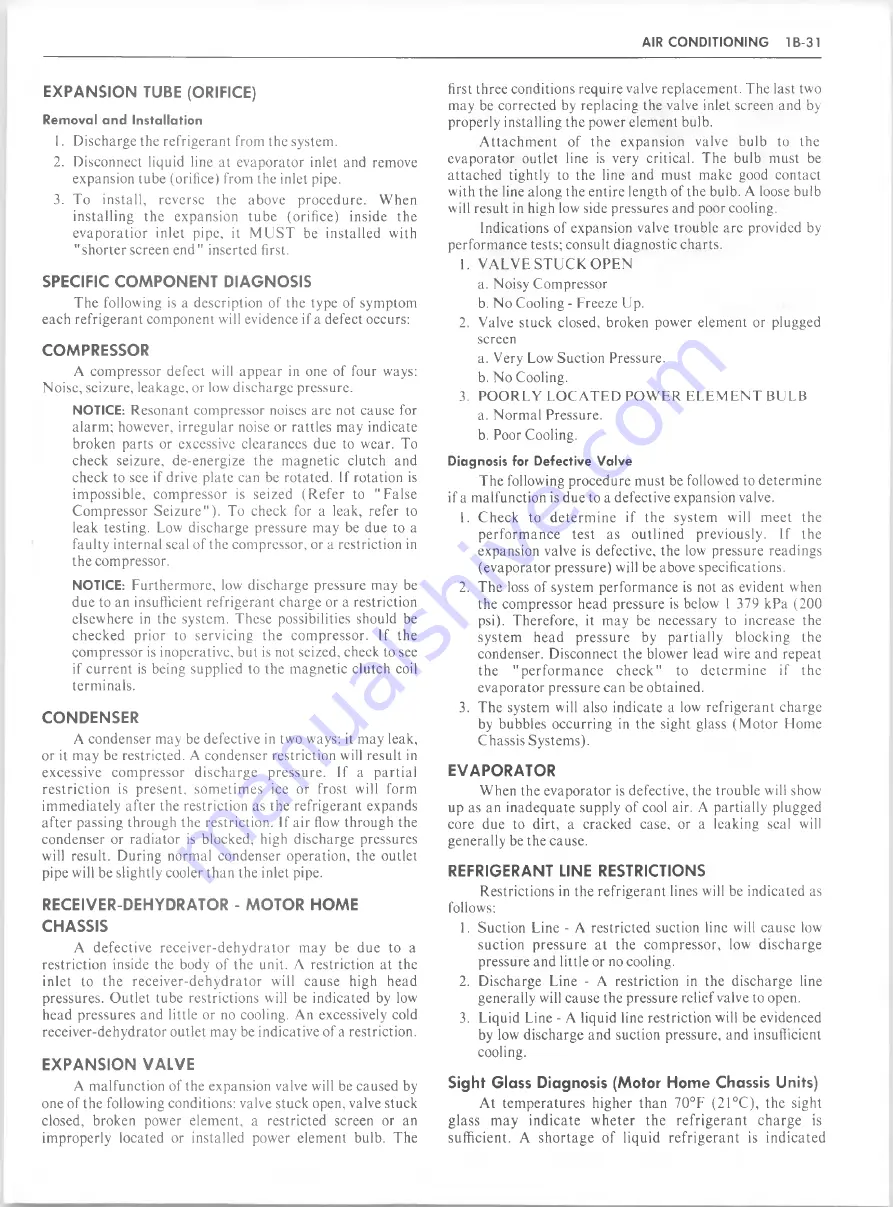
AIR CONDITIONING
IB-31
E X P A N S IO N TUBE (ORIFICE)
R em oval a n d Installatio n
1. D ischarge the refrigerant from the system.
2. Disconnect liquid line at evaporator inlet and remove
expansion tube (orifice) from the inlet pipe.
3. To in stall, reverse the above procedure. W hen
in stallin g th e expansion tu b e (orifice) inside the
ev a p o ra tio r inlet pipe, it M U S T be in stalled w ith
" shorter screen end " inserted first.
