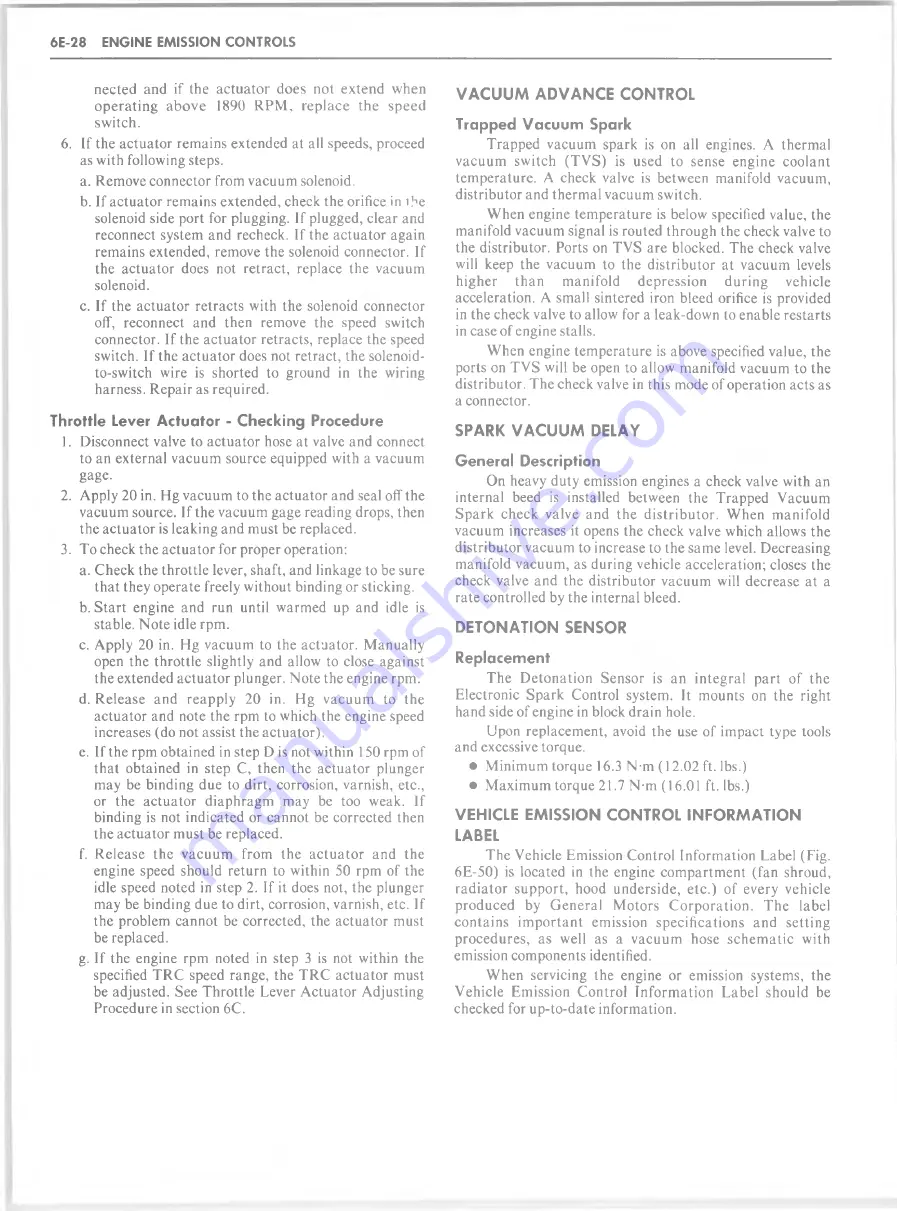
6 E -2 8
ENGINE EMISSION CONTROLS
n ected and if the a c tu a to r does n o t e x ten d w hen
o p e ra tin g a b o v e 1890 R P M , re p la c e th e sp eed
sw itch.
