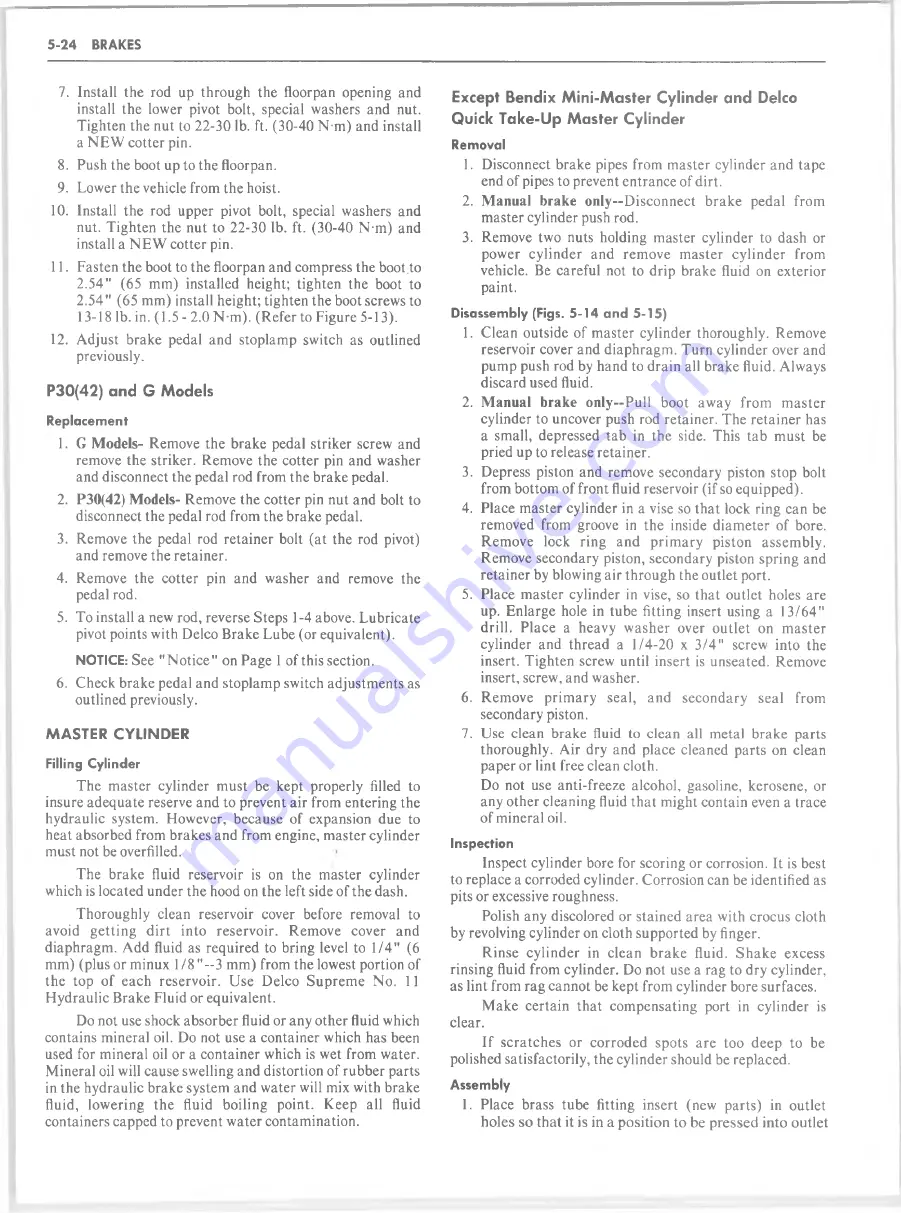
5-24
BRAKES
7. Install the rod up through the floorpan opening and
install the lower pivot bolt, special washers and nut.
Tighten the nut to 22-30 lb. ft. (30-40 N-m) and install
a NEW cotter pin.
8. Push the boot up to the floorpan.
9. Lower the vehicle from the hoist.
10. Install the rod upper pivot bolt, special washers and
nut. Tighten the nut to 22-30 lb. ft. (30-40 N-m) and
install a NEW cotter pin.
