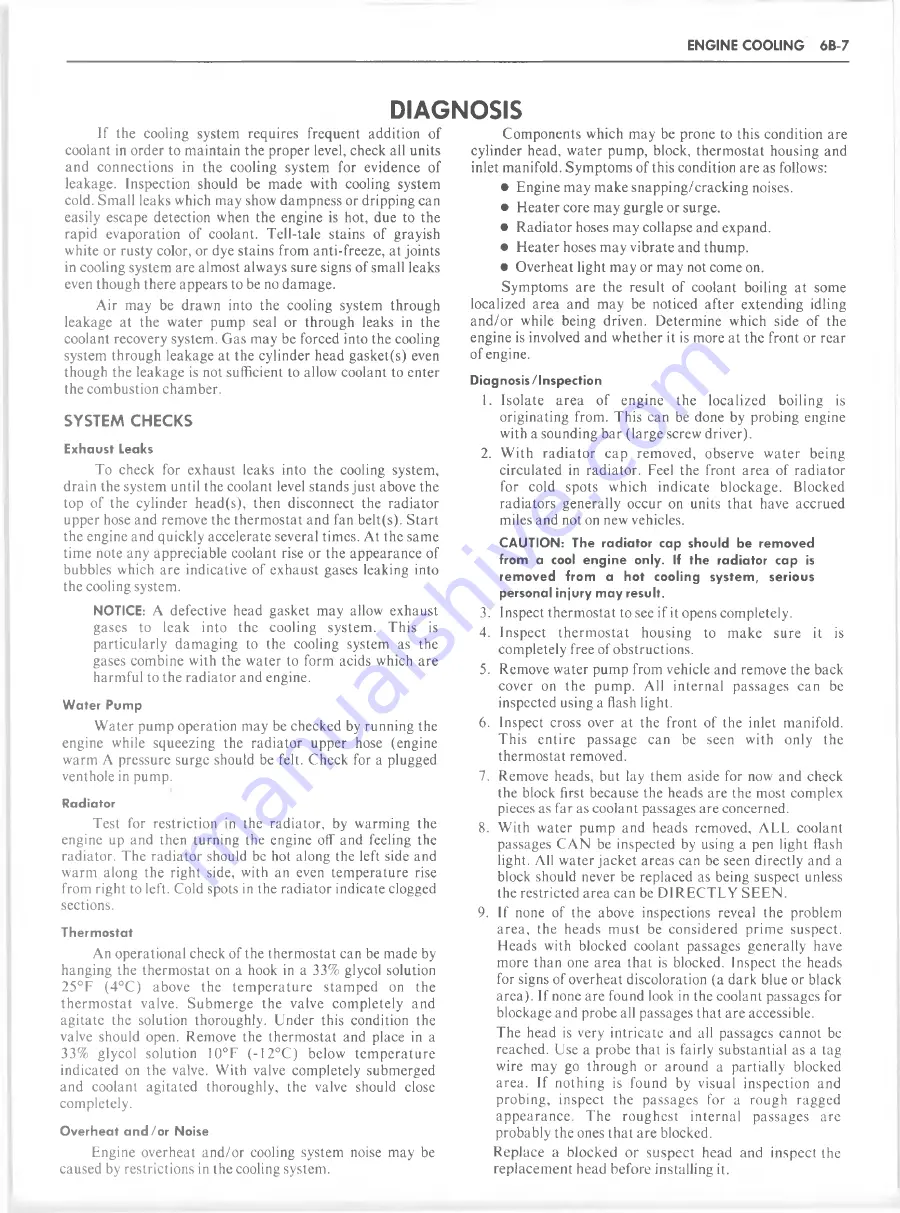
ENGINE COOLING 6B-7
DIAGNOSIS
If the cooling system requires frequent addition of
coolant in order to maintain the proper level, check all units
and connections in the cooling system for evidence of
leakage. Inspection should be made with cooling system
cold. Small leaks which may show dampness or dripping can
easily escape detection when the engine is hot, due to the
rapid evaporation of coolant. Tell-tale stains of grayish
white or rusty color, or dye stains from anti-freeze, at joints
in cooling system are almost always sure signs of small leaks
even though there appears to be no damage.