6. If the a c tu a to r rem ains extended at all speeds, proceed
as with following steps.
a. Remove connector from vacuum solenoid.
b. If actu a to r rem ains extended, check the orifice in tbe
solenoid side port for plugging. If plugged, clear and
reconnect system and recheck. If the a c tu ato r again
rem ains extended, remove the solenoid connector. If
the a c tu ato r does not re trac t, replace the vacuum
solenoid.
c. If the actu a to r re tracts with the solenoid connector
off, reconnect and then remove the speed switch
connector. If the actu a to r retracts, replace the speed
switch. If the actu a to r does not retract, the solenoid-
to-sw itch wire is shorted to ground in the wiring
harness. R ep air as required.
Throttle Lever A ctu ato r - Checking Procedure
1. Disconnect valve to a c tu a to r hose a t valve and connect
to an external vacuum source equipped with a vacuum
gage.
2. Apply 20 in. Hg vacuum to the ac tu ato r and seal off the
vacuum source. If the vacuum gage reading drops, then
the a c tu ato r is leaking and m ust be replaced.
3. To check the a c tu a to r for proper operation:
a. C heck the th ro ttle lever, shaft, and linkage to be sure
th a t they operate freely w ithout binding or sticking.
b. S ta rt engine and run until w arm ed up and idle is
stable. N ote idle rpm .
c. Apply 20 in. Hg vacuum to the actu ato r. M anually
open the th ro ttle slightly and allow to close against
the extended a c tu a to r plunger. N ote the engine rpm .
d. R elease and re ap p ly 20 in. H g v acuum to the
a c tu ato r and note the rpm to which the engine speed
increases (do not assist the actu ato r).
e. If the rpm obtained in step D is not w ithin 150 rpm of
th a t obtained in step C, then the a c tu ato r plunger
m ay be binding due to d irt, corrosion, varnish, etc.,
or the ac tu a to r d iaphragm m ay be too weak. If
binding is not indicated or cannot be corrected then
the a c tu ato r m ust be replaced.
f. R elease th e v ac u u m from the a c tu a to r and the
engine speed should retu rn to within 50 rpm of the
idle speed noted in step 2. If it does not, the plunger
m ay be binding due to d irt, corrosion, varnish, etc. If
the problem cannot be corrected, the actu ato r m ust
be replaced.
g. If the engine rpm noted in step 3 is not w ithin the
specified T R C speed range, the T R C ac tu ato r m ust
be adjusted. See T h ro ttle Lever A ctu ato r A djusting
Procedure in section 6C.
V A C U U M A D V A N C E C O N TRO L
Trapped V a cu u m Spark
T rapped vacuum spark is on all engines. A therm al
vacuum sw itch (T V S ) is used to sense engine co olant
tem perature. A check valve is betw een manifold vacuum ,
d istrib u to r and therm al vacuum switch.
W hen engine tem p eratu re is below specified value, the
m anifold vacuum signal is routed through the check valve to
the distributor. Ports on TV S are blocked. The check valve
will keep the vacuum to the d istrib u to r at vacuum levels
h ig h er
th a n
m anifold
d epression
d u rin g
vehicle
acceleration. A sm all sintered iron bleed orifice is provided
in the check valve to allow for a leak-dow n to enable restarts
in case of engine stalls.
W hen engine tem p eratu re is above specified value, the
ports on TV S will be open to allow m anifold vacuum to the
distributor. T he check valve in this mode of operation acts as
a connector.
SPARK V A C U U M DELAY
G e n e ral Description
On heavy duty emission engines a check valve w ith an
internal beed is installed betw een the T rapped V acuum
S p a rk check valve and th e d is trib u to r. W hen m anifold
vacuum increases it opens the check valve which allows the
distributor vacuum to increase to the sam e level. D ecreasing
m anifold vacuum , as during vehicle acceleration; closes the
check valve and the d istributor vacuum will decrease at a
ra te controlled by the internal bleed.
D E T O N A T IO N SENSOR
R eplacem ent
T he D eto n atio n S ensor is an in te g ra l p a rt of the
E lectronic S p ark Control system . It m ounts on the right
hand side of engine in block drain hole.
Upon replacem ent, avoid the use of im pact type tools
and excessive torque.
• M inim um torque 16.3 N -m (12.02 ft. lbs.)
• M a x im u m to rq u e 2 1 .7 N-m (16.01 ft. lbs.)
