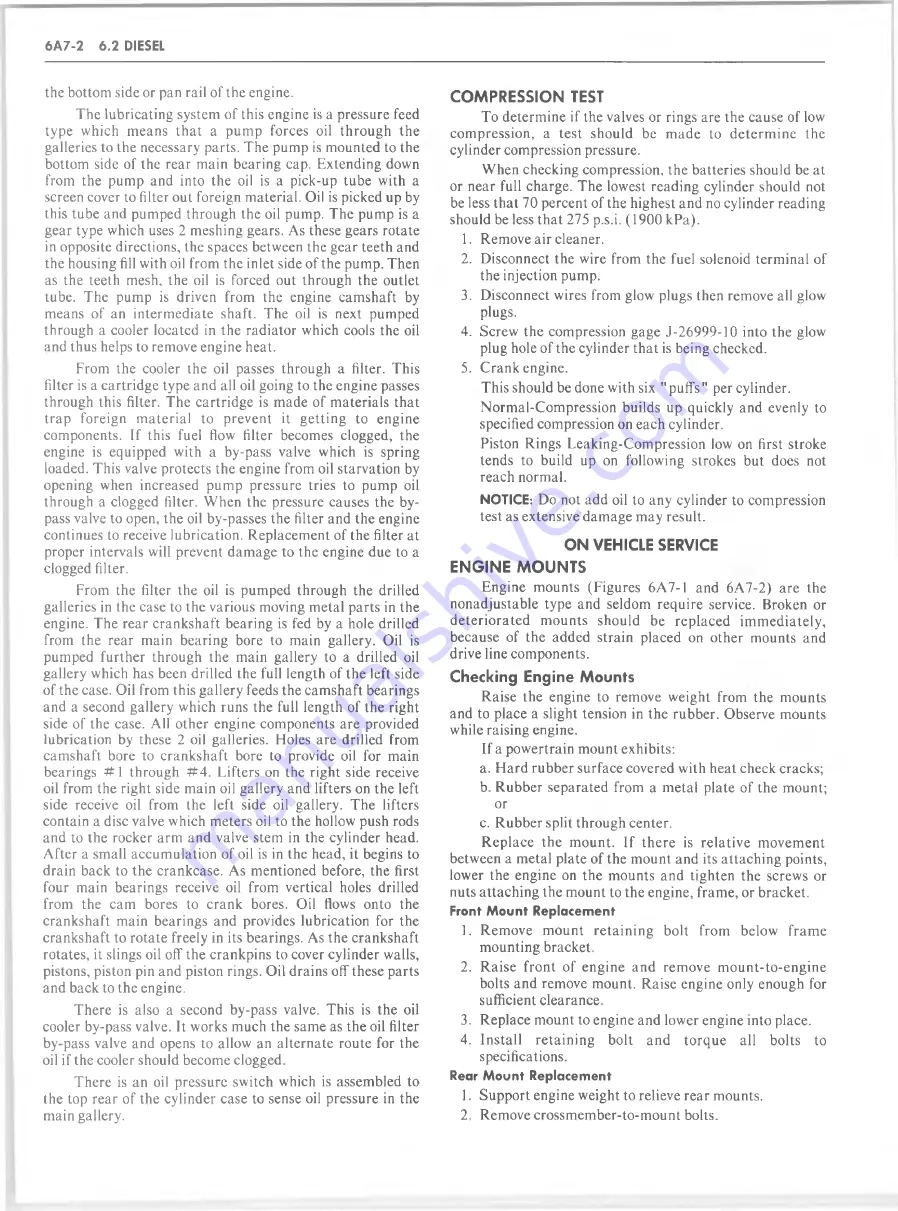
6A7-2 6.2 DIESEL
the bottom side or pan rail of the engine.
The lubricating system of this engine is a pressure feed
type which means that a pump forces oil through the
galleries to the necessary parts. The pump is mounted to the
bottom side of the rear main bearing cap. Extending down
from the pump and into the oil is a pick-up tube with a
screen cover to filter out foreign material. Oil is picked up by
this tube and pumped through the oil pump. The pump is a
gear type which uses 2 meshing gears. As these gears rotate
in opposite directions, the spaces between the gear teeth and
the housing fill with oil from the inlet side of the pump. Then
as the teeth mesh, the oil is forced out through the outlet
tube. The pump is driven from the engine camshaft by
means of an intermediate shaft. The oil is next pumped
through a cooler located in the radiator which cools the oil
and thus helps to remove engine heat.