SPECIFIC C O M P O N E N T D IA G N O S IS
The following is a description of the type of sym ptom
each refrig eran t com ponent will evidence if a defect occurs:
COM PRESSOR
A com pressor defect will appear in one of four ways:
Noise, seizure, leakage, or low discharge pressure.
NOTICE:
R esonant com pressor noises are not cause for
alarm ; however, irregular noise or rattles may indicate
broken parts or excessive clearances due to wear. To
check seizure, de-energize the m agnetic clutch and
check to see if drive plate can be rotated. If rotation is
im possible, com pressor is seized (R e fe r to "F alse
C om pressor S e iz u re "). To check for a leak, refer to
leak testing. Low discharge pressure may be due to a
faulty internal seal of the com pressor, or a restriction in
the com pressor.
NOTICE:
F urtherm ore, low discharge pressure m ay be
due to an insufficient refrig eran t charge or a restriction
elsewhere in the system. These possibilities should be
checked prior to servicing the com pressor. If the
com pressor is inoperative, but is not seized, check to see
if cu rren t is being supplied to the m agnetic clutch coil
term inals.
CO N D EN SER
A condenser may be defective in two ways: it may leak,
or it m ay be restricted. A condenser restriction will result in
excessive com pressor d isch arg e pressure. If a p a rtia l
re stric tio n is present, som etim es ice or frost will form
im m ediately after the restriction as the refrigerant expands
afte r passing through the restriction. If air flow through the
condenser or radiator is blocked, high discharge pressures
will result. During norm al condenser operation, the outlet
pipe will be slightly cooler than the inlet pipe.
RECEIVER-DEHYDRATO R - M O T O R H O M E
CHASSIS
A defective re c e iv e r-d e h y d ra to r m ay be due to a
restriction inside the body of the unit. A restriction at the
inlet to the receiv e r-d e h y d ra to r will cause high head
pressures. O utlet tube restrictions will be indicated by low
head pressures and little or no cooling. An excessively cold
receiver-dehydrator outlet may be indicative of a restriction.
E X P A N S IO N V A LV E
A m alfunction of the expansion valve will be caused by
one of the following conditions: valve stuck open, valve stuck
closed, broken power elem ent, a restricted screen or an
im properly located or installed power elem ent bulb. The
first three conditions require valve replacem ent. The last two
may be corrected by replacing the valve inlet screen and by
properly installing the power elem ent bulb.
A tta c h m e n t of the expansion valve bulb to the
evaporator outlet line is very critical. The bulb m ust be
attached tightly to the line and m ust make good contact
with the line along the entire length of the bulb. A loose bulb
will result in high low side pressures and poor cooling.
Indications of expansion valve trouble are provided by
perform ance tests; consult diagnostic charts.
1. V A LV E S T U C K O PE N
a. Noisy Com pressor
b. N o Cooling - Freeze Up.
2. Valve stuck closed, broken power elem ent or plugged
screen
a. Very Low Suction Pressure.
b. N o Cooling.
3. P O O R L Y L O C A T E D P O W E R E L E M E N T BULB
a. N orm al Pressure.
b. Poor Cooling.
Diagnosis for Defective V a lv e
T he following procedure m ust be followed to determ ine
if a m alfunction is due to a defective expansion valve.
1. C heck to d e te rm in e if the system will m eet the
p erfo rm an ce test as outlined previously. If the
expansion valve is defective, the low pressure readings
(evaporator pressure) will be above specifications.
2. The loss of system perform ance is not as evident when
the com pressor head pressure is below 1 379 kPa (200
psi). Therefore, it may be necessary to increase the
system head p ressu re by p a rtially blocking the
condenser. Disconnect the blower lead wire and repeat
the "p e rfo rm a n c e c h eck " to d eterm in e if the
evaporator pressure can be obtained.
3. The system will also indicate a low refrigerant charge
by bubbles occurring in the sight glass (M otor Home
Chassis System s).
E V APO R A TO R
W hen the evaporator is defective, the trouble will show
up as an inadequate supply of cool air. A partially plugged
core due to dirt, a cracked case, or a leaking seal will
generally be the cause.
REFRIGERANT LINE RESTRICTIONS
R estrictions in the refrigerant lines will be indicated as
follows:
1. Suction Line - A restricted suction line will cause low
suction pressure a t the com pressor, low d isch arg e
pressure and little or no cooling.
