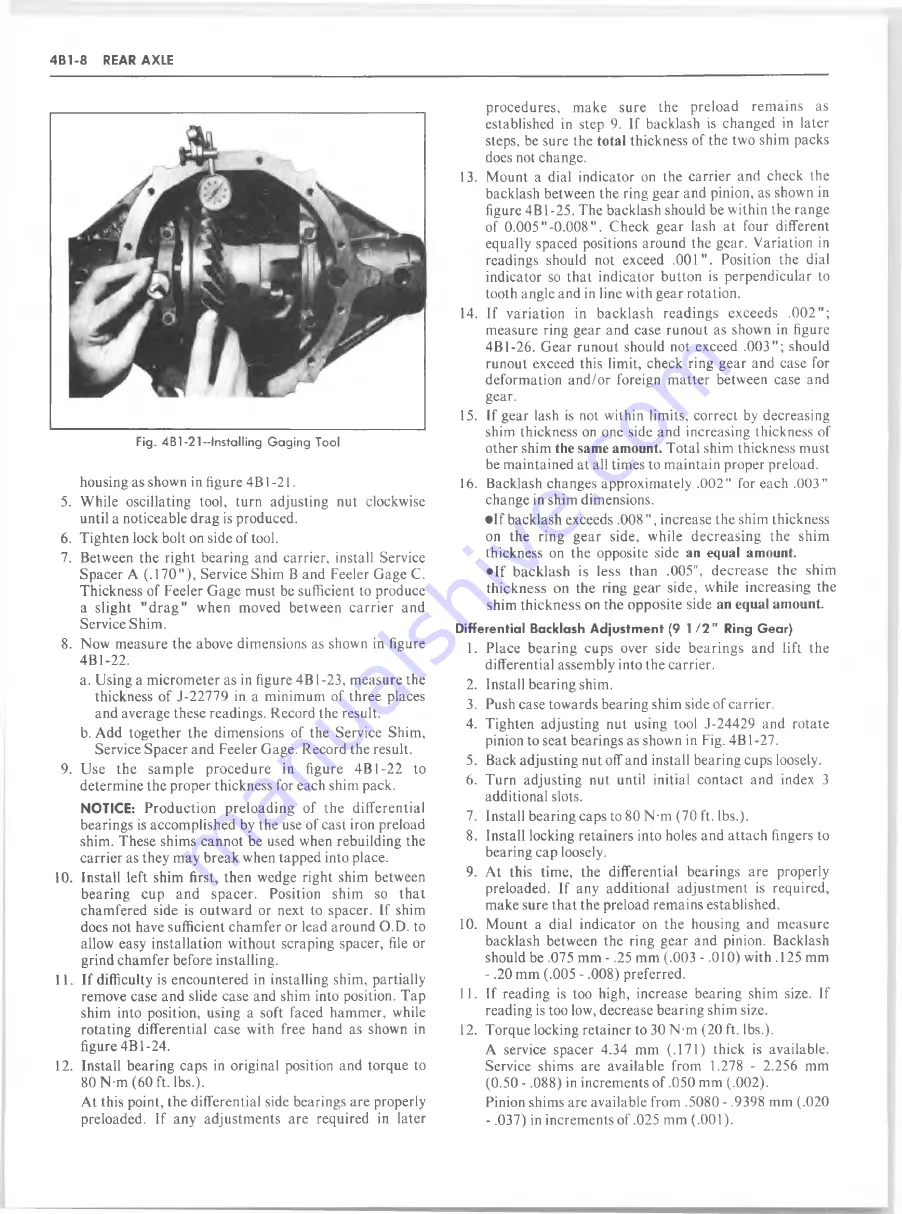
4 B 1 - 8
R EA R A X L E
Fig. 4B1 -21 -Installing Gaging Tool
housing as shown in figure 4 B 1 -21.
5. While oscillating tool, turn adjusting nut clockwise
until a noticeable drag is produced.
6. Tighten lock bolt on side of tool.
7. Between the right bearing and carrier, install Service
Spacer A (.1 7 0 " ), Service Shim B and Feeler Gage C.