From the cooler the oil passes through a filter. This
filter is a cartridge type and all oil going to the engine passes
through this filter. The cartridge is made of materials that
trap foreign m aterial to prevent it getting to engine
components. If this fuel flow filter becomes clogged, the
engine is equipped with a by-pass valve which is spring
loaded. This valve protects the engine from oil starvation by
opening when increased pump pressure tries to pump oil
through a clogged filter. When the pressure causes the by
pass valve to open, the oil by-passes the filter and the engine
continues to receive lubrication. Replacement of the filter at
proper intervals will prevent damage to the engine due to a
clogged filter.
From the filter the oil is pumped through the drilled
galleries in the case to the various moving metal parts in the
engine. The rear crankshaft bearing is fed by a hole drilled
from the rear main bearing bore to main gallery. Oil is
pumped further through the main gallery to a drilled oil
gallery which has been drilled the full length of the left side
of the case. Oil from this gallery feeds the camshaft bearings
and a second gallery which runs the full length of the right
side of the case. All other engine components are provided
lubrication by these 2 oil galleries. Holes are drilled from
camshaft bore to crankshaft bore to provide oil for main
bearings # 1 through # 4 . Lifters on the right side receive
oil from the right side main oil gallery and lifters on the left
side receive oil from the left side oil gallery. The lifters
contain a disc valve which meters oil to the hollow push rods
and to the rocker arm and valve stem in the cylinder head.
After a small accumulation of oil is in the head, it begins to
drain back to the crankcase. As mentioned before, the first
four main bearings receive oil from vertical holes drilled
from the cam bores to crank bores. Oil flows onto the
crankshaft main bearings and provides lubrication for the
crankshaft to rotate freely in its bearings. As the crankshaft
rotates, it slings oil off the crankpins to cover cylinder walls,
pistons, piston pin and piston rings. Oil drains off these parts
and back to the engine.
There is also a second by-pass valve. This is the oil
cooler by-pass valve. It works much the same as the oil filter
by-pass valve and opens to allow an alternate route for the
oil if the cooler should become clogged.
There is an oil pressure switch which is assembled to
the top rear of the cylinder case to sense oil pressure in the
main gallery.
C O M P R E S S IO N TEST
To determine if the valves or rings are the cause of low
com pression, a test should be made to determ ine the
cylinder compression pressure.
When checking compression, the batteries should be at
or near full charge. The lowest reading cylinder should not
be less that 70 percent of the highest and no cylinder reading
should be less that 275 p.s.i. (1900 kPa).
1. Remove air cleaner.
2. Disconnect the wire from the fuel solenoid terminal of
the injection pump.
3. Disconnect wires from glow plugs then remove all glow
plugs.
4. Screw the compression gage J-26999-10 into the glow
plug hole of the cylinder that is being checked.
5. Crank engine.
This should be done with six "puffs" per cylinder.
Normal-Compression builds up quickly and evenly to
specified compression on each cylinder.
Piston Rings Leaking-Compression low on first stroke
tends to build up on following strokes but does not
reach normal.
N O T IC E :
Do not add oil to any cylinder to compression
test as extensive damage may result.
O N VEHICLE SERVICE
E N G IN E M O U N T S
Engine mounts (Figures 6A7-1 and 6A7-2) are the
nonadjustable type and seldom require service. Broken or
deteriorated mounts should be replaced im m ediately,
because of the added strain placed on other mounts and
drive line components.
Checking Engine M ounts
Raise the engine to remove weight from the mounts
and to place a slight tension in the rubber. Observe mounts
while raising engine.
If a powertrain mount exhibits:
a. Hard rubber surface covered with heat check cracks;
b. Rubber separated from a metal plate of the mount;
or
c. Rubber split through center.
R eplace the mount. If there is relative movement
between a metal plate of the mount and its attaching points,
lower the engine on the mounts and tighten the screws or
nuts attaching the mount to the engine, frame, or bracket.
