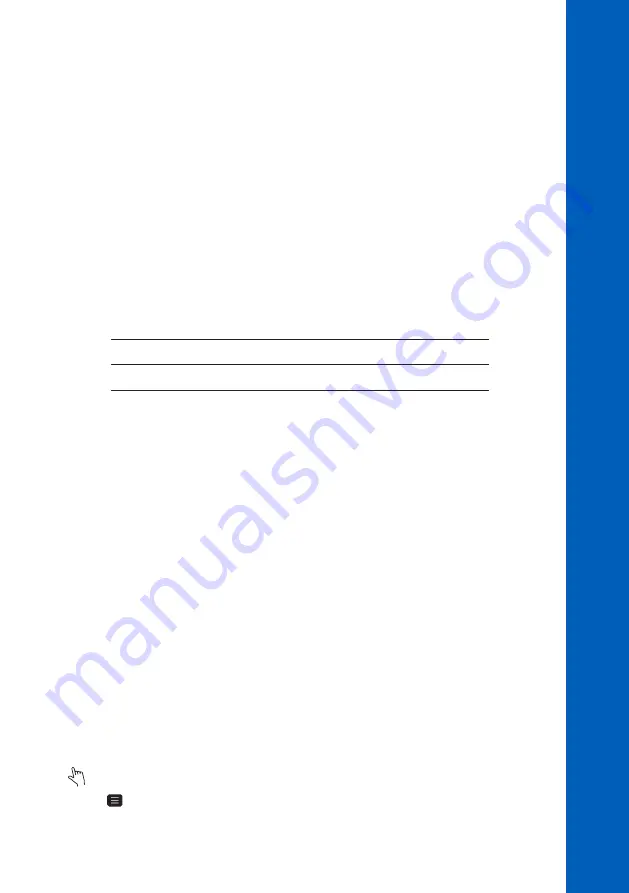
89
CONTROL MODES
14. CONTROL MODES
HI510
is intended to be used to control industrial processes. The instrument and sensor measure the
process variable and the
HI510
uses control settings to control outputs that are connected to auxiliary
equipment to control the process variable to the desired value.
The
HI510
uses smart probes to measure the process variable. In the case of a pH probe, the probe
also measures temperature. The smart probe stores the probe type, calibration data, Model, Firmware
version, Serial number and Factory calibration date in the probe. In the case of a pH probe, it converts
the high impedance mV value to a digital signal for clean measurement transport to the controller.
There are three types of algorithm corrections that can be applied to the control function: On/Off, Time
proportional and Proportional Integral & Derivative (PID).
The
HI510
uses outputs to interact with pumps, valves, and other equipment to control a process. It
contains Relays and Analog Outputs for this purpose.
Control Output Element
Output
Relays
On or Off
Analog Outputs (AO)
0-20 or 4-20 mA
The On relay state occurs when the relay is energized (NO and COM connected, NC and COM
disconnected).
The Off relay state occurs when the relay is de-energized (NO and COM disconnected, NC and COM
connected).
The Analog outputs can be adjusted to a minimum value of 0mA (default) or 4mA and a maximum
value of 20mA. See SECTION 11.3.2 Analog Outputs.
14.1. CONTROL ALGORITHMS
This section describes the controller behavior with a pH smart input. It presents a similar behavior with
other smart probe types.
There are three control algorithms implemented in
HI510
, and each algorithm has both specific and
common settings. The common settings – overtime & minimum On time – affect control output after
the specific algorithm settings and rules are evaluated.
The
overtime
(safety timer) sets the maximum continuous time that the control element is running
at it’s maximum value. If this time is exceeded, the control will be stopped and an alarm generated.
The
minimum on time
timer sets a time value to control the speed of the relay status change. This
timer prevents the relay and connected device from “chattering” by forcing a minimum on and off
time
.
This is necessary to protect elements that are driven (e.g. actuators, motors, contactors) from
electrical and mechanical shocks.
Navigation:
• Press from the Measure mode.