2. D ischarge Line - A restriction in the discharge line
generally will cause the pressure relief valve to open.
3. Liquid Line - A liquid line restriction will be evidenced
by low discharge and suction pressure, and insufficient
cooling.
Sight Glass Diagnosis (M oto r H om e Chassis Units)
A t tem peratures higher th an 70°F (21°C ), the sight
glass m ay in d icate w h eter the re frig e ra n t ch arg e is
sufficient. A sh o rta g e of liquid re frig e ra n t is ind icated
Summary of Contents for 1982 Light Duty Truck
Page 1: ......
Page 28: ...HEATER 1A 3 Fig lA 2 Heater Control C K Models Fig lA 3 Heater Control G Models...
Page 37: ...Fig 1A 11 T E E V A L V E A S M TEE AND VALVE C36...
Page 38: ...HEATER 1A 13 Fig 1A l2 Distributor Ducts G Models Fig 1A l5 Control Assembly G Models...
Page 39: ...1A 14 HEATER V IE W A V IE W B Fig 1A l7 Control Cable Routing G Models...
Page 42: ...HEATER 1A 19 Fig 1A 23 Auxiliary Heater Hose Routing...
Page 56: ...AIR CONDITIONING IB 13 Chart 1B 4 Pressure Cycling CCOT System Diagnosis...
Page 64: ...Fig 1B 17 C60 System Vacuum Diagram C K Series...
Page 65: ......
Page 66: ...Fig 1B 19 C60 Motor Home Chassis Wiring Diagram SWITCH AIR CONDITIONING IB 2 3...
Page 67: ...IB 24 AIR CONDITIONING Fig IB 20 1 P A C Harness Wiring...
Page 68: ...AIR CONDITIONING IB 25 VIE W A Fig IB 21 A C Compressor wiring...
Page 76: ...AIR CONDITIONING IB 33 Fig 1B 26 Compressor Mounting...
Page 91: ...IB 48 AIR CONDITIONING Fig 1B 59 C K Models Refrigerant Lines L6...
Page 150: ......
Page 162: ......
Page 164: ...2D 2 BODY Fig 2D 4 Typical Utility Vehicle Model...
Page 182: ...2D 20 BODY Fig 2D 51 Rear Door Controls Fig 2D 52 Rear Door Outside Handle and Lock Cylinder...
Page 193: ...BODY 2D 31 BELTS 3RD SEAT Fig 2D 82 Seat Belt Installation Suburban Driver Seat Suburban...
Page 194: ...2D 32 BODY Fig 2D 85 Passenger s Bucket Seat Chassis Cab...
Page 195: ...BODY 2D 33 Fig 2D 88 Rear Bench Seats Suburban...
Page 196: ...2D 34 BODY Fig 2D 89 CK Utility Seat Attachments...
Page 197: ...BODY 2D 35 Fig 2D 90 Seat Separator Compartment and Door CK Models...
Page 222: ......
Page 223: ...BODY 2D 61 Fig 2D 139 Front Seat Belt Installation...
Page 228: ......
Page 234: ......
Page 252: ...3B2 8 MANUAL STEERING GEAR Fig 3B2 11 Manual Steering Gear Exploded View...
Page 256: ......
Page 273: ...POWER STEERING SYSTEM 3B3 17 with LE3 Engine Exc HC4 LE4 LG9 LF4 LS9 LT9 and JB7 HC4 and JB8...
Page 342: ......
Page 389: ...REAR SUSPENSION 3D 7 Fig 3D 17 Rear Spring Installation C K Models...
Page 428: ...4 B 1 4 REAR AXLE Fig 4B 8 Gear Tooth Nomenclature Fig 4B 9 G ear Tooth Contact Pattern Check...
Page 444: ......
Page 454: ......
Page 468: ...4 B 5 2 REAR AXLE Fig 4B5 2 Rockwell Assembly...
Page 480: ...4 B 5 1 4 REAR AXLE...
Page 482: ...i...
Page 502: ......
Page 520: ......
Page 533: ...Fig 5 5 Front Brake Pipes and Hoses C K Models BRAKES 5 13...