Front M ount R e p lace m e n t
1. Rem ove mount retaining bolt from below frame
mounting bracket.
2. Raise front of engine and remove m ount-to-engine
bolts and remove mount. Raise engine only enough for
sufficient clearance.
3. Replace mount to engine and lower engine into place.
4. Install retaining bolt and torque all bolts to
specifications.
Rear M ount R e p lace m e n t
1. Support engine weight to relieve rear mounts.
2. Remove crossmember-to-mount bolts.
Summary of Contents for 1982 Light Duty Truck
Page 1: ......
Page 28: ...HEATER 1A 3 Fig lA 2 Heater Control C K Models Fig lA 3 Heater Control G Models...
Page 37: ...Fig 1A 11 T E E V A L V E A S M TEE AND VALVE C36...
Page 38: ...HEATER 1A 13 Fig 1A l2 Distributor Ducts G Models Fig 1A l5 Control Assembly G Models...
Page 39: ...1A 14 HEATER V IE W A V IE W B Fig 1A l7 Control Cable Routing G Models...
Page 42: ...HEATER 1A 19 Fig 1A 23 Auxiliary Heater Hose Routing...
Page 56: ...AIR CONDITIONING IB 13 Chart 1B 4 Pressure Cycling CCOT System Diagnosis...
Page 64: ...Fig 1B 17 C60 System Vacuum Diagram C K Series...
Page 65: ......
Page 66: ...Fig 1B 19 C60 Motor Home Chassis Wiring Diagram SWITCH AIR CONDITIONING IB 2 3...
Page 67: ...IB 24 AIR CONDITIONING Fig IB 20 1 P A C Harness Wiring...
Page 68: ...AIR CONDITIONING IB 25 VIE W A Fig IB 21 A C Compressor wiring...
Page 76: ...AIR CONDITIONING IB 33 Fig 1B 26 Compressor Mounting...
Page 91: ...IB 48 AIR CONDITIONING Fig 1B 59 C K Models Refrigerant Lines L6...
Page 150: ......
Page 162: ......
Page 164: ...2D 2 BODY Fig 2D 4 Typical Utility Vehicle Model...
Page 182: ...2D 20 BODY Fig 2D 51 Rear Door Controls Fig 2D 52 Rear Door Outside Handle and Lock Cylinder...
Page 193: ...BODY 2D 31 BELTS 3RD SEAT Fig 2D 82 Seat Belt Installation Suburban Driver Seat Suburban...
Page 194: ...2D 32 BODY Fig 2D 85 Passenger s Bucket Seat Chassis Cab...
Page 195: ...BODY 2D 33 Fig 2D 88 Rear Bench Seats Suburban...
Page 196: ...2D 34 BODY Fig 2D 89 CK Utility Seat Attachments...
Page 197: ...BODY 2D 35 Fig 2D 90 Seat Separator Compartment and Door CK Models...
Page 222: ......
Page 223: ...BODY 2D 61 Fig 2D 139 Front Seat Belt Installation...
Page 228: ......
Page 234: ......
Page 252: ...3B2 8 MANUAL STEERING GEAR Fig 3B2 11 Manual Steering Gear Exploded View...
Page 256: ......
Page 273: ...POWER STEERING SYSTEM 3B3 17 with LE3 Engine Exc HC4 LE4 LG9 LF4 LS9 LT9 and JB7 HC4 and JB8...
Page 342: ......
Page 389: ...REAR SUSPENSION 3D 7 Fig 3D 17 Rear Spring Installation C K Models...
Page 428: ...4 B 1 4 REAR AXLE Fig 4B 8 Gear Tooth Nomenclature Fig 4B 9 G ear Tooth Contact Pattern Check...
Page 444: ......
Page 454: ......
Page 468: ...4 B 5 2 REAR AXLE Fig 4B5 2 Rockwell Assembly...
Page 480: ...4 B 5 1 4 REAR AXLE...
Page 482: ...i...
Page 502: ......
Page 520: ......
Page 533: ...Fig 5 5 Front Brake Pipes and Hoses C K Models BRAKES 5 13...