11. Fasten the boot to the floorpan and compress the boot,to
2.54" (65 mm) installed height; tighten the boot to
2.54" (65 mm) install height; tighten the boot screws to
13-18 lb. in. (1.5 - 2.0 N-m). (Refer to Figure 5-13).
12. Adjust brake pedal and stoplamp switch as outlined
previously.
P30(42) and G M odels
Replacement
1. G Models- Remove the brake pedal striker screw and
remove the striker. Remove the cotter pin and washer
and disconnect the pedal rod from the brake pedal.
2. P30(42) Models- Remove the cotter pin nut and bolt to
disconnect the pedal rod from the brake pedal.
3. Remove the pedal rod retainer bolt (at the rod pivot)
and remove the retainer.
4. Remove the cotter pin and washer and remove the
pedal rod.
5. To install a new rod, reverse Steps 1-4 above. Lubricate
pivot points with Delco Brake Lube (or equivalent).
NOTICE:
See "Notice" on Page 1 of this section.
6. Check brake pedal and stoplamp switch adjustments as
outlined previously.
MASTER CYLINDER
Filling Cylinder
The master cylinder must be kept properly filled to
insure adequate reserve and to prevent air from entering the
hydraulic system. However, because of expansion due to
heat absorbed from brakes and from engine, master cylinder
must not be overfilled.
The brake fluid reservoir is on the master cylinder
which is located under the hood on the left side of the dash.
Thoroughly clean reservoir cover before removal to
avoid getting dirt into reservoir. Remove cover and
diaphragm. Add fluid as required to bring level to 1/4" (6
mm) (plus or minux 1 /8 " —3 mm) from the lowest portion of
the top of each reservoir. Use Delco Supreme No. 11
Hydraulic Brake Fluid or equivalent.
Do not use shock absorber fluid or any other fluid which
contains mineral oil. Do not use a container which has been
used for mineral oil or a container which is wet from water.
Mineral oil will cause swelling and distortion of rubber parts
in the hydraulic brake system and water will mix with brake
fluid, lowering the fluid boiling point. Keep all fluid
containers capped to prevent water contamination.
Except Bendix M ini-M aster Cylinder and Delco
Quick Take-Up M aster Cylinder
Removal
1. Disconnect brake pipes from master cylinder and tape
end of pipes to prevent entrance of dirt.
2. Manual brake only—Disconnect brake pedal from
master cylinder push rod.
3. Remove two nuts holding master cylinder to dash or
power cylinder and remove master cylinder from
vehicle. Be careful not to drip brake fluid on exterior
paint.
Disassembly (Figs. 5 -14 and 5-15)
1. Clean outside of master cylinder thoroughly. Remove
reservoir cover and diaphragm. Turn cylinder over and
pump push rod by hand to drain all brake fluid. Always
discard used fluid.
2. Manual brake only—Pull boot away from master
cylinder to uncover push rod retainer. The retainer has
a small, depressed tab in the side. This tab must be
pried up to release retainer.
3. Depress piston and remove secondary piston stop bolt
from bottom of front fluid reservoir (if so equipped).
4. Place master cylinder in a vise so that lock ring can be
removed from groove in the inside diameter of bore.
Remove lock ring and primary piston assembly.
Remove secondary piston, secondary piston spring and
retainer by blowing air through the outlet port.
5. Place master cylinder in vise, so that outlet holes are
up. Enlarge hole in tube fitting insert using a 13/64"
drill. Place a heavy washer over outlet on master
cylinder and thread a 1/4-20 x 3/4" screw into the
insert. Tighten screw until insert is unseated. Remove
insert, screw, and washer.
6. Remove primary seal, and secondary seal from
secondary piston.
7. Use clean brake fluid to clean all metal brake parts
thoroughly. Air dry and place cleaned parts on clean
paper or lint free clean cloth.
Do not use anti-freeze alcohol, gasoline, kerosene, or
any other cleaning fluid that might contain even a trace
of mineral oil.
Inspection
Inspect cylinder bore for scoring or corrosion. It is best
to replace a corroded cylinder. Corrosion can be identified as
pits or excessive roughness.