Air may be drawn into the cooling system through
leakage at the water pump seal or through leaks in the
coolant recovery system. Gas may be forced into the cooling
system through leakage at the cylinder head gasket(s) even
though the leakage is not sufficient to allow coolant to enter
the combustion chamber.
SY ST E M C H E C K S
E x h a u s t Leaks
To check for exhaust leaks into the cooling system,
drain the system until the coolant level stands just above the
top of the cylinder head(s), then disconnect the radiator
upper hose and remove the thermostat and fan belt(s). Start
the engine and quickly accelerate several times. At the same
time note any appreciable coolant rise or the appearance of
bubbles which are indicative of exhaust gases leaking into
the cooling system.
N O TIC E :
A defective head gasket may allow exhaust
gases to leak into the cooling system . This is
particularly damaging to the cooling system as the
gases combine with the water to form acids which are
harmful to the radiator and engine.
W a te r P u m p
Water pump operation may be checked by running the
engine while squeezing the radiator upper hose (engine
warm A pressure surge should be felt. Check for a plugged
venthole in pump.
R a d ia to r
Test for restriction in the radiator, by warming the
engine up and then turning the engine off and feeling the
radiator. The radiator should be hot along the left side and
warm along the right side, with an even temperature rise
from right to left. Cold spots in the radiator indicate clogged
sections.
T h e rm o s ta t
An operational check of the thermostat can be made by
hanging the thermostat on a hook in a 33% glycol solution
25°F (4°C ) above the temperature stamped on the
therm ostat valve. Subm erge the valve com pletely and
agitate the solution thoroughly. Under this condition the
valve should open. Remove the thermostat and place in a
33% glycol solution 10°F (-12°C ) below temperature
indicated on the valve. With valve completely submerged
and coolant agitated thoroughly, the valve should close
completely.
O v e rh e a t a n d / o r N oise
Engine overheat and/or cooling system noise may be
caused by restrictions in the cooling system.
Components which may be prone to this condition are
cylinder head, water pump, block, thermostat housing and
inlet manifold. Symptoms of this condition are as follows:
• Engine may make snapping/cracking noises.
• Heater core may gurgle or surge.
• Radiator hoses may collapse and expand.
• Heater hoses may vibrate and thump.
• Overheat light may or may not come on.
Symptoms are the result of coolant boiling at some
localized area and may be noticed after extending idling
and/or while being driven. Determine which side of the
engine is involved and whether it is more at the front or rear
of engine.
D ia g n o s is /In s p e c tio n
1. Isolate area of engine the localized boiling is
originating from. This can be done by probing engine
with a sounding bar (large screw driver).
2. W ith radiator cap removed, observe water being
circulated in radiator. Feel the front area of radiator
for cold spots which indicate blockage. Blocked
radiators generally occur on units that have accrued
miles and not on new vehicles.
C A U T IO N : T h e ra d ia to r c ap sh ould b e re m o v e d
fro m a cool e n g in e o n ly . If th e ra d ia to r c ap is
re m o v e d fro m a h o t c o o lin g s y s te m , serio u s
perso n al in ju ry m a y re su lt.
3. Inspect thermostat to see if it opens completely.
4. Inspect therm ostat housing to make sure it is
completely free of obstructions.
5. Remove water pump from vehicle and remove the back
cover on the pump. All internal passages can be
inspected using a flash light.
6. Inspect cross over at the front of the inlet manifold.
This entire passage can be seen with only the
thermostat removed.
7. Remove heads, but lay them aside for now and check
the block first because the heads are the most complex
pieces as far as coolant passages are concerned.
8. With water pump and heads removed, ALL coolant
passages C A N be inspected by using a pen light flash
light. All water jacket areas can be seen directly and a
block should never be replaced as being suspect unless
the restricted area can be DIRECTLY SE E N .
9. If none of the above inspections reveal the problem
area, the heads must be considered prime suspect.
Heads with blocked coolant passages generally have
more than one area that is blocked. Inspect the heads
for signs of overheat discoloration (a dark blue or black
area). If none are found look in the coolant passages for
blockage and probe all passages that are accessible.
