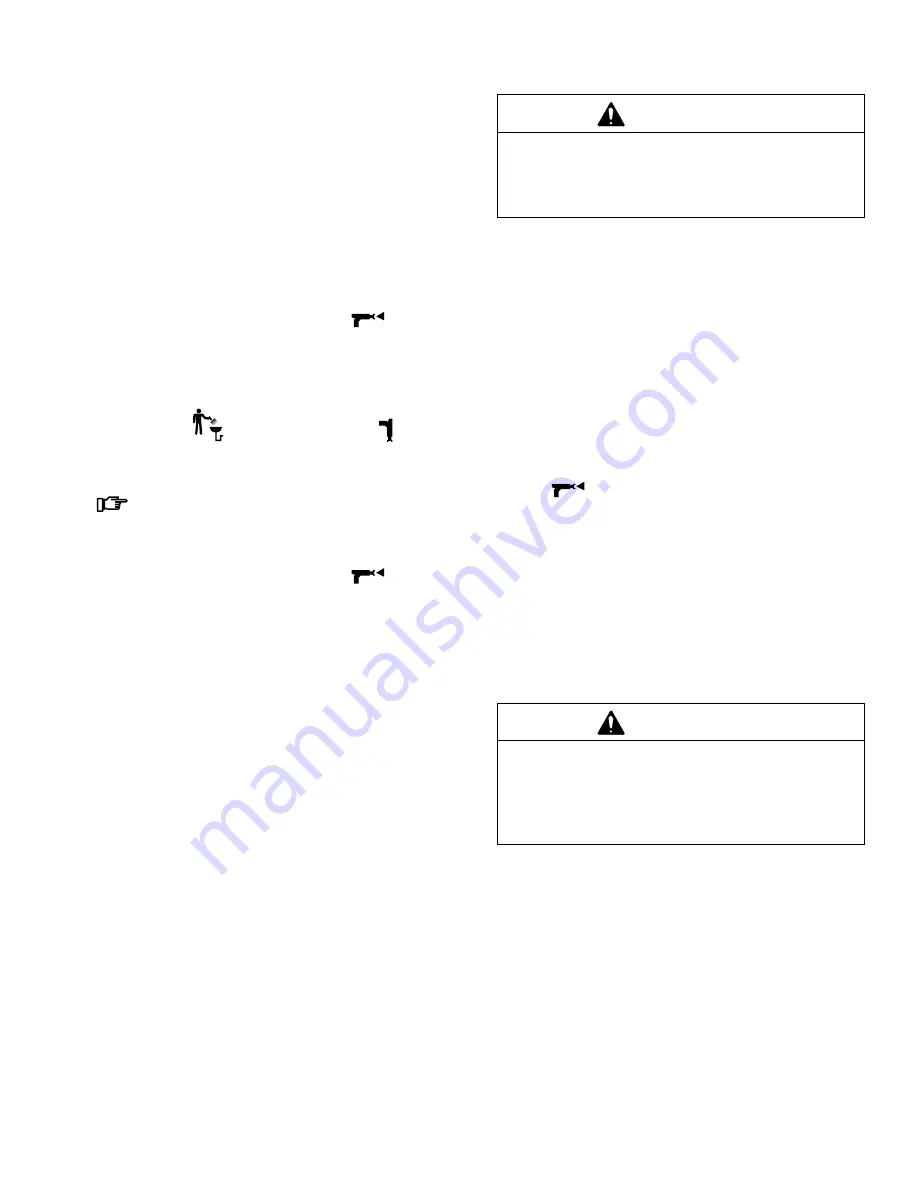
Operation
4–13
Operation
Starting Production
– continued
8.
Remove any air from the fluid lines of the system:
a.
Shut off the air to the gun by closing the air
regulator or shut-off valve for the gun atomiz-
ing air.
b.
Hold a metal part of the spray gun firmly to the
side of a grounded metal pail and trigger the
gun.
c.
Set the operator switch to Mix
.
d.
If the flow meters overrun because of air in the
system, and alarm will occur and operation will
stop. Move the operator switch momentarily to
Purge
, then back to Standby
to clear
the alarm and continue operation.