Page 534: ...Fig 5 6 Front Brake Pipes and Hoses G M odels 5 14 B R A K E S...
Page 535: ...Fig 5 7 Front Brake Pipes and Hoses P Models BRAKES 5 15...
Page 536: ...5 16 BRAKES Fig 5 8 Rear Brake Hoses...
Page 538: ...5 18 BRAKES Fig 5 10 Parking Brake System Typical...
Page 539: ...BRAKES 5 19...
Page 570: ...5 50 BRAKES Fig 5 57 Power Steering Hose Routing C K Models...
Page 571: ...BRAKES 5 51 Fig 5 58 Power Steering Hose Routing G Models...
Page 572: ...Fig 5 59 Power Steering H ose Routing P Models 5 52 BRAKES...
Page 577: ...BRAKES 5 57 4 CONT A SECONDARY DIAPHRAGM B SECONDARY POWER 4 CONT C PRIMARY D Fig 5 5A Service...
Page 604: ......
Page 625: ...NOTES ENGINE 6 21...
Page 626: ......
Page 629: ...IN LINE 6 6A1 3 OIL PRESSURE SENDING UNIT Fig 6A1 1 In Line Engine Lubrication...
Page 630: ...6A1 4 IN LINE 6 Fig 6 A l 2 P Series Engine Front Mount...
Page 631: ...IN LINE 6 6A1 5 Fig 6Al 3 P Series Engine Rear Mount Fig 6 A l 4 C Series Engine Rear Mounts...
Page 634: ...6A1 8 IN LINE 6 Fig 6Al 7 K Series Engine Rear Mount...
Page 660: ......
Page 663: ...SMALL BLOCK 6A4 3 Fig 6A4 T Engine Lubrication...
Page 664: ...6A4 4 SMALL BLOCK Fig 6A4 2 Engine Lubrication...
Page 665: ...Fig 6A4 3 P Series Engine Mount Bracket...
Page 667: ...SMALL BLOCK 6A4 7 Fig 6A 4 5 P Series Engine Front Mount...
Page 668: ...6A4 8 SMALL BLOCK...
Page 669: ...SMALL BLOCK 6A4 9 Fig 6A 4 7 K Series Engine Mounts...
Page 670: ...6A4 10 SMALL BLOCK Fig 6A 4 8 C Series Engine Mounts...
Page 703: ...MARK IV 6A5 7 Fig 6A 5 6 P Series Engine Front Mount...
Page 704: ...6A5 8 MARK IV Fig 6 A 5 7 C Series Engine Mounts...
Page 731: ...6 2 DIESEL 6A7 3...
Page 760: ...6B 6 ENGINE COOLING Fig 6B 7 A C and A I R Adjustment...
Page 771: ...ENGINE COOLING 6B 17 Fig 6B 20 Engine O il C o o le r 6 2L Diesel...
Page 784: ......
Page 807: ...CARBURETOR MODEL 2SE 6C2 9 Fig 6C2 6 Typical 2SE Carburetor Assembly...
Page 820: ......
Page 830: ...6C4 10 CARBURETOR MODEL M4ME M4MC 101368 Fig 6C4 12 M 4M C M 4M E Carburetor Exploded View...
Page 848: ......
Page 876: ......
Page 888: ...6D 12 ENGINE ELECTRICAL Fig 6D 6C Generator Mounting Fig 6D 7C Generator Mounting...
Page 919: ...ENGINE ELECTRICAL 6D 43...
Page 934: ...Fig 6D 8E Starter M otor Mounting...
Page 974: ......
Page 1011: ...Figure 350C 25A Neutral Engine Running AUTOMATIC TRANSMISSION 350C 11...
Page 1054: ...Fig 7A 1C 400 Autom atic Transmission Side Cross Section Typical...
Page 1152: ...700 R4 40 AUTOMATIC TRANSMISSION Figure 700 R4 76 Transmission Assembly Exploded View...
Page 1162: ......
Page 1189: ...89MM MANUAL TRANSMISSION 7B3 5 Fig 7 3 4 4 Speed 89mm Exploded View...
Page 1219: ...CLUTCH 7C 5 Fig 7C 6 C K Truck Clutch Controls...
