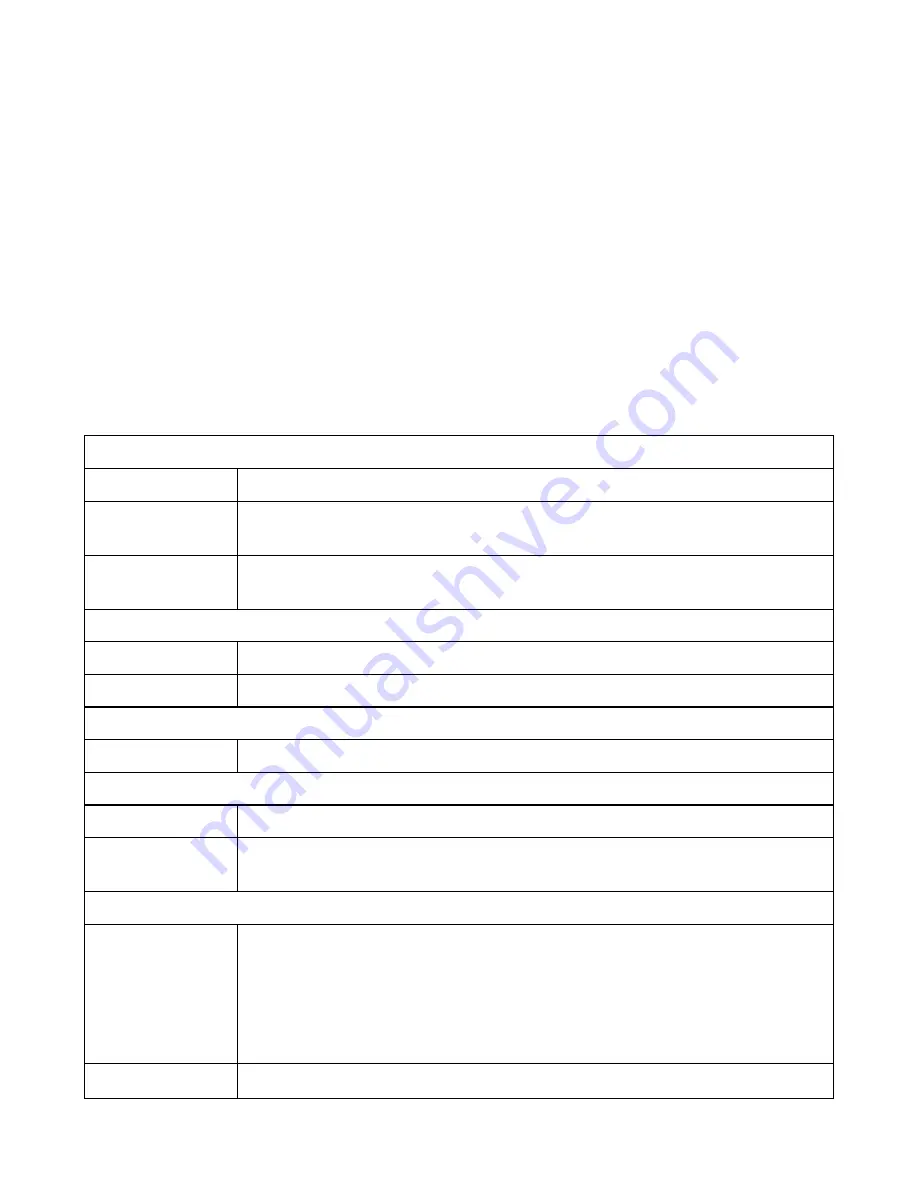
CHAPTER
6
Additional Information
Learn about strategic information related to the Honeywell Vertex™ Edge Detector.
Specifications
OVERALL SYSTEM DIMENSION
Size
76” x 24” x 35”
Weight - Full
loaded condition
Full ~900lbs (~408kg)
Weight - Empty
rack
Empty ~655lbs (~297kg)
ANALYZER
Size
22” x 13” x 6”
Weight
≤ 27lbs (12kg)
POWER REQUIREMENTS
Operating voltage /-10% (under load) @ 50/60Hz: 15A, single phase
POWER CONSUMPTION
Normal condition
1.1k Watt
Maximum
condition
≤ 1.4k Watt
DISPLAY AND OUTPUTS
Visual
15.6” wide screen monitor with capacitive touch interface Display gas
reading, alarm & instrument status real-time base Provide real-time trend
chart and gas event snapshot trend chart Event logging including
maintenance/instrument fault and gas alarm Multiple searching option for
the event LED indicator: Normal (Green), Alarm 1 (Red), Alarm 2 (Red), Fault
(Yellow)
Digital
TCP/IP and RTU Modbus, OPC (Option)
Vertex Edge System
122
User Manual
Summary of Contents for Vertex Edge
Page 1: ...Vertex Edge 72 POINT CONTINUOUS MONITOR ...
Page 2: ......
Page 6: ......
Page 19: ...Chemcassette 1 Chemcassette directional flow Vertex Edge System 18 User Manual ...
Page 29: ...Installation Drawings Vertex Edge System 28 User Manual ...
Page 46: ......
Page 59: ...Vertex Edge System 58 User Manual ...
Page 63: ...Vertex Edge System 62 User Manual ...
Page 69: ...Vertex Edge System 68 User Manual ...
Page 91: ...Vertex Edge System 90 User Manual ...
Page 96: ...Vertex Edge System 95 User Manual ...
Page 98: ...1 Main power ON OFF switch 2 Analyzer power switches Vertex Edge System 97 User Manual ...
Page 165: ... September 2021 1998 2002_EN_RevA1_VertexEdge_UserManual Vertex Edge System 164 User Manual ...