VEHICLE E M IS S IO N C O N TRO L IN F O R M A T IO N
LABEL
T he Vehicle Emission C ontrol Inform ation Label (Fig.
6E-50) is located in the engine co m p artm en t (fan shroud,
ra d ia to r su p p o rt, hood u n d ersid e, etc .) of every vehicle
produced by G en eral M otors C o rp o ra tio n . T h e label
co n tain s im p o rta n t em ission specifications and settin g
p ro ced u res, as well as a v a cu u m hose sc h e m a tic w ith
emission com ponents identified.
W hen servicing the engine or emission system s, the
V ehicle Em ission C ontrol In fo rm a tio n L abel should be
checked for up-to-date inform ation.
Summary of Contents for 1982 Light Duty Truck
Page 1: ......
Page 28: ...HEATER 1A 3 Fig lA 2 Heater Control C K Models Fig lA 3 Heater Control G Models...
Page 37: ...Fig 1A 11 T E E V A L V E A S M TEE AND VALVE C36...
Page 38: ...HEATER 1A 13 Fig 1A l2 Distributor Ducts G Models Fig 1A l5 Control Assembly G Models...
Page 39: ...1A 14 HEATER V IE W A V IE W B Fig 1A l7 Control Cable Routing G Models...
Page 42: ...HEATER 1A 19 Fig 1A 23 Auxiliary Heater Hose Routing...
Page 56: ...AIR CONDITIONING IB 13 Chart 1B 4 Pressure Cycling CCOT System Diagnosis...
Page 64: ...Fig 1B 17 C60 System Vacuum Diagram C K Series...
Page 65: ......
Page 66: ...Fig 1B 19 C60 Motor Home Chassis Wiring Diagram SWITCH AIR CONDITIONING IB 2 3...
Page 67: ...IB 24 AIR CONDITIONING Fig IB 20 1 P A C Harness Wiring...
Page 68: ...AIR CONDITIONING IB 25 VIE W A Fig IB 21 A C Compressor wiring...
Page 76: ...AIR CONDITIONING IB 33 Fig 1B 26 Compressor Mounting...
Page 91: ...IB 48 AIR CONDITIONING Fig 1B 59 C K Models Refrigerant Lines L6...
Page 150: ......
Page 162: ......
Page 164: ...2D 2 BODY Fig 2D 4 Typical Utility Vehicle Model...
Page 182: ...2D 20 BODY Fig 2D 51 Rear Door Controls Fig 2D 52 Rear Door Outside Handle and Lock Cylinder...
Page 193: ...BODY 2D 31 BELTS 3RD SEAT Fig 2D 82 Seat Belt Installation Suburban Driver Seat Suburban...
Page 194: ...2D 32 BODY Fig 2D 85 Passenger s Bucket Seat Chassis Cab...
Page 195: ...BODY 2D 33 Fig 2D 88 Rear Bench Seats Suburban...
Page 196: ...2D 34 BODY Fig 2D 89 CK Utility Seat Attachments...
Page 197: ...BODY 2D 35 Fig 2D 90 Seat Separator Compartment and Door CK Models...
Page 222: ......
Page 223: ...BODY 2D 61 Fig 2D 139 Front Seat Belt Installation...
Page 228: ......
Page 234: ......
Page 252: ...3B2 8 MANUAL STEERING GEAR Fig 3B2 11 Manual Steering Gear Exploded View...
Page 256: ......
Page 273: ...POWER STEERING SYSTEM 3B3 17 with LE3 Engine Exc HC4 LE4 LG9 LF4 LS9 LT9 and JB7 HC4 and JB8...
Page 342: ......
Page 389: ...REAR SUSPENSION 3D 7 Fig 3D 17 Rear Spring Installation C K Models...
Page 428: ...4 B 1 4 REAR AXLE Fig 4B 8 Gear Tooth Nomenclature Fig 4B 9 G ear Tooth Contact Pattern Check...
Page 444: ......
Page 454: ......
Page 468: ...4 B 5 2 REAR AXLE Fig 4B5 2 Rockwell Assembly...
Page 480: ...4 B 5 1 4 REAR AXLE...
Page 482: ...i...
Page 502: ......
Page 520: ......
Page 533: ...Fig 5 5 Front Brake Pipes and Hoses C K Models BRAKES 5 13...