Page 1220: ...Fig 7C 7 G Truck Clutch Controls...
Page 1221: ...CLUTCH 7C 7 Fig 7C 8 P Truck Clutch Controls...
Page 1234: ...7E 2 TRANSFER CASE Fig 7E 1 Model 208 Transfer Case Cross Section...
Page 1252: ...7E 20 TRANSFER CASE Fig 7E 39 Transfer Case Attachment Typical...
Page 1278: ...8A 16 ELECTRICAL BODY AND CHASSIS Fig 8A 11 License Plate Lamps C K Series...
Page 1280: ...8A 18 ELECTRICAL BODY AND CHASSIS VIEW A VIEW B Fig 8A 15 CK Series Rear Lamp W iring...
Page 1281: ...ELECTRICAL BODY AND CHASSIS 8A 19 Fig 8A 16 CK Series Auxiliary W iring...
Page 1290: ...8B 8 ELECTRICAL AND WIRING Fig 8B 13 Seat Belt Reminder System Schematic...
Page 1292: ......
Page 1346: ...8C 54 INSTRUMENT PANEL AND GAGES Fig 8C 46 CK Series W iring 3 of 29...
Page 1351: ...INSTRUMENT PANEL AND GAGES 8C 59 SUBURBAN Fig 8C 51 CK Series W iring 8 of 29...
Page 1364: ...8C 72 INSTRUMENT PANEL AND GAGES Fig 8C 64 CK Series W iring 21 of 29...
Page 1365: ...INSTRUMENT PANEL AND GAGES 8C 73 CAB CRFW CAB CHASSIS Fig 8C 65 CK Series W iring 22 of 29...
Page 1366: ...8C 74 INSTRUMENT PANEL AND GAGES Fig 8C 66 CK Series W iring 23 of 29...
Page 1374: ...8C 82 INSTRUMENT PANEL AND GAGES Fig 8C 74 G Series W iring 2 of 19...
Page 1375: ...INSTRUMENT PANEL AND GAGES 8C 83 Fig 8C 75 G Series W iring 3 of 19...
Page 1376: ...8C 84 INSTRUMENT PANEL AND GAGES Fig 8C 76 G Series W iring 4 of 19...
Page 1379: ...INSTRUMENT PANEL AND GAGES 8C 87 Fig 8C 79 G Series W iring 7 of 19...
Page 1383: ...INSTRUMENT PANEL AND GAGES 8C 91 Fig 8C 83 G Series W iring 11 o f 19...
Page 1384: ...8C 92 INSTRUMENT PANEL AND GAGES BUS BARGWO Fig 8C 84 G Series W iring 12 of 19...
Page 1390: ...8C 98 INSTRUMENT PANEL AND GAGES Fig 8C 90 G Series W iring 18 of 19...
Page 1391: ...INSTRUMENT PANEL AND GAGES 8C 99 Fig 8C 91 G Series W iring 19 of 19...
Page 1392: ...8C 100 INSTRUMENT PANEL AND GAGES Fig 8C 92 P Series W iring 1 of 11...
Page 1393: ...INSTRUMENT PANEL AND GAGES 8C 101 Fig 8C 93 P Series W iring 2 of 11...
Page 1396: ...8C 104 INSTRUMENT PANEL AND GAGES Fig 8C 96 P Series W iring 5 of 11...
Page 1399: ...INSTRUMENT PANEL AND GAGES 8C 107 Fig 8C 99 P Series W iring 8 of 11...
Page 1401: ...INSTRUMENT PANEL AND GAGES 8C 109 START RUN OF LOCK ACC Fig 8C 101 P Series W iring 10 of 11...
Page 1415: ...ACCESSORIES 9 13 RADIO NOISE BLOWER MOTOR Fig 9 6R Radio Diagnosis Chart B...
Page 1416: ...9 14 ACCESSORIES D E A D R A D IO A M R A D IO I Fig 9 7R Radio Diagnosis Chart C...
Page 1417: ...ACCESSORIES 9 15 DEAD RADIO AM FM RADIO Fig 9 8R Radio Diagnosis Chart D...
Page 1435: ...t f l i t 1...