Polish any discolored or stained area with crocus cloth
by revolving cylinder on cloth supported by finger.
Rinse cylinder in clean brake fluid. Shake excess
rinsing fluid from cylinder. Do not use a rag to dry cylinder,
as lint from rag cannot be kept from cylinder bore surfaces.
Make certain that compensating port in cylinder is
clear.
If scratches or corroded spots are too deep to be
polished satisfactorily, the cylinder should be replaced.
Assembly
1. Place brass tube fitting insert (new parts) in outlet
holes so that it is in a position to be pressed into outlet
Summary of Contents for 1982 Light Duty Truck
Page 1: ......
Page 28: ...HEATER 1A 3 Fig lA 2 Heater Control C K Models Fig lA 3 Heater Control G Models...
Page 37: ...Fig 1A 11 T E E V A L V E A S M TEE AND VALVE C36...
Page 38: ...HEATER 1A 13 Fig 1A l2 Distributor Ducts G Models Fig 1A l5 Control Assembly G Models...
Page 39: ...1A 14 HEATER V IE W A V IE W B Fig 1A l7 Control Cable Routing G Models...
Page 42: ...HEATER 1A 19 Fig 1A 23 Auxiliary Heater Hose Routing...
Page 56: ...AIR CONDITIONING IB 13 Chart 1B 4 Pressure Cycling CCOT System Diagnosis...
Page 64: ...Fig 1B 17 C60 System Vacuum Diagram C K Series...
Page 65: ......
Page 66: ...Fig 1B 19 C60 Motor Home Chassis Wiring Diagram SWITCH AIR CONDITIONING IB 2 3...
Page 67: ...IB 24 AIR CONDITIONING Fig IB 20 1 P A C Harness Wiring...
Page 68: ...AIR CONDITIONING IB 25 VIE W A Fig IB 21 A C Compressor wiring...
Page 76: ...AIR CONDITIONING IB 33 Fig 1B 26 Compressor Mounting...
Page 91: ...IB 48 AIR CONDITIONING Fig 1B 59 C K Models Refrigerant Lines L6...
Page 150: ......
Page 162: ......
Page 164: ...2D 2 BODY Fig 2D 4 Typical Utility Vehicle Model...
Page 182: ...2D 20 BODY Fig 2D 51 Rear Door Controls Fig 2D 52 Rear Door Outside Handle and Lock Cylinder...
Page 193: ...BODY 2D 31 BELTS 3RD SEAT Fig 2D 82 Seat Belt Installation Suburban Driver Seat Suburban...
Page 194: ...2D 32 BODY Fig 2D 85 Passenger s Bucket Seat Chassis Cab...
Page 195: ...BODY 2D 33 Fig 2D 88 Rear Bench Seats Suburban...
Page 196: ...2D 34 BODY Fig 2D 89 CK Utility Seat Attachments...
Page 197: ...BODY 2D 35 Fig 2D 90 Seat Separator Compartment and Door CK Models...
Page 222: ......
Page 223: ...BODY 2D 61 Fig 2D 139 Front Seat Belt Installation...
Page 228: ......
Page 234: ......
Page 252: ...3B2 8 MANUAL STEERING GEAR Fig 3B2 11 Manual Steering Gear Exploded View...
Page 256: ......
Page 273: ...POWER STEERING SYSTEM 3B3 17 with LE3 Engine Exc HC4 LE4 LG9 LF4 LS9 LT9 and JB7 HC4 and JB8...
Page 342: ......
Page 389: ...REAR SUSPENSION 3D 7 Fig 3D 17 Rear Spring Installation C K Models...
Page 428: ...4 B 1 4 REAR AXLE Fig 4B 8 Gear Tooth Nomenclature Fig 4B 9 G ear Tooth Contact Pattern Check...
Page 444: ......
Page 454: ......
Page 468: ...4 B 5 2 REAR AXLE Fig 4B5 2 Rockwell Assembly...
Page 480: ...4 B 5 1 4 REAR AXLE...
Page 482: ...i...
Page 502: ......
Page 520: ......
Page 533: ...Fig 5 5 Front Brake Pipes and Hoses C K Models BRAKES 5 13...
