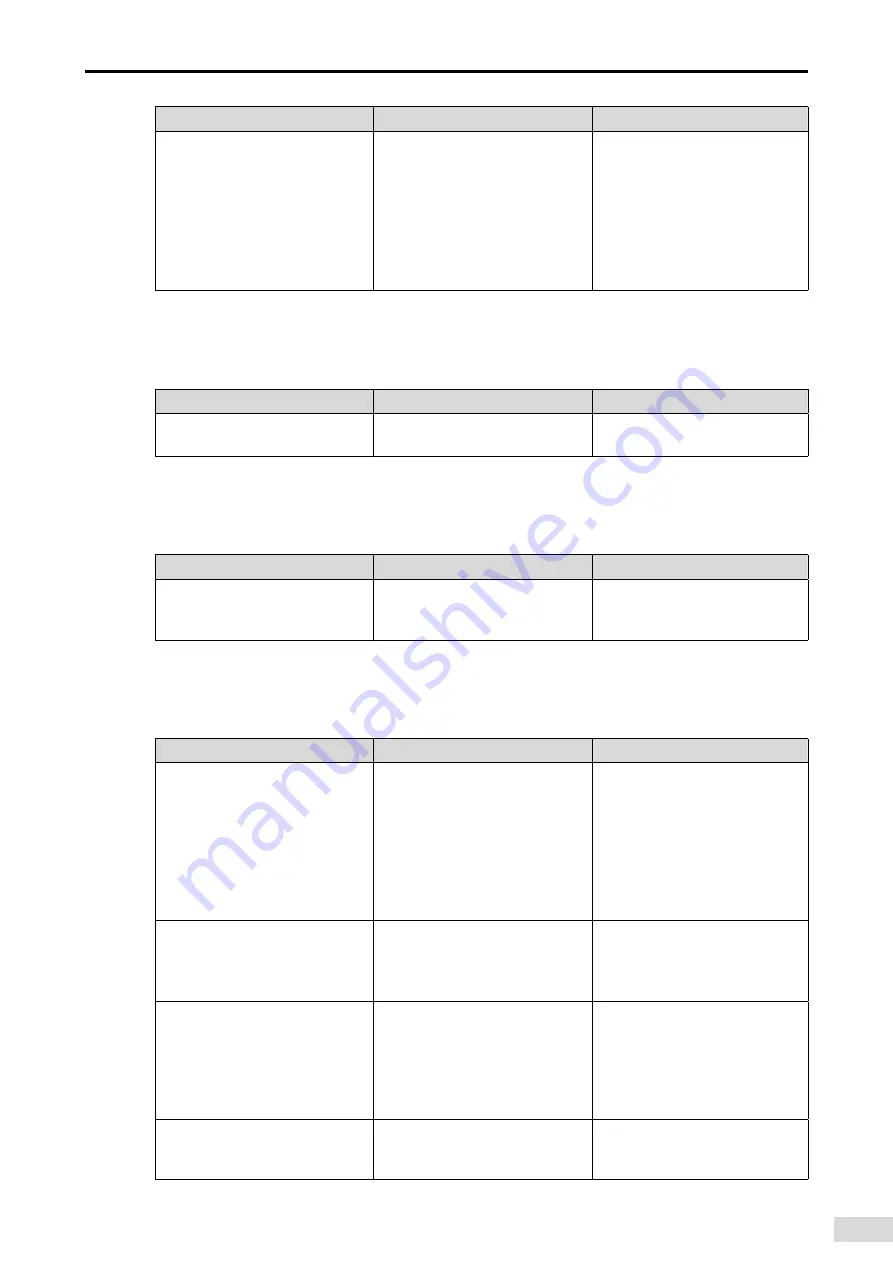
-319-
9 Troubleshooting
Root Cause
Confirming Method
Solution
The FPGA speed measurement is
abnormal.
Check whether the bit9 of H0B-30 is 1.
◆
The speed feedback is abnormal,
check whether the encoder
version (H00-04) is proper.
◆
Replace the encoder cables.
◆
The encoder cables suffer from
interference. Re-connect the
grounding cable and the shielded
cable or install a magnetic ring.
■
E602.0: Angle auto-tuning error
Direct cause:
Abnormal jitter occurs on the encoder feedback during angle auto-tuning.
Root Cause
Confirming Method
Solution
An encoder feedback error occurs.
Check if the encoder communication
suffers from interference.
Check the wiring of the encoder
hardware.
■
E602.2: Wrong UVW phase sequence detected during angle auto-tuning
Direct cause:
A wrong UVW phase sequence is detected during angle auto-tuning.
Root Cause
Confirming Method
Solution
The UVW cables are connected
reversely, which is detected during
angle auto-tuning.
-
Exchange the cables of any two
phases and perform auto-tuning again.
■
E620.0: Motor overload
Direct cause:
The accumulative heat of the servo motor reaches the fault threshold.
Root Cause
Confirming Method
Solution
1. The motor and encoder cables are
connected improperly.
Check the wiring among the servo
drive, servo motor and encoder
according to the correct wiring
diagram.
Connect cables according to the
correct wiring diagram.
It is recommended to use the cables
provided by Inovance.
If you use customized cables, ensure
such cables are made and connected
based on the hardware wiring
instructions.
2. The load is too heavy. The motor
keeps outputting the effective torque
higher than the rated value.
Check the overload characteristics of
the servo drive or servo motor.
Check whether the average load ratio
(200B-0DH) keeps exceeding 100.0%.
Replace with a high-power servo
drive and a matching servo motor.
Reduce the load and increase the
acceleration/deceleration time.
3. The acceleration/deceleration is
too frequent or the load inertia is too
large.
Calculate the mechanical inertia ratio
or perform inertia auto-tuning, and
view the value of 2008-10h (Load
inertia ratio).
Confirm the single running cycle when
the servo motor runs cyclically.
Increase the acceleration/
deceleration time during single
running.
4. The gain is improper or the stiffness
level is too high.
Observe whether the motor vibrates
and generates abnormal noise during
running.
Adjust the gain.