Page 534: ...Fig 5 6 Front Brake Pipes and Hoses G M odels 5 14 B R A K E S...
Page 535: ...Fig 5 7 Front Brake Pipes and Hoses P Models BRAKES 5 15...
Page 536: ...5 16 BRAKES Fig 5 8 Rear Brake Hoses...
Page 538: ...5 18 BRAKES Fig 5 10 Parking Brake System Typical...
Page 539: ...BRAKES 5 19...
Page 570: ...5 50 BRAKES Fig 5 57 Power Steering Hose Routing C K Models...
Page 571: ...BRAKES 5 51 Fig 5 58 Power Steering Hose Routing G Models...
Page 572: ...Fig 5 59 Power Steering H ose Routing P Models 5 52 BRAKES...
Page 577: ...BRAKES 5 57 4 CONT A SECONDARY DIAPHRAGM B SECONDARY POWER 4 CONT C PRIMARY D Fig 5 5A Service...
Page 604: ......
Page 625: ...NOTES ENGINE 6 21...
Page 626: ......
Page 629: ...IN LINE 6 6A1 3 OIL PRESSURE SENDING UNIT Fig 6A1 1 In Line Engine Lubrication...
Page 630: ...6A1 4 IN LINE 6 Fig 6 A l 2 P Series Engine Front Mount...
Page 631: ...IN LINE 6 6A1 5 Fig 6Al 3 P Series Engine Rear Mount Fig 6 A l 4 C Series Engine Rear Mounts...
Page 634: ...6A1 8 IN LINE 6 Fig 6Al 7 K Series Engine Rear Mount...
Page 660: ......
Page 663: ...SMALL BLOCK 6A4 3 Fig 6A4 T Engine Lubrication...
Page 664: ...6A4 4 SMALL BLOCK Fig 6A4 2 Engine Lubrication...
Page 665: ...Fig 6A4 3 P Series Engine Mount Bracket...
Page 667: ...SMALL BLOCK 6A4 7 Fig 6A 4 5 P Series Engine Front Mount...
Page 668: ...6A4 8 SMALL BLOCK...
Page 669: ...SMALL BLOCK 6A4 9 Fig 6A 4 7 K Series Engine Mounts...
Page 670: ...6A4 10 SMALL BLOCK Fig 6A 4 8 C Series Engine Mounts...
Page 703: ...MARK IV 6A5 7 Fig 6A 5 6 P Series Engine Front Mount...
Page 704: ...6A5 8 MARK IV Fig 6 A 5 7 C Series Engine Mounts...
Page 731: ...6 2 DIESEL 6A7 3...
Page 760: ...6B 6 ENGINE COOLING Fig 6B 7 A C and A I R Adjustment...
Page 771: ...ENGINE COOLING 6B 17 Fig 6B 20 Engine O il C o o le r 6 2L Diesel...
Page 784: ......
Page 807: ...CARBURETOR MODEL 2SE 6C2 9 Fig 6C2 6 Typical 2SE Carburetor Assembly...
Page 820: ......
Page 830: ...6C4 10 CARBURETOR MODEL M4ME M4MC 101368 Fig 6C4 12 M 4M C M 4M E Carburetor Exploded View...
Page 848: ......
Page 876: ......
Page 888: ...6D 12 ENGINE ELECTRICAL Fig 6D 6C Generator Mounting Fig 6D 7C Generator Mounting...
Page 919: ...ENGINE ELECTRICAL 6D 43...
Page 934: ...Fig 6D 8E Starter M otor Mounting...
Page 974: ......
Page 1011: ...Figure 350C 25A Neutral Engine Running AUTOMATIC TRANSMISSION 350C 11...
Page 1054: ...Fig 7A 1C 400 Autom atic Transmission Side Cross Section Typical...
Page 1152: ...700 R4 40 AUTOMATIC TRANSMISSION Figure 700 R4 76 Transmission Assembly Exploded View...
Page 1162: ......
Page 1189: ...89MM MANUAL TRANSMISSION 7B3 5 Fig 7 3 4 4 Speed 89mm Exploded View...
Page 1219: ...CLUTCH 7C 5 Fig 7C 6 C K Truck Clutch Controls...