Page 534: ...Fig 5 6 Front Brake Pipes and Hoses G M odels 5 14 B R A K E S...
Page 535: ...Fig 5 7 Front Brake Pipes and Hoses P Models BRAKES 5 15...
Page 536: ...5 16 BRAKES Fig 5 8 Rear Brake Hoses...
Page 538: ...5 18 BRAKES Fig 5 10 Parking Brake System Typical...
Page 539: ...BRAKES 5 19...
Page 570: ...5 50 BRAKES Fig 5 57 Power Steering Hose Routing C K Models...
Page 571: ...BRAKES 5 51 Fig 5 58 Power Steering Hose Routing G Models...
Page 572: ...Fig 5 59 Power Steering H ose Routing P Models 5 52 BRAKES...
Page 577: ...BRAKES 5 57 4 CONT A SECONDARY DIAPHRAGM B SECONDARY POWER 4 CONT C PRIMARY D Fig 5 5A Service...
Page 604: ......
Page 625: ...NOTES ENGINE 6 21...
Page 626: ......
Page 629: ...IN LINE 6 6A1 3 OIL PRESSURE SENDING UNIT Fig 6A1 1 In Line Engine Lubrication...
Page 630: ...6A1 4 IN LINE 6 Fig 6 A l 2 P Series Engine Front Mount...
Page 631: ...IN LINE 6 6A1 5 Fig 6Al 3 P Series Engine Rear Mount Fig 6 A l 4 C Series Engine Rear Mounts...
Page 634: ...6A1 8 IN LINE 6 Fig 6Al 7 K Series Engine Rear Mount...
Page 660: ......
Page 663: ...SMALL BLOCK 6A4 3 Fig 6A4 T Engine Lubrication...
Page 664: ...6A4 4 SMALL BLOCK Fig 6A4 2 Engine Lubrication...
Page 665: ...Fig 6A4 3 P Series Engine Mount Bracket...
Page 667: ...SMALL BLOCK 6A4 7 Fig 6A 4 5 P Series Engine Front Mount...
Page 668: ...6A4 8 SMALL BLOCK...
Page 669: ...SMALL BLOCK 6A4 9 Fig 6A 4 7 K Series Engine Mounts...
Page 670: ...6A4 10 SMALL BLOCK Fig 6A 4 8 C Series Engine Mounts...
Page 703: ...MARK IV 6A5 7 Fig 6A 5 6 P Series Engine Front Mount...
Page 704: ...6A5 8 MARK IV Fig 6 A 5 7 C Series Engine Mounts...
Page 731: ...6 2 DIESEL 6A7 3...
Page 760: ...6B 6 ENGINE COOLING Fig 6B 7 A C and A I R Adjustment...
Page 771: ...ENGINE COOLING 6B 17 Fig 6B 20 Engine O il C o o le r 6 2L Diesel...
Page 784: ......
Page 807: ...CARBURETOR MODEL 2SE 6C2 9 Fig 6C2 6 Typical 2SE Carburetor Assembly...
Page 820: ......
Page 830: ...6C4 10 CARBURETOR MODEL M4ME M4MC 101368 Fig 6C4 12 M 4M C M 4M E Carburetor Exploded View...
Page 848: ......
Page 876: ......
Page 888: ...6D 12 ENGINE ELECTRICAL Fig 6D 6C Generator Mounting Fig 6D 7C Generator Mounting...
Page 919: ...ENGINE ELECTRICAL 6D 43...
Page 934: ...Fig 6D 8E Starter M otor Mounting...
Page 974: ......
Page 1011: ...Figure 350C 25A Neutral Engine Running AUTOMATIC TRANSMISSION 350C 11...
Page 1054: ...Fig 7A 1C 400 Autom atic Transmission Side Cross Section Typical...
Page 1152: ...700 R4 40 AUTOMATIC TRANSMISSION Figure 700 R4 76 Transmission Assembly Exploded View...
Page 1162: ......
Page 1189: ...89MM MANUAL TRANSMISSION 7B3 5 Fig 7 3 4 4 Speed 89mm Exploded View...
Page 1219: ...CLUTCH 7C 5 Fig 7C 6 C K Truck Clutch Controls...
