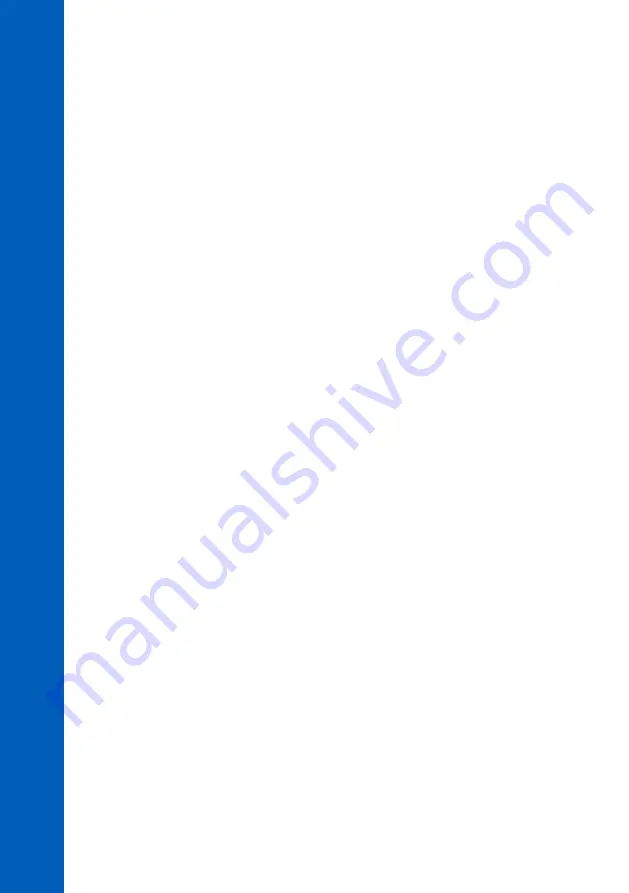
100
CONTROL MODES
14.1.3. Proportional Integral Derivative (PID) Control Algorithm
PID control on the
HI510
is a mathematical control loop method that automatically applies algorithm
corrections to the control function.
Proportional, Integral and Derivative control actions are brought together to create a single PID
control algorithm. PID systems use feedback (through integration) and prediction (through differentiation)
algorithms.There are various tuning parameters that must be set by the user. These enable a prediction
based on the speed of the process response to the output. With a well-tuned system, overshoot, offset
and oscillations are eliminated.
PID can be used for closed loop (such as batch tank) and open loop (such as chemical injection into
a pipe) systems.
Inputs
• Set point as the desired value of the controlled parameter
• Control mode as High or Low
• Deviation as a relative parameter
• Control period as time
• Reset time for integrative component as time
• Rate time for derivative component as time
• Dead Band as a relative parameter
• Dead Band Gain as 0 to 100%
Where:
Deviation
is the interval aligned with the Set point where control output proportional term can take
values from 0 to 100%. 0% indicates no action and 100% indicates full control output action. If
control output is assigned to a relay, 0% control output will keep relay Off during control time, while
100% will drive relay On for this entire time. A low value for this parameter is suitable for low latency
processes, allowing the control system to react quickly and strongly.
Control Period
is the time interval required for updating PID control output. High-dynamic processes
require frequent PID calculations updates, meaning shorter Control periods.
Reset time
indicates the history of the process control efficiency - sum of errors between Set point and
measured process value. A low value for this parameter, will increase the representation of previous
errors in the control output. This option is appropriate if deviation parameter is large or/and process
has a high latency.
Rate time
is a predictive parameter that indicates the speed of evolution of the control errors. It is
based on current and previous errors. A large value will increase control response to fast disturbances,
but will also make control more vulnerable to noise. Slow processes require rate time to be close to 0.
Dead Band
represents an area where the error between Set point and process value is considered 0.
The integrative term does not change in this area.
Dead Band Gain
is a coefficient applied to PID integrative term in the Dead Band area. 0% indicates
that the integrative term is nullified and 100% indicates that the term is part of the control output.