Page 534: ...Fig 5 6 Front Brake Pipes and Hoses G M odels 5 14 B R A K E S...
Page 535: ...Fig 5 7 Front Brake Pipes and Hoses P Models BRAKES 5 15...
Page 536: ...5 16 BRAKES Fig 5 8 Rear Brake Hoses...
Page 538: ...5 18 BRAKES Fig 5 10 Parking Brake System Typical...
Page 539: ...BRAKES 5 19...
Page 570: ...5 50 BRAKES Fig 5 57 Power Steering Hose Routing C K Models...
Page 571: ...BRAKES 5 51 Fig 5 58 Power Steering Hose Routing G Models...
Page 572: ...Fig 5 59 Power Steering H ose Routing P Models 5 52 BRAKES...
Page 577: ...BRAKES 5 57 4 CONT A SECONDARY DIAPHRAGM B SECONDARY POWER 4 CONT C PRIMARY D Fig 5 5A Service...
Page 604: ......
Page 625: ...NOTES ENGINE 6 21...
Page 626: ......
Page 629: ...IN LINE 6 6A1 3 OIL PRESSURE SENDING UNIT Fig 6A1 1 In Line Engine Lubrication...
Page 630: ...6A1 4 IN LINE 6 Fig 6 A l 2 P Series Engine Front Mount...
Page 631: ...IN LINE 6 6A1 5 Fig 6Al 3 P Series Engine Rear Mount Fig 6 A l 4 C Series Engine Rear Mounts...
Page 634: ...6A1 8 IN LINE 6 Fig 6Al 7 K Series Engine Rear Mount...
Page 660: ......
Page 663: ...SMALL BLOCK 6A4 3 Fig 6A4 T Engine Lubrication...
Page 664: ...6A4 4 SMALL BLOCK Fig 6A4 2 Engine Lubrication...
Page 665: ...Fig 6A4 3 P Series Engine Mount Bracket...
Page 667: ...SMALL BLOCK 6A4 7 Fig 6A 4 5 P Series Engine Front Mount...
Page 668: ...6A4 8 SMALL BLOCK...
Page 669: ...SMALL BLOCK 6A4 9 Fig 6A 4 7 K Series Engine Mounts...
Page 670: ...6A4 10 SMALL BLOCK Fig 6A 4 8 C Series Engine Mounts...
Page 703: ...MARK IV 6A5 7 Fig 6A 5 6 P Series Engine Front Mount...
Page 704: ...6A5 8 MARK IV Fig 6 A 5 7 C Series Engine Mounts...
Page 731: ...6 2 DIESEL 6A7 3...
Page 760: ...6B 6 ENGINE COOLING Fig 6B 7 A C and A I R Adjustment...
Page 771: ...ENGINE COOLING 6B 17 Fig 6B 20 Engine O il C o o le r 6 2L Diesel...
Page 784: ......
Page 807: ...CARBURETOR MODEL 2SE 6C2 9 Fig 6C2 6 Typical 2SE Carburetor Assembly...
Page 820: ......
Page 830: ...6C4 10 CARBURETOR MODEL M4ME M4MC 101368 Fig 6C4 12 M 4M C M 4M E Carburetor Exploded View...
Page 848: ......
Page 876: ......
Page 888: ...6D 12 ENGINE ELECTRICAL Fig 6D 6C Generator Mounting Fig 6D 7C Generator Mounting...
Page 919: ...ENGINE ELECTRICAL 6D 43...
Page 934: ...Fig 6D 8E Starter M otor Mounting...
Page 974: ......
Page 1011: ...Figure 350C 25A Neutral Engine Running AUTOMATIC TRANSMISSION 350C 11...
Page 1054: ...Fig 7A 1C 400 Autom atic Transmission Side Cross Section Typical...
Page 1152: ...700 R4 40 AUTOMATIC TRANSMISSION Figure 700 R4 76 Transmission Assembly Exploded View...
Page 1162: ......
Page 1189: ...89MM MANUAL TRANSMISSION 7B3 5 Fig 7 3 4 4 Speed 89mm Exploded View...
Page 1219: ...CLUTCH 7C 5 Fig 7C 6 C K Truck Clutch Controls...
