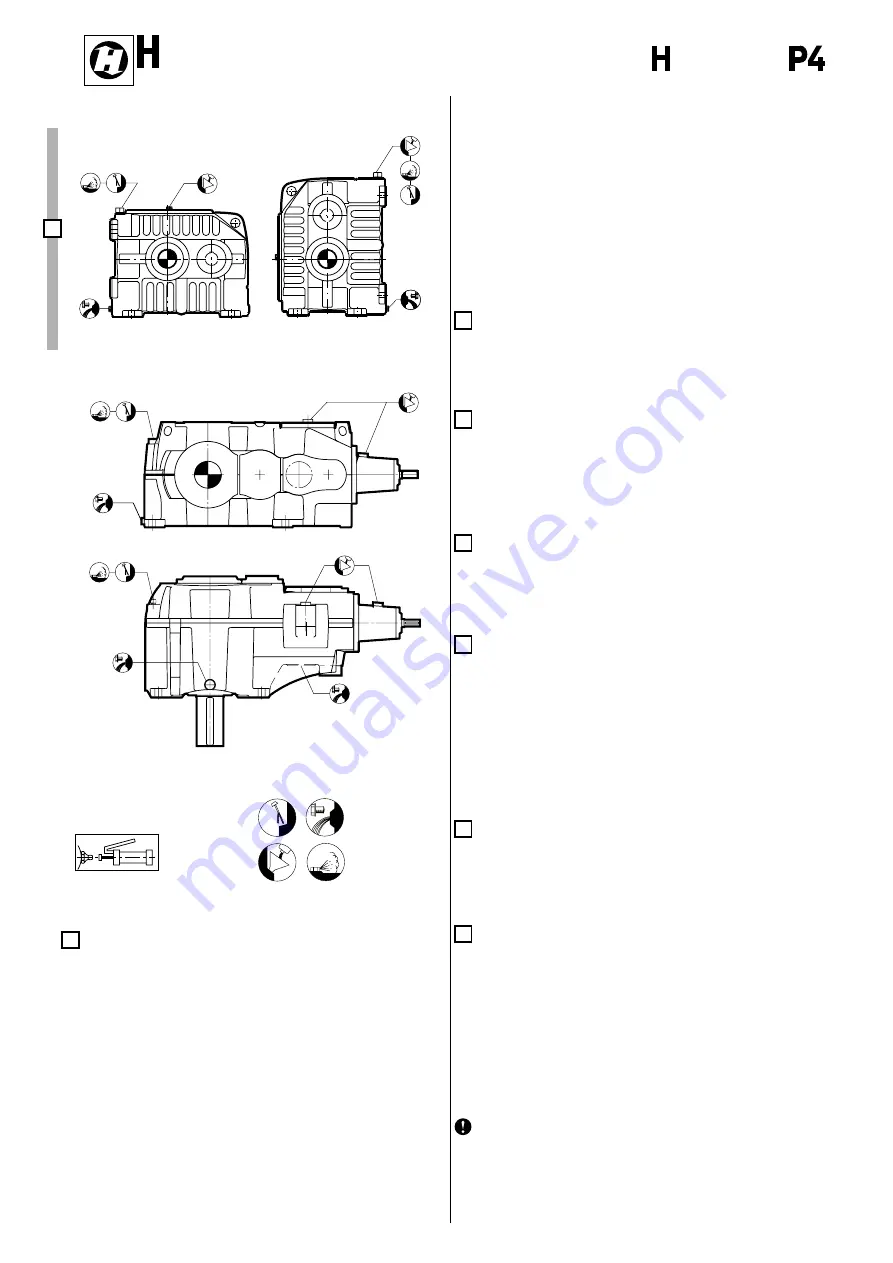
6.5. THE FIRST OIL FILLING
(see fig. 5)
Fill units only after final installation, especially gear units with vertical
downwards shafts, to prevent oil splashing over drywell during handling.
Fill the gear unit exclusively through the oil filling open-
ing which is provided in the inspection cover for that
purpose. In that way, all bearings are lubricated with
fresh oil.
Note :
- Additional oil filling of the bearing housing.