Thickness of Feeler G age must be sufficient to produce
a slight " d r a g " when moved betw een c a rrie r and
Service Shim.
8. Now measure the above dimensions as shown in figure
4B1-22.
a. Using a micrometer as in figure 4B1-23, measure the
thickness of J-22779 in a minim um of three places
and average these readings. Record the result.
b. Add together the dimensions of the Service Shim,
Service Spacer and Feeler Gage. Record the result.
9. Use th e sam ple pro ced u re in figure 4B1-22 to
determine the proper thickness for each shim pack.
NOTICE:
Production preloading of th e differential
bearings is accomplished by the use of cast iron preload
shim. These shims cannot be used when rebuilding the
carrier as they may break when tapped into place.
10. Install left shim first, then wedge right shim between
bearing cup and spacer. Position shim so t h a t
chamfered side is outward or next to spacer. If shim
does not have sufficient cham fer or lead around O.D. to
allow easy installation without scraping spacer, file or
grind chamfer before installing.
11. If difficulty is encountered in installing shim, partially
remove case and slide case and shim into position. Tap
shim into position, using a soft faced ham m er, while
rotating differential case with free hand as shown in
figure 4B1-24.
12. Install bearing caps in original position and torque to
80 N-m (60 ft. lbs.).
At this point, the differential side bearings are properly
preloaded. If any adjustments are required in later
procedures, m ake sure the preload rem ains as
established in step 9. If backlash is changed in later
steps, be sure the
total
thickness of the two shim packs
does not change.
13. Mount a dial indicator on the carrier and check the
backlash between the ring gear and pinion, as shown in
figure 4B1-25. The backlash should be within the range
of 0.0 0 5 "-0 .0 0 8 " . Check gear lash at four different
equally spaced positions around the gear. Variation in
readings should not exceed .001". Position the dial
indicator so that indicator button is perpendicular to
tooth angle and in line with gear rotation.
14. If variation in backlash readings exceeds .0 0 2 " ;
measure ring gear and case runout as shown in figure
4B1-26. Gear runout should not exceed .0 03"; should
runout exceed this limit, check ring gear and case for
deformation a n d /o r foreign m atter between case and
gear.
15. If gear lash is not within limits, correct by decreasing
shim thickness on one side and increasing thickness of
other shim
the same amount.
Total shim thickness must
be maintained at all times to maintain proper preload.
16. Backlash changes approximately .002" for each .003"
change in shim dimensions.
• I f backlash exceeds .008 ", increase the shim thickness
on the ring gear side, while d ecreasing the shim
thickness on the opposite side
an equal amount.
• I f b acklash is less than .005", d e c re a se the shim
thickness on the ring gear side, while increasing the
shim th ickness on the opposite side
an equal amount.
D iffe re n tia l Backlash A d ju s tm e n t (9 1
I I "
Ring G ear)
1. Place bearing cups over side bearings and lift the
differential assembly into the carrier.
2. Install bearing shim.
3. Push case towards bearing shim side of carrier.
4. Tighten adjusting nut using tool J-24429 and rotate
pinion to seat bearings as shown in Fig. 4 B 1 -27.
5. Back adjusting nut off and install bearing cups loosely.
6. Turn adjusting nut until initial contact and index 3
additional slots.
7. Install bearing caps to 80 N-m (70 ft. lbs.).
8. Install locking retainers into holes and attach fingers to
bearing cap loosely.
9. At this time, the differential bearings are properly
preloaded. If any additional adjustm ent is required,
make sure th at the preload remains established.
10. M ount a dial indicator on the housing and measure
backlash between the ring gear and pinion. Backlash
should be .075 mm - .25 mm (.003 - .010) with .125 mm
- .20 mm (.005 - .008) preferred.
11. If reading is too high, increase bearing shim size. If
reading is too low, decrease bearing shim size.
12. Torque locking retainer to 30 N-m (20 ft. lbs.).
A service spacer 4.34 mm (.171) thick is available.