Page 1220: ...Fig 7C 7 G Truck Clutch Controls...
Page 1221: ...CLUTCH 7C 7 Fig 7C 8 P Truck Clutch Controls...
Page 1234: ...7E 2 TRANSFER CASE Fig 7E 1 Model 208 Transfer Case Cross Section...
Page 1252: ...7E 20 TRANSFER CASE Fig 7E 39 Transfer Case Attachment Typical...
Page 1278: ...8A 16 ELECTRICAL BODY AND CHASSIS Fig 8A 11 License Plate Lamps C K Series...
Page 1280: ...8A 18 ELECTRICAL BODY AND CHASSIS VIEW A VIEW B Fig 8A 15 CK Series Rear Lamp W iring...
Page 1281: ...ELECTRICAL BODY AND CHASSIS 8A 19 Fig 8A 16 CK Series Auxiliary W iring...
Page 1290: ...8B 8 ELECTRICAL AND WIRING Fig 8B 13 Seat Belt Reminder System Schematic...
Page 1292: ......
Page 1346: ...8C 54 INSTRUMENT PANEL AND GAGES Fig 8C 46 CK Series W iring 3 of 29...
Page 1351: ...INSTRUMENT PANEL AND GAGES 8C 59 SUBURBAN Fig 8C 51 CK Series W iring 8 of 29...
Page 1364: ...8C 72 INSTRUMENT PANEL AND GAGES Fig 8C 64 CK Series W iring 21 of 29...
Page 1365: ...INSTRUMENT PANEL AND GAGES 8C 73 CAB CRFW CAB CHASSIS Fig 8C 65 CK Series W iring 22 of 29...
Page 1366: ...8C 74 INSTRUMENT PANEL AND GAGES Fig 8C 66 CK Series W iring 23 of 29...
Page 1374: ...8C 82 INSTRUMENT PANEL AND GAGES Fig 8C 74 G Series W iring 2 of 19...
Page 1375: ...INSTRUMENT PANEL AND GAGES 8C 83 Fig 8C 75 G Series W iring 3 of 19...
Page 1376: ...8C 84 INSTRUMENT PANEL AND GAGES Fig 8C 76 G Series W iring 4 of 19...
Page 1379: ...INSTRUMENT PANEL AND GAGES 8C 87 Fig 8C 79 G Series W iring 7 of 19...
Page 1383: ...INSTRUMENT PANEL AND GAGES 8C 91 Fig 8C 83 G Series W iring 11 o f 19...
Page 1384: ...8C 92 INSTRUMENT PANEL AND GAGES BUS BARGWO Fig 8C 84 G Series W iring 12 of 19...
Page 1390: ...8C 98 INSTRUMENT PANEL AND GAGES Fig 8C 90 G Series W iring 18 of 19...
Page 1391: ...INSTRUMENT PANEL AND GAGES 8C 99 Fig 8C 91 G Series W iring 19 of 19...
Page 1392: ...8C 100 INSTRUMENT PANEL AND GAGES Fig 8C 92 P Series W iring 1 of 11...
Page 1393: ...INSTRUMENT PANEL AND GAGES 8C 101 Fig 8C 93 P Series W iring 2 of 11...
Page 1396: ...8C 104 INSTRUMENT PANEL AND GAGES Fig 8C 96 P Series W iring 5 of 11...
Page 1399: ...INSTRUMENT PANEL AND GAGES 8C 107 Fig 8C 99 P Series W iring 8 of 11...
Page 1401: ...INSTRUMENT PANEL AND GAGES 8C 109 START RUN OF LOCK ACC Fig 8C 101 P Series W iring 10 of 11...
Page 1415: ...ACCESSORIES 9 13 RADIO NOISE BLOWER MOTOR Fig 9 6R Radio Diagnosis Chart B...
Page 1416: ...9 14 ACCESSORIES D E A D R A D IO A M R A D IO I Fig 9 7R Radio Diagnosis Chart C...
Page 1417: ...ACCESSORIES 9 15 DEAD RADIO AM FM RADIO Fig 9 8R Radio Diagnosis Chart D...
Page 1435: ...t f l i t 1...