The head is very intricate and all passages cannot be
reached. Use a probe that is fairly substantial as a tag
wire may go through or around a partially blocked
area. If nothing is found by visual inspection and
probing, inspect the passages for a rough ragged
appearance. The roughest internal passages are
probably the ones that are blocked.
Replace a blocked or suspect head and inspect the
replacement head before installing it.
Summary of Contents for 1982 Light Duty Truck
Page 1: ......
Page 28: ...HEATER 1A 3 Fig lA 2 Heater Control C K Models Fig lA 3 Heater Control G Models...
Page 37: ...Fig 1A 11 T E E V A L V E A S M TEE AND VALVE C36...
Page 38: ...HEATER 1A 13 Fig 1A l2 Distributor Ducts G Models Fig 1A l5 Control Assembly G Models...
Page 39: ...1A 14 HEATER V IE W A V IE W B Fig 1A l7 Control Cable Routing G Models...
Page 42: ...HEATER 1A 19 Fig 1A 23 Auxiliary Heater Hose Routing...
Page 56: ...AIR CONDITIONING IB 13 Chart 1B 4 Pressure Cycling CCOT System Diagnosis...
Page 64: ...Fig 1B 17 C60 System Vacuum Diagram C K Series...
Page 65: ......
Page 66: ...Fig 1B 19 C60 Motor Home Chassis Wiring Diagram SWITCH AIR CONDITIONING IB 2 3...
Page 67: ...IB 24 AIR CONDITIONING Fig IB 20 1 P A C Harness Wiring...
Page 68: ...AIR CONDITIONING IB 25 VIE W A Fig IB 21 A C Compressor wiring...
Page 76: ...AIR CONDITIONING IB 33 Fig 1B 26 Compressor Mounting...
Page 91: ...IB 48 AIR CONDITIONING Fig 1B 59 C K Models Refrigerant Lines L6...
Page 150: ......
Page 162: ......
Page 164: ...2D 2 BODY Fig 2D 4 Typical Utility Vehicle Model...
Page 182: ...2D 20 BODY Fig 2D 51 Rear Door Controls Fig 2D 52 Rear Door Outside Handle and Lock Cylinder...
Page 193: ...BODY 2D 31 BELTS 3RD SEAT Fig 2D 82 Seat Belt Installation Suburban Driver Seat Suburban...
Page 194: ...2D 32 BODY Fig 2D 85 Passenger s Bucket Seat Chassis Cab...
Page 195: ...BODY 2D 33 Fig 2D 88 Rear Bench Seats Suburban...
Page 196: ...2D 34 BODY Fig 2D 89 CK Utility Seat Attachments...
Page 197: ...BODY 2D 35 Fig 2D 90 Seat Separator Compartment and Door CK Models...
Page 222: ......
Page 223: ...BODY 2D 61 Fig 2D 139 Front Seat Belt Installation...
Page 228: ......
Page 234: ......
Page 252: ...3B2 8 MANUAL STEERING GEAR Fig 3B2 11 Manual Steering Gear Exploded View...
Page 256: ......
Page 273: ...POWER STEERING SYSTEM 3B3 17 with LE3 Engine Exc HC4 LE4 LG9 LF4 LS9 LT9 and JB7 HC4 and JB8...
Page 342: ......
Page 389: ...REAR SUSPENSION 3D 7 Fig 3D 17 Rear Spring Installation C K Models...
Page 428: ...4 B 1 4 REAR AXLE Fig 4B 8 Gear Tooth Nomenclature Fig 4B 9 G ear Tooth Contact Pattern Check...
Page 444: ......
Page 454: ......
Page 468: ...4 B 5 2 REAR AXLE Fig 4B5 2 Rockwell Assembly...
Page 480: ...4 B 5 1 4 REAR AXLE...
Page 482: ...i...
Page 502: ......
Page 520: ......
Page 533: ...Fig 5 5 Front Brake Pipes and Hoses C K Models BRAKES 5 13...
Page 534: ...Fig 5 6 Front Brake Pipes and Hoses G M odels 5 14 B R A K E S...