Page 1220: ...Fig 7C 7 G Truck Clutch Controls...
Page 1221: ...CLUTCH 7C 7 Fig 7C 8 P Truck Clutch Controls...
Page 1234: ...7E 2 TRANSFER CASE Fig 7E 1 Model 208 Transfer Case Cross Section...
Page 1252: ...7E 20 TRANSFER CASE Fig 7E 39 Transfer Case Attachment Typical...
Page 1278: ...8A 16 ELECTRICAL BODY AND CHASSIS Fig 8A 11 License Plate Lamps C K Series...
Page 1280: ...8A 18 ELECTRICAL BODY AND CHASSIS VIEW A VIEW B Fig 8A 15 CK Series Rear Lamp W iring...
Page 1281: ...ELECTRICAL BODY AND CHASSIS 8A 19 Fig 8A 16 CK Series Auxiliary W iring...
Page 1290: ...8B 8 ELECTRICAL AND WIRING Fig 8B 13 Seat Belt Reminder System Schematic...
Page 1292: ......
Page 1346: ...8C 54 INSTRUMENT PANEL AND GAGES Fig 8C 46 CK Series W iring 3 of 29...
Page 1351: ...INSTRUMENT PANEL AND GAGES 8C 59 SUBURBAN Fig 8C 51 CK Series W iring 8 of 29...
Page 1364: ...8C 72 INSTRUMENT PANEL AND GAGES Fig 8C 64 CK Series W iring 21 of 29...
Page 1365: ...INSTRUMENT PANEL AND GAGES 8C 73 CAB CRFW CAB CHASSIS Fig 8C 65 CK Series W iring 22 of 29...
Page 1366: ...8C 74 INSTRUMENT PANEL AND GAGES Fig 8C 66 CK Series W iring 23 of 29...
Page 1374: ...8C 82 INSTRUMENT PANEL AND GAGES Fig 8C 74 G Series W iring 2 of 19...
Page 1375: ...INSTRUMENT PANEL AND GAGES 8C 83 Fig 8C 75 G Series W iring 3 of 19...
Page 1376: ...8C 84 INSTRUMENT PANEL AND GAGES Fig 8C 76 G Series W iring 4 of 19...
Page 1379: ...INSTRUMENT PANEL AND GAGES 8C 87 Fig 8C 79 G Series W iring 7 of 19...
Page 1383: ...INSTRUMENT PANEL AND GAGES 8C 91 Fig 8C 83 G Series W iring 11 o f 19...
Page 1384: ...8C 92 INSTRUMENT PANEL AND GAGES BUS BARGWO Fig 8C 84 G Series W iring 12 of 19...
Page 1390: ...8C 98 INSTRUMENT PANEL AND GAGES Fig 8C 90 G Series W iring 18 of 19...
Page 1391: ...INSTRUMENT PANEL AND GAGES 8C 99 Fig 8C 91 G Series W iring 19 of 19...
Page 1392: ...8C 100 INSTRUMENT PANEL AND GAGES Fig 8C 92 P Series W iring 1 of 11...
Page 1393: ...INSTRUMENT PANEL AND GAGES 8C 101 Fig 8C 93 P Series W iring 2 of 11...
Page 1396: ...8C 104 INSTRUMENT PANEL AND GAGES Fig 8C 96 P Series W iring 5 of 11...
Page 1399: ...INSTRUMENT PANEL AND GAGES 8C 107 Fig 8C 99 P Series W iring 8 of 11...
Page 1401: ...INSTRUMENT PANEL AND GAGES 8C 109 START RUN OF LOCK ACC Fig 8C 101 P Series W iring 10 of 11...
Page 1415: ...ACCESSORIES 9 13 RADIO NOISE BLOWER MOTOR Fig 9 6R Radio Diagnosis Chart B...
Page 1416: ...9 14 ACCESSORIES D E A D R A D IO A M R A D IO I Fig 9 7R Radio Diagnosis Chart C...
Page 1417: ...ACCESSORIES 9 15 DEAD RADIO AM FM RADIO Fig 9 8R Radio Diagnosis Chart D...
Page 1435: ...t f l i t 1...