4-stage horizontal gear units with right angle shafts
(QHR.4) and 3- and 4-stage vertical gear units with
right angle shafts (QVR.3 + QVR.4) require on initial
oil filling also an additional oil filling of the bearing
housing.
See special sticker on gear unit.
The additional oil quantity is mentioned on the
certified drawing and on the sticker.
M
M
M
M
M
M
- Oil filling of a gear unit with M1 or M3 motor base.
Units with horizontal shafts (QH ..) equipped with a motorbase M1 and
M3 must be filled on initial filling with a small quantity of oil through the
inspection cover located in the top face of the gear unit (see special sticker
on gear unit).
If easy access to the oil filler plug is prevented through lack of space
between the motor base and the gear unit upper face, the motor base
should be raised following removal of the belt.
For gear units with M1 motor base the normal oil filling plug is located at
the side of the output shaft, opposite the side where the dipstick is
located.
For gear units with M3 motor base the normal oil filling plug is located at
the side of the dipstick.
If the gear unit is filled with storage oil, it has to be drained and it may in
some instances be necessary to rinse the gear unit with the selected oil before
starting up. Check with the oil supplier.
6.6. GREASE SELECTION
(see table page 36)
Use only high quality greases, with EP-additives and consistency
NLGI-Grade 3.
Greases with EP-additives and consistency NLGI-Grade 2 may be used for re-
greasable labyrinth type seals and grease lubricated lower bearing of the
low speed shaft.
6.7. GREASE LUBRICATION POINTS
(see fig. 5)
All greasing points for bearings which are not oil lubricated and for labyrinth
seals are equipped with nipples according to DIN 71412 and have been
filled before shipment.
The total number of nipples is indicated on the nameplate.
Some built-on backstops are grease lubricated.
For detailed information refer to appropriate leaflet supplied with this
manual.
6.8. OIL DRAINING
(see fig. 5)
Drain the oil while unit is still warm.
To facilitate oil drai-
ning, remove dipstick. Drain units having a large oil volume through drain
plug. Use portable pump. With some executions a small quantity of oil
remains beneath the high speed bearings. This oil can be drained by means
of a second drain plug (1).
6.9. VENTILATION
(see fig. 5)
To prevent pressure build-up, the gear unit is provided with a breather which
is generally integrated in the dipstick.
Take care and check regularly that this breather
does not become clogged.
For some applications, the dipstick with breather hole is replaced by one
without breather hole in combination with an anti-dust or anti-humidity
breather.
7. COOLING
Heat generated in the gear unit due to friction and churning of the oil, must
be dissipated through the housing into the environment.
It is important not to decrease the heath dissipation capacity of the housing.
Regularly clean the surface of the housing.
7.1. SEPARATE AIR COOLING
7.1.1. Fans
One or two fans may be mounted on gear unit shafts.
Check regularly that the air inlet and the air
outlet are not obstructed.
Fans need no special maintenance, except occasional cleaning.
7.1.2. Air-oil coolers
The service manual of the lubrication and cooling system gives detailed
information about the air-oil cooler.
7.2. SEPARATE WATER COOLING
All water cooling systems must be connected to a non-calcareous water
supply. See also service manual on lubrication and cooling system and/or
technical leaflets on specific instrumentation. The use of seawater must be
specified with the order; coolers suited for use of seawater are available.
When unit is not operating and freezing temperatures may occur, water must
be drained from cooling system. Drain facilities have to be provided by end
user.
Unless otherwise stipulated, the water flow indicated on the dimensional
drawing is the required rate for water at 20 C (70 F).
According to load, ambient temperature and the water temperature a lower
rate will suffice. Adjust waterflow to obtain an oil working temperature bet-
ween 60 and 80 C (140 and 180 F).
9
ansen
dipstick
oil filling
oil draining
ventilation
grease lubrication
points
Type and position of the
stickers : refer to certified
drawing and gear unit
FIG. 5
T R A N S M I S S I O N S
ansen
®
- Single stage gear units
(1) see 6.8
QHP.1
QHP.1W
- Multi stage gear units
M
n