Page 535: ...Fig 5 7 Front Brake Pipes and Hoses P Models BRAKES 5 15...
Page 536: ...5 16 BRAKES Fig 5 8 Rear Brake Hoses...
Page 538: ...5 18 BRAKES Fig 5 10 Parking Brake System Typical...
Page 539: ...BRAKES 5 19...
Page 570: ...5 50 BRAKES Fig 5 57 Power Steering Hose Routing C K Models...
Page 571: ...BRAKES 5 51 Fig 5 58 Power Steering Hose Routing G Models...
Page 572: ...Fig 5 59 Power Steering H ose Routing P Models 5 52 BRAKES...
Page 577: ...BRAKES 5 57 4 CONT A SECONDARY DIAPHRAGM B SECONDARY POWER 4 CONT C PRIMARY D Fig 5 5A Service...
Page 604: ......
Page 625: ...NOTES ENGINE 6 21...
Page 626: ......
Page 629: ...IN LINE 6 6A1 3 OIL PRESSURE SENDING UNIT Fig 6A1 1 In Line Engine Lubrication...
Page 630: ...6A1 4 IN LINE 6 Fig 6 A l 2 P Series Engine Front Mount...
Page 631: ...IN LINE 6 6A1 5 Fig 6Al 3 P Series Engine Rear Mount Fig 6 A l 4 C Series Engine Rear Mounts...
Page 634: ...6A1 8 IN LINE 6 Fig 6Al 7 K Series Engine Rear Mount...
Page 660: ......
Page 663: ...SMALL BLOCK 6A4 3 Fig 6A4 T Engine Lubrication...
Page 664: ...6A4 4 SMALL BLOCK Fig 6A4 2 Engine Lubrication...
Page 665: ...Fig 6A4 3 P Series Engine Mount Bracket...
Page 667: ...SMALL BLOCK 6A4 7 Fig 6A 4 5 P Series Engine Front Mount...
Page 668: ...6A4 8 SMALL BLOCK...
Page 669: ...SMALL BLOCK 6A4 9 Fig 6A 4 7 K Series Engine Mounts...
Page 670: ...6A4 10 SMALL BLOCK Fig 6A 4 8 C Series Engine Mounts...
Page 703: ...MARK IV 6A5 7 Fig 6A 5 6 P Series Engine Front Mount...
Page 704: ...6A5 8 MARK IV Fig 6 A 5 7 C Series Engine Mounts...
Page 731: ...6 2 DIESEL 6A7 3...
Page 760: ...6B 6 ENGINE COOLING Fig 6B 7 A C and A I R Adjustment...
Page 771: ...ENGINE COOLING 6B 17 Fig 6B 20 Engine O il C o o le r 6 2L Diesel...
Page 784: ......
Page 807: ...CARBURETOR MODEL 2SE 6C2 9 Fig 6C2 6 Typical 2SE Carburetor Assembly...
Page 820: ......
Page 830: ...6C4 10 CARBURETOR MODEL M4ME M4MC 101368 Fig 6C4 12 M 4M C M 4M E Carburetor Exploded View...
Page 848: ......
Page 876: ......
Page 888: ...6D 12 ENGINE ELECTRICAL Fig 6D 6C Generator Mounting Fig 6D 7C Generator Mounting...
Page 919: ...ENGINE ELECTRICAL 6D 43...
Page 934: ...Fig 6D 8E Starter M otor Mounting...
Page 974: ......
Page 1011: ...Figure 350C 25A Neutral Engine Running AUTOMATIC TRANSMISSION 350C 11...
Page 1054: ...Fig 7A 1C 400 Autom atic Transmission Side Cross Section Typical...
Page 1152: ...700 R4 40 AUTOMATIC TRANSMISSION Figure 700 R4 76 Transmission Assembly Exploded View...
Page 1162: ......
Page 1189: ...89MM MANUAL TRANSMISSION 7B3 5 Fig 7 3 4 4 Speed 89mm Exploded View...
Page 1219: ...CLUTCH 7C 5 Fig 7C 6 C K Truck Clutch Controls...