Service shims are available from 1.278 - 2.256 mm
(0.50 - .088) in increments of .050 mm (.002).
Pinion shims are available from .5080 - .9398 mm (.020
- .037) in increments of .025 mm (.001).
Summary of Contents for 1982 Light Duty Truck
Page 1: ......
Page 28: ...HEATER 1A 3 Fig lA 2 Heater Control C K Models Fig lA 3 Heater Control G Models...
Page 37: ...Fig 1A 11 T E E V A L V E A S M TEE AND VALVE C36...
Page 38: ...HEATER 1A 13 Fig 1A l2 Distributor Ducts G Models Fig 1A l5 Control Assembly G Models...
Page 39: ...1A 14 HEATER V IE W A V IE W B Fig 1A l7 Control Cable Routing G Models...
Page 42: ...HEATER 1A 19 Fig 1A 23 Auxiliary Heater Hose Routing...
Page 56: ...AIR CONDITIONING IB 13 Chart 1B 4 Pressure Cycling CCOT System Diagnosis...
Page 64: ...Fig 1B 17 C60 System Vacuum Diagram C K Series...
Page 65: ......
Page 66: ...Fig 1B 19 C60 Motor Home Chassis Wiring Diagram SWITCH AIR CONDITIONING IB 2 3...
Page 67: ...IB 24 AIR CONDITIONING Fig IB 20 1 P A C Harness Wiring...
Page 68: ...AIR CONDITIONING IB 25 VIE W A Fig IB 21 A C Compressor wiring...
Page 76: ...AIR CONDITIONING IB 33 Fig 1B 26 Compressor Mounting...
Page 91: ...IB 48 AIR CONDITIONING Fig 1B 59 C K Models Refrigerant Lines L6...
Page 150: ......
Page 162: ......
Page 164: ...2D 2 BODY Fig 2D 4 Typical Utility Vehicle Model...
Page 182: ...2D 20 BODY Fig 2D 51 Rear Door Controls Fig 2D 52 Rear Door Outside Handle and Lock Cylinder...
Page 193: ...BODY 2D 31 BELTS 3RD SEAT Fig 2D 82 Seat Belt Installation Suburban Driver Seat Suburban...
Page 194: ...2D 32 BODY Fig 2D 85 Passenger s Bucket Seat Chassis Cab...
Page 195: ...BODY 2D 33 Fig 2D 88 Rear Bench Seats Suburban...
Page 196: ...2D 34 BODY Fig 2D 89 CK Utility Seat Attachments...
Page 197: ...BODY 2D 35 Fig 2D 90 Seat Separator Compartment and Door CK Models...
Page 222: ......
Page 223: ...BODY 2D 61 Fig 2D 139 Front Seat Belt Installation...
Page 228: ......
Page 234: ......
Page 252: ...3B2 8 MANUAL STEERING GEAR Fig 3B2 11 Manual Steering Gear Exploded View...
Page 256: ......
Page 273: ...POWER STEERING SYSTEM 3B3 17 with LE3 Engine Exc HC4 LE4 LG9 LF4 LS9 LT9 and JB7 HC4 and JB8...
Page 342: ......
Page 389: ...REAR SUSPENSION 3D 7 Fig 3D 17 Rear Spring Installation C K Models...
Page 428: ...4 B 1 4 REAR AXLE Fig 4B 8 Gear Tooth Nomenclature Fig 4B 9 G ear Tooth Contact Pattern Check...
Page 444: ......
Page 454: ......
Page 468: ...4 B 5 2 REAR AXLE Fig 4B5 2 Rockwell Assembly...
Page 480: ...4 B 5 1 4 REAR AXLE...
Page 482: ...i...
Page 502: ......
Page 520: ......
Page 533: ...Fig 5 5 Front Brake Pipes and Hoses C K Models BRAKES 5 13...
Page 534: ...Fig 5 6 Front Brake Pipes and Hoses G M odels 5 14 B R A K E S...
Page 535: ...Fig 5 7 Front Brake Pipes and Hoses P Models BRAKES 5 15...
