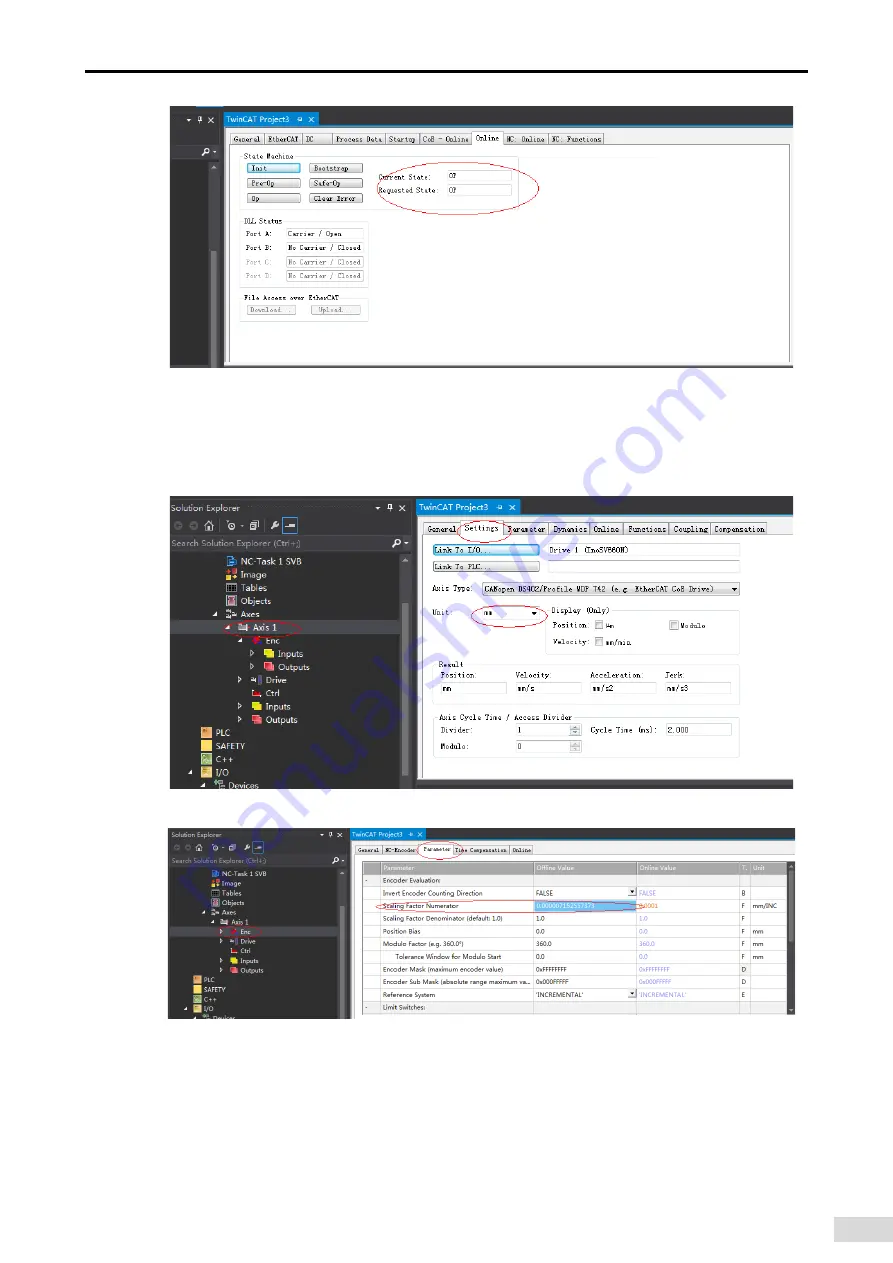
-363-
10 Application Cases
7) Controlling the servo drive through NC controller or PLC program
7-1) Servo drive running in the CSP mode
a)
Set the unit.
The unit is "mm" during testing.
b)
Set the scaling factor.
■
Scaling factor: distance corresponding to the encoder pulses per position feedback
For example, 8388608 pulses per motor revolution corresponds to the distance of 60 mm, and the scaling
factor is: 60/8388608 = 0.000007152557373 mm/Inc.