Page 1220: ...Fig 7C 7 G Truck Clutch Controls...
Page 1221: ...CLUTCH 7C 7 Fig 7C 8 P Truck Clutch Controls...
Page 1234: ...7E 2 TRANSFER CASE Fig 7E 1 Model 208 Transfer Case Cross Section...
Page 1252: ...7E 20 TRANSFER CASE Fig 7E 39 Transfer Case Attachment Typical...
Page 1278: ...8A 16 ELECTRICAL BODY AND CHASSIS Fig 8A 11 License Plate Lamps C K Series...
Page 1280: ...8A 18 ELECTRICAL BODY AND CHASSIS VIEW A VIEW B Fig 8A 15 CK Series Rear Lamp W iring...
Page 1281: ...ELECTRICAL BODY AND CHASSIS 8A 19 Fig 8A 16 CK Series Auxiliary W iring...
Page 1290: ...8B 8 ELECTRICAL AND WIRING Fig 8B 13 Seat Belt Reminder System Schematic...
Page 1292: ......
Page 1346: ...8C 54 INSTRUMENT PANEL AND GAGES Fig 8C 46 CK Series W iring 3 of 29...
Page 1351: ...INSTRUMENT PANEL AND GAGES 8C 59 SUBURBAN Fig 8C 51 CK Series W iring 8 of 29...
Page 1364: ...8C 72 INSTRUMENT PANEL AND GAGES Fig 8C 64 CK Series W iring 21 of 29...
Page 1365: ...INSTRUMENT PANEL AND GAGES 8C 73 CAB CRFW CAB CHASSIS Fig 8C 65 CK Series W iring 22 of 29...
Page 1366: ...8C 74 INSTRUMENT PANEL AND GAGES Fig 8C 66 CK Series W iring 23 of 29...
Page 1374: ...8C 82 INSTRUMENT PANEL AND GAGES Fig 8C 74 G Series W iring 2 of 19...
Page 1375: ...INSTRUMENT PANEL AND GAGES 8C 83 Fig 8C 75 G Series W iring 3 of 19...
Page 1376: ...8C 84 INSTRUMENT PANEL AND GAGES Fig 8C 76 G Series W iring 4 of 19...
Page 1379: ...INSTRUMENT PANEL AND GAGES 8C 87 Fig 8C 79 G Series W iring 7 of 19...
Page 1383: ...INSTRUMENT PANEL AND GAGES 8C 91 Fig 8C 83 G Series W iring 11 o f 19...
Page 1384: ...8C 92 INSTRUMENT PANEL AND GAGES BUS BARGWO Fig 8C 84 G Series W iring 12 of 19...
Page 1390: ...8C 98 INSTRUMENT PANEL AND GAGES Fig 8C 90 G Series W iring 18 of 19...
Page 1391: ...INSTRUMENT PANEL AND GAGES 8C 99 Fig 8C 91 G Series W iring 19 of 19...
Page 1392: ...8C 100 INSTRUMENT PANEL AND GAGES Fig 8C 92 P Series W iring 1 of 11...
Page 1393: ...INSTRUMENT PANEL AND GAGES 8C 101 Fig 8C 93 P Series W iring 2 of 11...
Page 1396: ...8C 104 INSTRUMENT PANEL AND GAGES Fig 8C 96 P Series W iring 5 of 11...
Page 1399: ...INSTRUMENT PANEL AND GAGES 8C 107 Fig 8C 99 P Series W iring 8 of 11...
Page 1401: ...INSTRUMENT PANEL AND GAGES 8C 109 START RUN OF LOCK ACC Fig 8C 101 P Series W iring 10 of 11...
Page 1415: ...ACCESSORIES 9 13 RADIO NOISE BLOWER MOTOR Fig 9 6R Radio Diagnosis Chart B...
Page 1416: ...9 14 ACCESSORIES D E A D R A D IO A M R A D IO I Fig 9 7R Radio Diagnosis Chart C...
Page 1417: ...ACCESSORIES 9 15 DEAD RADIO AM FM RADIO Fig 9 8R Radio Diagnosis Chart D...
Page 1435: ...t f l i t 1...