servo drive always depend on the overall drive concept consisting of
the following components:
▪ Power supply
▪ Servo drive
▪
Motor
▪ Electromechanical system
▪ Configuration and type of wiring
▪ Superordinate control system
In order to increase interference immunity and to decrease interference emissions, the servo drive has integrated filters so
that it can be used without additional shielding and filtering devices in most applications.
9.1.3 Proper wiring
Comply with following instructions to ensure the safe and EMC-compliant set-up of the drive system:
DANGER
Dangerous electrical voltage!
For safety reasons, all of the PE earth (ground) conductors must be connected prior to the initial operation of the system.
The shields must be connected on both sides.
The EN 61800-5-1 regulations concerning protective earthing (grounding) must be complied with during the installation.
▪ In order to keep the leakage currents and losses in the motor connecting cable as small as possible, the servo drive should
be located as close to the motor as possible (see also section 9.1.4 Operation with long motor cables on page 53).
▪ The motor cable and angle encoder cable must be shielded.
▪ Connect the shield of the motor cable to the back panel of the control cabinet by way of suitable shield terminals. The
unshielded cable end should not be longer than 80 mm.
▪ The mains-end PE connector must be connected to the PE connection point of the supply connector [X9].