Page 536: ...5 16 BRAKES Fig 5 8 Rear Brake Hoses...
Page 538: ...5 18 BRAKES Fig 5 10 Parking Brake System Typical...
Page 539: ...BRAKES 5 19...
Page 570: ...5 50 BRAKES Fig 5 57 Power Steering Hose Routing C K Models...
Page 571: ...BRAKES 5 51 Fig 5 58 Power Steering Hose Routing G Models...
Page 572: ...Fig 5 59 Power Steering H ose Routing P Models 5 52 BRAKES...
Page 577: ...BRAKES 5 57 4 CONT A SECONDARY DIAPHRAGM B SECONDARY POWER 4 CONT C PRIMARY D Fig 5 5A Service...
Page 604: ......
Page 625: ...NOTES ENGINE 6 21...
Page 626: ......
Page 629: ...IN LINE 6 6A1 3 OIL PRESSURE SENDING UNIT Fig 6A1 1 In Line Engine Lubrication...
Page 630: ...6A1 4 IN LINE 6 Fig 6 A l 2 P Series Engine Front Mount...
Page 631: ...IN LINE 6 6A1 5 Fig 6Al 3 P Series Engine Rear Mount Fig 6 A l 4 C Series Engine Rear Mounts...
Page 634: ...6A1 8 IN LINE 6 Fig 6Al 7 K Series Engine Rear Mount...
Page 660: ......
Page 663: ...SMALL BLOCK 6A4 3 Fig 6A4 T Engine Lubrication...
Page 664: ...6A4 4 SMALL BLOCK Fig 6A4 2 Engine Lubrication...
Page 665: ...Fig 6A4 3 P Series Engine Mount Bracket...
Page 667: ...SMALL BLOCK 6A4 7 Fig 6A 4 5 P Series Engine Front Mount...
Page 668: ...6A4 8 SMALL BLOCK...
Page 669: ...SMALL BLOCK 6A4 9 Fig 6A 4 7 K Series Engine Mounts...
Page 670: ...6A4 10 SMALL BLOCK Fig 6A 4 8 C Series Engine Mounts...
Page 703: ...MARK IV 6A5 7 Fig 6A 5 6 P Series Engine Front Mount...
Page 704: ...6A5 8 MARK IV Fig 6 A 5 7 C Series Engine Mounts...
Page 731: ...6 2 DIESEL 6A7 3...
Page 760: ...6B 6 ENGINE COOLING Fig 6B 7 A C and A I R Adjustment...
Page 771: ...ENGINE COOLING 6B 17 Fig 6B 20 Engine O il C o o le r 6 2L Diesel...
Page 784: ......
Page 807: ...CARBURETOR MODEL 2SE 6C2 9 Fig 6C2 6 Typical 2SE Carburetor Assembly...
Page 820: ......
Page 830: ...6C4 10 CARBURETOR MODEL M4ME M4MC 101368 Fig 6C4 12 M 4M C M 4M E Carburetor Exploded View...
Page 848: ......
Page 876: ......
Page 888: ...6D 12 ENGINE ELECTRICAL Fig 6D 6C Generator Mounting Fig 6D 7C Generator Mounting...
Page 919: ...ENGINE ELECTRICAL 6D 43...
Page 934: ...Fig 6D 8E Starter M otor Mounting...
Page 974: ......
Page 1011: ...Figure 350C 25A Neutral Engine Running AUTOMATIC TRANSMISSION 350C 11...
Page 1054: ...Fig 7A 1C 400 Autom atic Transmission Side Cross Section Typical...
Page 1152: ...700 R4 40 AUTOMATIC TRANSMISSION Figure 700 R4 76 Transmission Assembly Exploded View...
Page 1162: ......
Page 1189: ...89MM MANUAL TRANSMISSION 7B3 5 Fig 7 3 4 4 Speed 89mm Exploded View...
Page 1219: ...CLUTCH 7C 5 Fig 7C 6 C K Truck Clutch Controls...
Page 1220: ...Fig 7C 7 G Truck Clutch Controls...