Page 1220: ...Fig 7C 7 G Truck Clutch Controls...
Page 1221: ...CLUTCH 7C 7 Fig 7C 8 P Truck Clutch Controls...
Page 1234: ...7E 2 TRANSFER CASE Fig 7E 1 Model 208 Transfer Case Cross Section...
Page 1252: ...7E 20 TRANSFER CASE Fig 7E 39 Transfer Case Attachment Typical...
Page 1278: ...8A 16 ELECTRICAL BODY AND CHASSIS Fig 8A 11 License Plate Lamps C K Series...
Page 1280: ...8A 18 ELECTRICAL BODY AND CHASSIS VIEW A VIEW B Fig 8A 15 CK Series Rear Lamp W iring...
Page 1281: ...ELECTRICAL BODY AND CHASSIS 8A 19 Fig 8A 16 CK Series Auxiliary W iring...
Page 1290: ...8B 8 ELECTRICAL AND WIRING Fig 8B 13 Seat Belt Reminder System Schematic...
Page 1292: ......
Page 1346: ...8C 54 INSTRUMENT PANEL AND GAGES Fig 8C 46 CK Series W iring 3 of 29...
Page 1351: ...INSTRUMENT PANEL AND GAGES 8C 59 SUBURBAN Fig 8C 51 CK Series W iring 8 of 29...
Page 1364: ...8C 72 INSTRUMENT PANEL AND GAGES Fig 8C 64 CK Series W iring 21 of 29...
Page 1365: ...INSTRUMENT PANEL AND GAGES 8C 73 CAB CRFW CAB CHASSIS Fig 8C 65 CK Series W iring 22 of 29...
Page 1366: ...8C 74 INSTRUMENT PANEL AND GAGES Fig 8C 66 CK Series W iring 23 of 29...
Page 1374: ...8C 82 INSTRUMENT PANEL AND GAGES Fig 8C 74 G Series W iring 2 of 19...
Page 1375: ...INSTRUMENT PANEL AND GAGES 8C 83 Fig 8C 75 G Series W iring 3 of 19...
Page 1376: ...8C 84 INSTRUMENT PANEL AND GAGES Fig 8C 76 G Series W iring 4 of 19...
Page 1379: ...INSTRUMENT PANEL AND GAGES 8C 87 Fig 8C 79 G Series W iring 7 of 19...
Page 1383: ...INSTRUMENT PANEL AND GAGES 8C 91 Fig 8C 83 G Series W iring 11 o f 19...
Page 1384: ...8C 92 INSTRUMENT PANEL AND GAGES BUS BARGWO Fig 8C 84 G Series W iring 12 of 19...
Page 1390: ...8C 98 INSTRUMENT PANEL AND GAGES Fig 8C 90 G Series W iring 18 of 19...
Page 1391: ...INSTRUMENT PANEL AND GAGES 8C 99 Fig 8C 91 G Series W iring 19 of 19...
Page 1392: ...8C 100 INSTRUMENT PANEL AND GAGES Fig 8C 92 P Series W iring 1 of 11...
Page 1393: ...INSTRUMENT PANEL AND GAGES 8C 101 Fig 8C 93 P Series W iring 2 of 11...
Page 1396: ...8C 104 INSTRUMENT PANEL AND GAGES Fig 8C 96 P Series W iring 5 of 11...
Page 1399: ...INSTRUMENT PANEL AND GAGES 8C 107 Fig 8C 99 P Series W iring 8 of 11...
Page 1401: ...INSTRUMENT PANEL AND GAGES 8C 109 START RUN OF LOCK ACC Fig 8C 101 P Series W iring 10 of 11...
Page 1415: ...ACCESSORIES 9 13 RADIO NOISE BLOWER MOTOR Fig 9 6R Radio Diagnosis Chart B...
Page 1416: ...9 14 ACCESSORIES D E A D R A D IO A M R A D IO I Fig 9 7R Radio Diagnosis Chart C...
Page 1417: ...ACCESSORIES 9 15 DEAD RADIO AM FM RADIO Fig 9 8R Radio Diagnosis Chart D...
Page 1435: ...t f l i t 1...