When clearing alarms, do not leave the opera-
tor switch in the Purge position for more than 2
seconds or the system will purge.
e.
Set the operator switch to Mix
to spray.
9.
Adjust the flow rate.
If a flow control system is installed,
see page 8–16
for flow control setup instructions and page 4–15
for flow control operation.
For a system without flow control:
a.
If the fluid output is too low, increase the
regulated fluid pressure. If the fluid output is
too high, adjust the fluid pressure regulator.
For fine adjustment, close the dispense valves
further.
CAUTION
Do not use the first 4 to 5 oz. (120 to 150 ml) of
material from the system, as it may not be thorough-
ly mixed due to alarms while loading material into the
system.
b.
Check the air pressure regulators on the fluid
supply tanks. The fluid flow rate at the spray
gun should be the same regardless of whether
the Component A, B, or C dispense valves are
open. The pressure adjustments of each
component will vary with each components
viscosity.
c.
Check or reset the air regulator in the atomiz-
ing air line.
10. Operation of the PrecisionMix II 3K is controlled by
the operation of the spray gun. When the gun is
triggered and the Operator Station switch is set to
Mix
, the dispense valves cycle and allow
Components A, B, and C to enter the mix manifold
and be mixed and dispensed to the gun.
NOTES:
If required, switch on the supply tank agitators
briefly whenever the fluid needs stirring. Over-agi-
tating can cause air entrainment.
Periodically check the fluid level in the fluid supply
tanks.
CAUTION
Never allow the fluid supply tanks to empty com-
pletely while the PrecisionMix II 3K is operating. Fill
them periodically, as needed. Failure to fill the tanks
when they are low may cause the metering ratios to
be incorrect without an alarm occurring.
Summary of Contents for PrecisionMix ii
Page 6: ...6 ...
Page 7: ...1 1 Warnings Warnings 1 ...
Page 8: ...1 2 Warnings ...
Page 11: ...Overview 2 1 Overview 2 ...
Page 12: ...2 2 Overview ...
Page 15: ...Overview 2 5 ...
Page 31: ...Installation 3 1 Installation 3 ...
Page 32: ...Installation 3 2 ...
Page 58: ...Installation 3 28 Notes ...
Page 67: ...Operation 4 1 Operation 4 ...
Page 68: ...Operation 4 2 ...
Page 83: ...Operation 4 17 Notes ...
Page 90: ...Operation 4 24 ...
Page 91: ...Screen Map 5 1 Screen Map 5 ...
Page 92: ...5 2 Screen Map ...
Page 94: ...5 4 Screen Map ...
Page 95: ...Run Monitor 6 1 Run Monitor 6 ...
Page 96: ...Run Monitor 6 2 ...
Page 103: ...Totalizers 7 1 Totalizers 7 ...
Page 104: ...Totalizers 7 2 ...
Page 108: ...Totalizers 7 6 ...
Page 109: ...System Configuration 8 1 System Configuration 8 ...
Page 110: ...System Configuration 8 2 ...
Page 142: ...System Configuration 8 34 ...
Page 143: ...Recipe Setup 9 1 Recipe Setup 9 ...
Page 144: ...Recipe Setup 9 2 ...
Page 165: ...10 1 Troubleshooting Troubleshooting 10 ...
Page 166: ...10 2 Troubleshooting ...
Page 182: ...10 18 Troubleshooting ...
Page 183: ...11 1 Service Service 11 ...
Page 184: ...11 2 Service ...
Page 192: ...11 10 Service ...
Page 193: ...12 1 Parts Parts 12 ...
Page 194: ...12 2 Parts ...
Page 207: ...12 15 Parts Notes ...
Page 228: ...12 36 Parts ...
Page 229: ...13 1 Utilities Software Utilities Software 13 ...
Page 230: ...13 2 Utilities Software ...
Page 254: ...13 26 Utilities Software ...
Page 255: ...14 1 Technical Data Technical Data 14 ...
Page 256: ...14 2 Technical Data ...
Page 259: ...14 5 Technical Data Notes ...