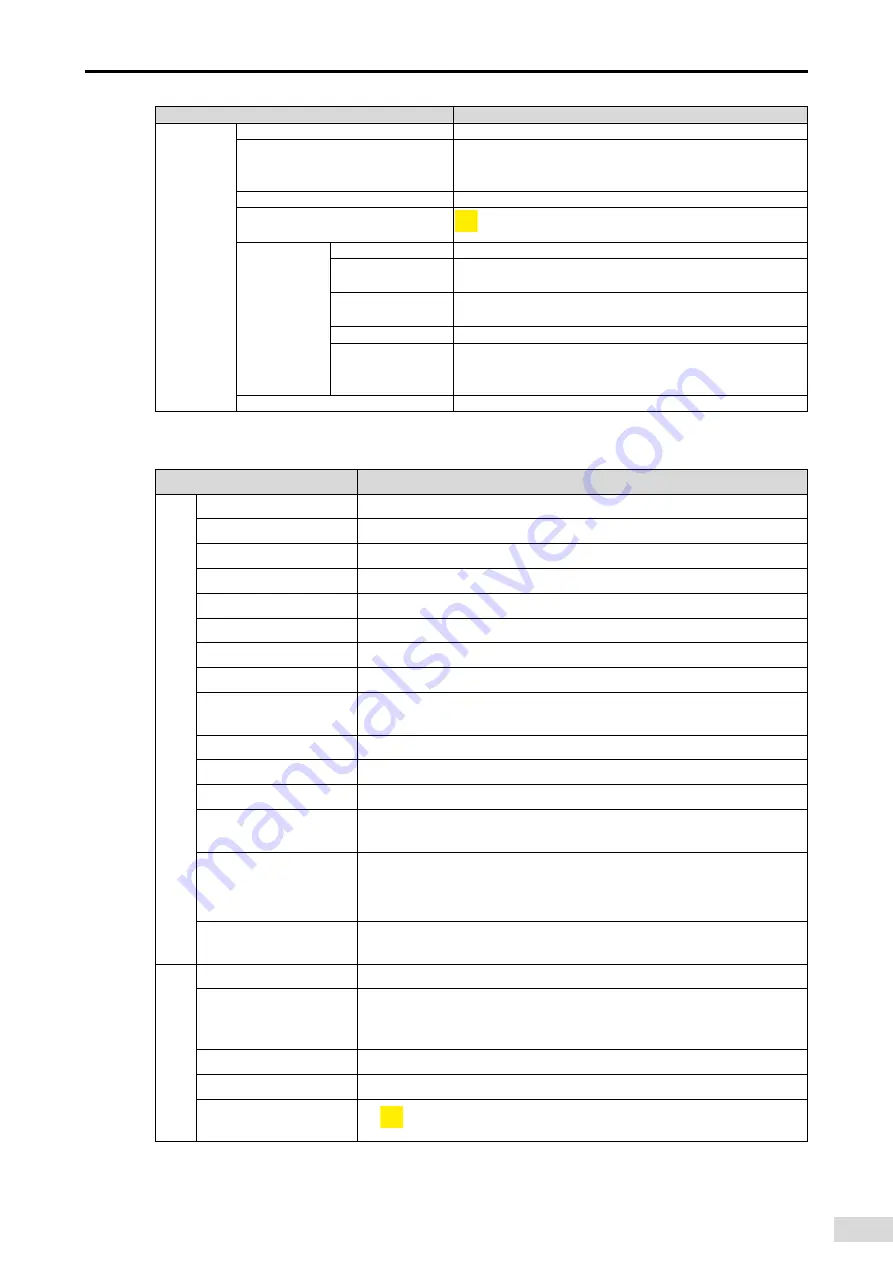
-21-
1 Product Information
Item
Description
Built-in
functions
Overtravel (OT) prevention
Stop immediately when P-OT and N-OT activated
Protective functions
Protections against overcurrent, overvoltage, undervoltage,
overload, main circuit detection error, heatsink overheat,
overspeed, encoder error, CPU error, and parameter error
LED display
Main power CHARGE indicator, 5-digit LED display
Vibration suppression
Five notches (including two adaptive notches), 50 Hz to 5000
Hz
Communication
function
Connection protocol RS232
Communication
protocol
EtherCAT
Multi-station
communication
Maximum number of slaves: 255
Axis address setting
No physical knob, set to 0 to 255 by software
Functions
Including status display, user parameter setting, monitoring
information display, fault tracking display, jog and auto-tuning,
and speed/torque reference signal observation
Others
Gain auto-tuning, fault log, jog
3
Technical specifications of EtherCAT communication
Item
Specifications
Basic perf
ormanc
e of E
therCA
T slav
e s
tation
Communication protocol
EtherCAT protocol
Available services
CoE (PDO, SDO)
Synchronization mode
DC - Distributed clock
Physical layer
100BASE-TX
Baud rate
100 Mbit/s (100Base-TX)
Duplex mode
Full duplex
Topological structure
Ring and linear
Transmission medium
Shielded Cat 5e network cable or better
Transmission distance
Less than 100 m between two nodes (with proper environment and proper
cables)
Number of slaves
65535 by protocol, equal to or less than 100 in actual use
EtherCAT frame length
44 bytes to 1498 bytes
Process data
A maximum of 1486 bytes per Ethernet frame
Synchronous jitter of two
slaves
< 1 μs
Refresh time
About 30 μs for 1000 DI/DOs
About 100 μs for 100 servo axes
Different refresh time for different interfaces
Communication code error
rate
10
-10
Ethernet standard
EtherCA
T c
onfigur
ation unit
Number of FMMU units
8
Number of storage
synchronization
management units
8
Process data RAM
8 KB
Distributed clock
64-bit
EEPROM capacity
32 Kbit
Initialization data written through EtherCAT master
[1] Install the servo drive in environments that meet the allowable ambient temperature range. When it is installed
inside an electric cabinet, the temperature inside the cabinet must also be within this range.