Page 1221: ...CLUTCH 7C 7 Fig 7C 8 P Truck Clutch Controls...
Page 1234: ...7E 2 TRANSFER CASE Fig 7E 1 Model 208 Transfer Case Cross Section...
Page 1252: ...7E 20 TRANSFER CASE Fig 7E 39 Transfer Case Attachment Typical...
Page 1278: ...8A 16 ELECTRICAL BODY AND CHASSIS Fig 8A 11 License Plate Lamps C K Series...
Page 1280: ...8A 18 ELECTRICAL BODY AND CHASSIS VIEW A VIEW B Fig 8A 15 CK Series Rear Lamp W iring...
Page 1281: ...ELECTRICAL BODY AND CHASSIS 8A 19 Fig 8A 16 CK Series Auxiliary W iring...
Page 1290: ...8B 8 ELECTRICAL AND WIRING Fig 8B 13 Seat Belt Reminder System Schematic...
Page 1292: ......
Page 1346: ...8C 54 INSTRUMENT PANEL AND GAGES Fig 8C 46 CK Series W iring 3 of 29...
Page 1351: ...INSTRUMENT PANEL AND GAGES 8C 59 SUBURBAN Fig 8C 51 CK Series W iring 8 of 29...
Page 1364: ...8C 72 INSTRUMENT PANEL AND GAGES Fig 8C 64 CK Series W iring 21 of 29...
Page 1365: ...INSTRUMENT PANEL AND GAGES 8C 73 CAB CRFW CAB CHASSIS Fig 8C 65 CK Series W iring 22 of 29...
Page 1366: ...8C 74 INSTRUMENT PANEL AND GAGES Fig 8C 66 CK Series W iring 23 of 29...
Page 1374: ...8C 82 INSTRUMENT PANEL AND GAGES Fig 8C 74 G Series W iring 2 of 19...
Page 1375: ...INSTRUMENT PANEL AND GAGES 8C 83 Fig 8C 75 G Series W iring 3 of 19...
Page 1376: ...8C 84 INSTRUMENT PANEL AND GAGES Fig 8C 76 G Series W iring 4 of 19...
Page 1379: ...INSTRUMENT PANEL AND GAGES 8C 87 Fig 8C 79 G Series W iring 7 of 19...
Page 1383: ...INSTRUMENT PANEL AND GAGES 8C 91 Fig 8C 83 G Series W iring 11 o f 19...
Page 1384: ...8C 92 INSTRUMENT PANEL AND GAGES BUS BARGWO Fig 8C 84 G Series W iring 12 of 19...
Page 1390: ...8C 98 INSTRUMENT PANEL AND GAGES Fig 8C 90 G Series W iring 18 of 19...
Page 1391: ...INSTRUMENT PANEL AND GAGES 8C 99 Fig 8C 91 G Series W iring 19 of 19...
Page 1392: ...8C 100 INSTRUMENT PANEL AND GAGES Fig 8C 92 P Series W iring 1 of 11...
Page 1393: ...INSTRUMENT PANEL AND GAGES 8C 101 Fig 8C 93 P Series W iring 2 of 11...
Page 1396: ...8C 104 INSTRUMENT PANEL AND GAGES Fig 8C 96 P Series W iring 5 of 11...
Page 1399: ...INSTRUMENT PANEL AND GAGES 8C 107 Fig 8C 99 P Series W iring 8 of 11...
Page 1401: ...INSTRUMENT PANEL AND GAGES 8C 109 START RUN OF LOCK ACC Fig 8C 101 P Series W iring 10 of 11...
Page 1415: ...ACCESSORIES 9 13 RADIO NOISE BLOWER MOTOR Fig 9 6R Radio Diagnosis Chart B...
Page 1416: ...9 14 ACCESSORIES D E A D R A D IO A M R A D IO I Fig 9 7R Radio Diagnosis Chart C...
Page 1417: ...ACCESSORIES 9 15 DEAD RADIO AM FM RADIO Fig 9 8R Radio Diagnosis Chart D...
Page 1435: ...t f l i t 1...